Desde la Edad de Piedra, la Edad del Bronce y la Edad del Hierro, el desarrollo de los materiales ha contribuido a ampliar los límites de los esfuerzos y logros humanos. En el siglo XXI, las exigencias de industrias como la aeroespacial y la automovilística fuerzan los límites de las propiedades de los materiales a cotas cada vez más extremas.
Es inherente a la naturaleza humana anticiparse a aquello que deseamos sea posible. La industria de la automoción es un claro ejemplo de ello. Cuando Ford publicó su lista de materiales para los vehículos del futuro, ésta incluía materiales que hasta podrían llegar a salvar vidas. El profesor Pim van der Jagt, director técnico ejecutivo del departamento de investigación e ingeniería avanzada de Ford, incluyó materiales tales como un nuevo tipo de acero tres veces más resistente que el acero actual; una espuma plástica capaz de estabilizar las estructuras durante los accidentes; y composites nano-reforzados que reducen drásticamente el peso a la vez que aumentan la resistencia. (Fuente: http://articles.sae.org/12297/)
En la edad moderna, la industria aeroespacial también busca materiales más tenaces, ligeros y resistentes al calor, que reduzcan las emisiones y los costes del combustible, y que al mismo tiempo permitan desplazarse a mayor velocidad. Hasta la fecha, los composites han sido el material más demandado de esta industria. Según la Dra. Eleanor Merson, especialista en investigación de composites, «Hace treinta años, un cinco por ciento del avión estaba hecho de composites; ahora, un 50% de un avión comercial, como el Dreamliner, está hecho de materiales de composite».
Aunque sólo pesan una quinta parte de lo que pesa el acero, los composites de fibra de carbono son más resistentes. El Dreamliner, por ejemplo, tiene composites de fibra de carbono en sus alas, cola, puertas, fuselaje e interior, lo cual se traduce en un avión más ligero. En las aeronaves, cada kilo cuenta. Los expertos estiman que un avión comercial un kilogramo (2,2 libras) más ligero puede reducir su coste operativo entre 2.000 y 3.000 euros al año.
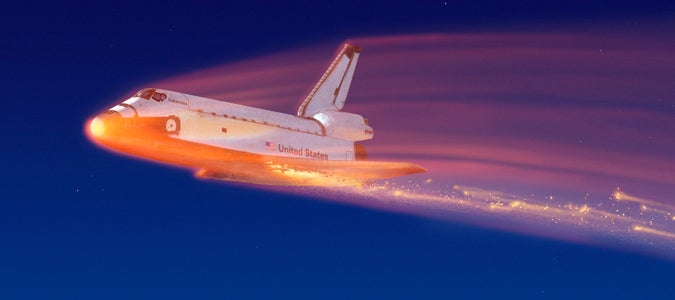
Un Lamborghini hecho de composites
Los composites aparecen con creciente frecuencia en vehículos, álabes de turbinas eólicas y otros productos. Por ejemplo, el BMW eléctrico i3 está casi totalmente hecho de composites. BMW afirma que esta reducción del peso permite que el vehículo se desplace hasta 160 kilómetros en una única carga. El Veneno Roadster de Lamborghini está hecho de múltiples piezas de composite que reducen su peso y le permiten acelerar de 0 a 100 km/hora en 2,9 segundos. Ahora, producir composites es más barato y el número de empresas que los fabrican es cada vez mayor; pero producir composites de alta calidad aún exige temperaturas elevadas, entornos extremadamente limpios y procesos laboriosos. Además, mecanizar estos composites de alta calidad supone un reto incluso mayor.
«Mecanizar y, en especial, taladrar composites es un reto enorme», explica Merson, investigador de composites para Sandvik Coromant. «Una aeronave tiene miles de agujeros y el material es muy abrasivo; las fibras de carbono desgastan las brocas muy rápidamente».
En el futuro, probablemente se aumente la resistencia de los composites mediante fibras desarrolladas a nanoescala. Además, se prevé que los científicos podrán crear soluciones cuasi perfectas a nivel atómico. Especialistas de la empresa química alemana, Altana AG, afirman que los nanotubos de carbono pueden ser 400 veces más resistentes que el acero o el aluminio y 20 veces más resistentes que las fibras de carbono convencionales.
Grafeno en smartphones
Los materiales como el grafeno y los cuasicristales, cuyos descubridores recibieron Premios Nobel, prometen una tenacidad mucho mayor y pueden revolucionar el diseño industrial. No obstante, su aplicación industrial general aún está lejos.
El año pasado, una empresa china introdujo granos de grafeno en teléfonos móviles para mejorar su conductividad. También se han moldeado esquirlas de cuasicristal en sartenes e instrumentos quirúrgicos metálicos para aumentar su durabilidad. Aunque no se divisan avances industriales importantes, se están haciendo grandes inversiones en la investigación del grafeno. El grafeno es 200 veces más resistente que el acero y es el material más fino del mundo (1 millón de veces más fino que el pelo humano). A su vez, los investigadores de las empresas y universidades se centran en mejorar las técnicas y los materiales existentes.
Las aleaciones de aluminio de bajo peso han remplazado al acero de gran resistencia en sistemas parachoques, componentes de anillos de tope y vigas de intrusión. Y, en los motores aeronáuticos, las aleaciones súper duras, resistentes a temperaturas extremas, pueden ayudar a mejorar la conversión de la energía y reducir los costes del combustible.
Recubrimientos más duros que el acero
La deposición física de vapor (PVD por sus siglas en inglés) y la deposición química de vapor (CVD por sus siglas en inglés) son procesos empleados para recubrir objetos con una película extremadamente fina y resistente a las altas temperaturas. Estas técnicas empezaron a utilizarse en los años 80 y siguen empleándose para dispositivos mecánicos, ópticos y electrónicos.
Sandvik Coromant usa estos métodos para endurecer las superficies de sus plaquitas. El núcleo de la plaquita está hecho de metal duro, compuesto principalmente de carburo de tungsteno y cobalto.
«Añada una capa de dos a 10 micras de PVD y la vida útil de la plaquita se multiplica por 100», explica el Dr. Mats Ahlgren, especialista en física material y jefe del departamento de PVD de Sandvik Coromant. «Los clientes no sólo pueden utilizar las plaquitas durante más tiempo, sino que también pueden aumentar su productividad al trabajar con ellas a mayor avance y velocidad».
Sus investigaciones actuales se centran en conseguir recubrimientos más tenaces que satisfagan la demanda de materiales duraderos.«En los últimos años, hemos desarrollado nuestra capacidad de controlar el proceso de creación de los recubrimientos nuevos», dice Ahlgren. «Podemos ver la estructura en microscopios, prácticamente a nivel atómico, lo cual nos ayuda a analizar las nuevas soluciones antes de implementarlas».
En 2013, Sandvik Coromant patentó su recubrimiento de CVD Inveio™. Gracias a sus cristales desarrollados para crecer en una misma dirección, Inveio supuso un paso de gigante en términos de durabilidad y dureza.
Al usar materiales más tenaces, ya no es tan necesario utilizar componentes robustos de gran volumen en una misma estructura. Los diseñadores son cada vez más selectivos en la elección de los materiales para las diferentes piezas de los automóviles o aeronaves y algunas de estas piezas no tienen por qué ser tan resistentes. Esta es la filosofía de Ian Scoley, antiguo jefe del departamento de diseño industrial de Airbus, donde se dedicaba al diseño de las cabinas aeroespaciales. En la actualidad, Scoley, jefe de diseño industrial en C&D Zodiac, dice inspirarse en los hueso de las aves. «Son fuertes en los puntos necesarios, pero ligeros y abiertos donde requieren flexibilidad», afirma.
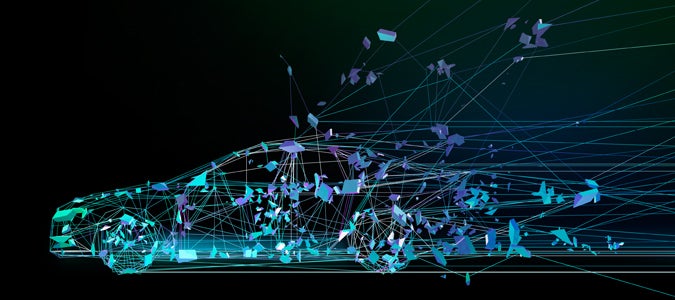
El auge del reciclado
Aunque los aviones y los vehículos emplean menos energía y producen menos emisiones gracias a los nuevos diseños y materiales, el reciclado también está adquiriendo más importancia. Muchos composites, por ejemplo, están hechos de aglomerantes adhesivos, difíciles de separar y reutilizar, pero las aleaciones de aluminio más recientes de la industria de la automoción se crean teniendo en cuenta su futuro reciclado.
De hecho, el reciclado se ha convertido en una fuerza motriz de la fabricación automovilística. Los gobiernos europeos exigen que los vehículos se construyan de tal modo que un 85% de sus materiales puedan reciclarse. «Las empresas automovilísticas estudian todas las partes del coche para satisfacer esas exigencias», explica Arjen Bongard, analista de la industria automovilística alemana.
El reto del reciclado está generando soluciones muy imaginativas. Ford ha empezado a utilizar paja de trigo y productos de soja en su diseño interior y está investigando el posible uso de cáscaras de coco, zanahorias y plásticos con base de maíz para los materiales. El plan de la empresa es producir interiores 100% biodegradables.
«Encontrar materiales alternativos es importante, al igual que crear procesos de sustitución y reciclado rentables», afirma la Dra. Anna Hultin Stigenberg, especialista líder en I+D de Sandvik Coromant. Hasta hace poco, Stigenberg presidía el comité directivo internacional de la Knowledge and Innovation Community for Raw Materials; una iniciativa que aúna más de 100 empresas y centros de investigación para promover el desarrollo de materiales sostenibles.
A nivel atómico
¿Por qué conformarse con materiales que ya existen? Los humanos han desarrollado la capacidad de crear materiales completamente nuevos, con propiedades específicas.
«Con la ayuda de los microscopios modernos y cálculos computacionales, cada vez somos mejores en el diseño de nuevos materiales a nivel atómico», afirma Hultin Stigenberg.
Desde el fin de la Edad del Bronce, 550 AEC, ningún otro material específico ha definido un periodo en la historia de la humanidad. Muchos académicos dicen que vivimos en la edad del plástico, pero, en el futuro, nuestra época podría conocerse como la edad de los nuevos materiales, y sus efectos en la evolución humana pueden ser mucho mayores de lo que ahora imaginamos.