Drehen - Erzielung einer hohen Bauteilqualität
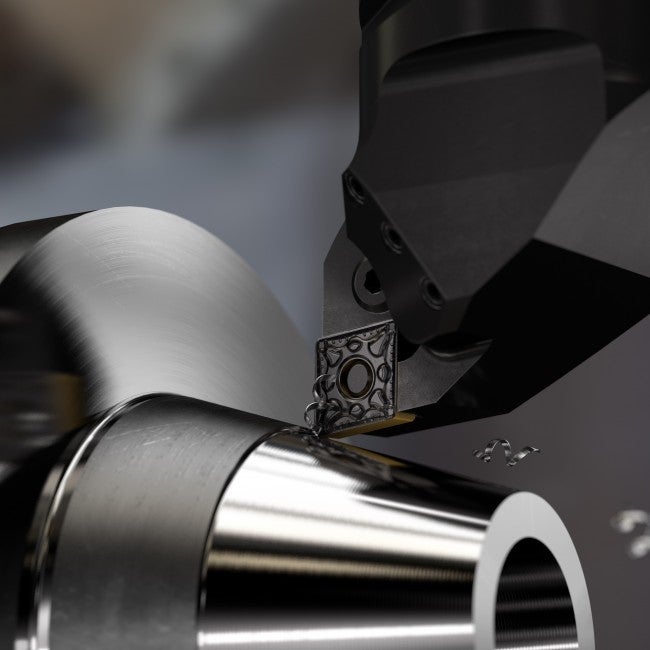
Zum Drehen hochqualitativer Bauteile ist die Spankontrolle einer der wichtigsten Faktoren, die zu beachten sind. Wählen Sie die passenden Schnittdaten und folgen Sie unseren Anwendungstipps für gute Bauteilqualität.
Erfolgreiche Spankontrolle
Spankontrolle ist einer der Schlüsselfaktoren beim Drehen. Es gibt drei Arten von Spanbruch:
- Selbst brechende Späne (z. B. Grauguss)
- Spanbruch am Werkzeug
- Spanbruch am Werkstück
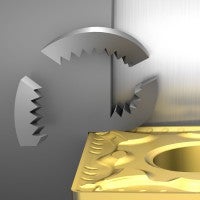
Selbstbrechend
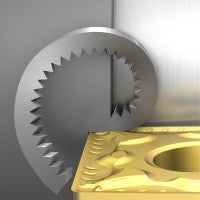
Spanbruch am Werkzeug
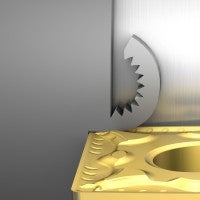
Spanbruch am Werkstück
Faktoren, die den Spanbruch beeinflussen
- Plattengeometrie: Je nach Spanraumweite und Ausführung der Mikro-/Makrogeometrie ist der Span offen oder gestaucht
- Eckenradius: Kleinerer Eckenradius bewirkt eine bessere Spankontrolle als ein größerer Eckenradius
- Einstellwinkel (Eintrittswinkel): Je nach Winkel erfolgt die Spanableitung auf unterschiedlichem Weg, entweder gegen eine Schulter oder von einer Schulter weg
- Schnitttiefe: In Abhängigkeit vom Werkstoff wirkt sich eine höhere Schnitttiefe auf den Spanbruch aus. Dies führt zu höheren Schnittkräften für Spanbruch und -abfuhr
- Vorschub: Ein höherer Vorschub erzeugt üblicherweise stabilere Späne. Dadurch können in einigen Fällen Spanbruch und -kontrolle unterstützt werden
- Schnittgeschwindigkeit: Eine höhere Schnittgeschwindigkeit kann den Spanbruch beeinflussen
- Werkstoff: Kurzspanende Werkstoffe (z. B. Guss) sind in der Regel leicht zerspanbar. Bei Werkstoffen mit hoher mechanischer Festigkeit und Kriechfestigkeit
(Verformungsneigung unter Belastung, z. B. Inconel) spielt der Spanbruch eine wichtigere Rolle
Schnittdaten für Drehbearbeitungen
Berücksichtigen Sie bei der Wahl der richtigen Schnittgeschwindigkeiten und Vorschübe für die Drehbearbeitung immer Maschine, Werkzeug, Wendeschneidplatte und Werkstoff.
- Mit niedrigem Vorschub beginnen, um Wendeschneidplattensicherheit und hohe Oberflächengüte zu erzielen, anschließend den Vorschub steigern, um den Spanbruch zu verbessern
- Die Schnitttiefe sollte größer als der Eckenradius sein. So wird die radiale Ablenkung der Wendeschneidplatte minimiert, was bei der Innenbearbeitung entscheidend ist
- Eine zu niedrige Schnittgeschwindigkeit resultiert in einer unzureichenden Standzeit. Verwenden Sie stets die empfohlene Schnittgeschwindigkeit, vc m/min (Fuß/min)
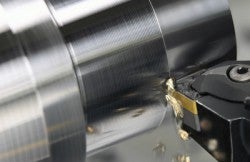
Verbessern Sie die Bauteilqualität mithilfe von Kühlschmierstoff
Bei richtiger Anwendung erhöht Kühlschmierstoffzufuhr die Prozesssicherheit und verbessert die Werkzeugleistung sowie die Bauteilqualität. Beim Einsatz von Kühlschmierstoffzufuhr ist Folgendes zu berücksichtigen:
- Für Schlichtanwendungen werden ausdrücklich Werkzeuge mit Präzisions-Kühlschmierstoffzufuhr empfohlen
- Der erforderliche Kühlschmierstoffdruck, um die Späne zu brechen ist abhängig vom Düsendurchmesser (Austritt), vom zerspanten Werkstoff und dem Vorschub
- Der erforderliche Durchsatz des Kühlschmierstoffs richtet sich nach dem Druck und den Kühlschmierstoffbohrungen
- Bei mittlerer Bearbeitung und beim Schruppen wird der Einsatz von unterer Kühlschmierstoffzufuhr empfohlen
- Beim Schlichten sollten sowohl Hochpräzisions-Kühlschmierstoff als auch eine untere Kühlschmierstoffzufuhr eingesetzt werden.
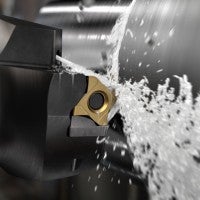
Bewältigung von Herausforderungen durch korrekte Anwendung von Kühlschmierstoff
- Schwierige Spankontrolle: Einsatz von oberer Kühlschmierstoffzufuhr
- Probleme bei der Maßgenauigkeit: Normalerweise durch hohe Temperatur verursacht – sowohl obere als auch untere Kühlschmierstoffzufuhr und höchstmöglichen Druck verwenden
- Schlechte Oberflächenqualität: Einsatz von oberer Kühlschmierstoffzufuhr, wenn Fehler durch Spanstau verursacht wurde
- Unberechenbare Standzeit beim Schruppen: Nur Einsatz von unterer Kühlschmierstoffzufuhr
- Unberechenbare Standzeit beim Schlichten: Einsatz von oberer und unterer Kühlschmierstoffzufuhr
- Schlechte Spanabfuhr bei der Innenbearbeitung: Einsatz von oberer und unterer Kühlschmierstoffzufuhr und höchstmöglichem Druck
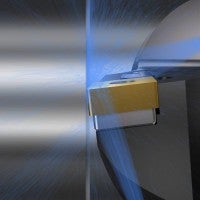
Drehen - Anwendung von Kühlschmierstoff und Schneidflüssigkeit
Drehen - Erzielung einer hohen Oberflächengüte
Allgemeine Regeln für eine hohe Oberflächengüte:
- Die Oberflächengüte lässt sich häufig durch Einsatz höherer Schnittgeschwindigkeiten verbessern
- Die Plattengeometrie (neutrale, positive und negative Spanwinkel, sowie positive Freiwinkel) beeinflusst die Oberflächengüte
- Die Wahl der Wendeschneidplattensorte hat auch Einfluss auf die Oberflächengüte
- Bei auftretenden Vibrationen einen kleineren Eckenradius wählen
Wiper-Wendeschneidplatte
Wiper-Wendeschneidplatten erlauben Drehbearbeitungen mit hohen Vorschubraten - ohne Beeinträchtigung der hohen Oberflächengüte oder Spanbildungsfähigkeit.
Als allgemeine Richtlinie gilt: Doppelter Vorschub – gleiche Oberflächengüte Gleicher Vorschub - doppelt so hohe Oberflächengüte
Der Wiper-Effekt, der die Oberfläche glättet, während sich die Wendeschneidplatte entlang des Bauteils bewegt, wurde hauptsächlich zum geradlinigen Längs- und Plandrehen entwickelt.
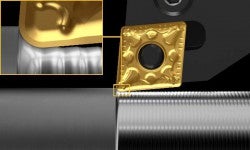
Standard-Radius
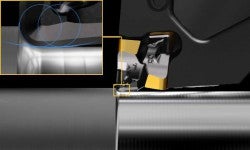
Wiper-Radius
Vergleich einer Standard-Wendeschneidplatte mit einer Wiper-Wendeschneidplatte, basierend auf Vorschub
Hinweis! Alle Werte für den Standardradius sind theoretisch berechnet. Die Werte für den Wiper-Radius basieren auf Versuchswerten in legiertem Stahl.
Vorschub mm (Zoll) | Standard RE 0.4 mm (0.016 Zoll) Ra µm (µZoll) | Wiper (-WF/-WM) RE 0.4mm (0.016 Zoll) Ra µm (µZoll) | Standard RE 0.8 mm (0.031 Zoll) Ra µm (µZoll) | Wiper (-WMX) RE 0.8 mm (0.031 Zoll) Ra µm (µZoll) |
0.07 (0.003) | 0.31 (12.4) | 0.30 (12.0) | - | – |
0.10 (0.004) | 0.63 (25.2) | 0.32 (12.8) | 0.31 (12.4) | - |
0.12 (0.005) | 0.90 (36.0) | 0.45 (18.0) | 0.45 (18.0) | - |
0.15 (0.006) | 1.41 (56.4) | 0.70 (28.0) | 0.70 (28.0) | 0.25 (10.0) |
0.18 (0.007) | 2.03 (80.8) | 1.00 (40.0) | 1.00 (40.4) | 0.30 (12.0) |
0.20 (0.008) | 2.50 (100.0) | 1.25 (50.0) | 1.25 (50.0) | 0.35 (14.0) |
0.22 (0.009) | 3.48 (139.2) | 1.74 (69.6) | 1.74 (69.6) | 0.40 (16.0) |
0.25 (0.010) | - | - | 2.25 (90.0) | 0.45 (18.0) |
0.28 (0.011) | - | - | 2.82 (112.8) | 0.50 (20.0) |
0.30 (0.012) | - | - | 3.23 (129.2) | 0.55 (22.0) |
0.35 (0.014) | - | - | 4.40 (176.0) | 0.60 (24.0) |
0.40 (0.016) | - | - | 5.75 (230.0) | 0.70 (28.0) |
0.45 (0.018) | - | - | 8.54 (341.6) | 1.1 (44.0) |
0.50 (0.020) | - | - | 10.55 (422.0) | 1.3 (51.0) |
Vorschub mm (Zoll) | Standard RE 1.2 mm (0.047 Zoll) Ra µm (µZoll) | Wiper (-WMX) RE 1.2mm (0.047 Zoll) Ra µm (µZoll) | Standard RE 1.6 mm (0.063 Zoll) Ra µm (µZoll) | Wiper (-WMX) RE 1.6 mm 1) (0.063 Zoll) Ra µm (µZoll) |
0.15 (0.006) | 0.47 (18.8) | - | - | – |
0.18 (0.007) | 0.68 (27.2) | - | - | - |
0.20 (0.008) | 0.83 (33.3) | 0.3 (12.0) | 0.63 (25.2) | - |
0.22 (0.009) | 1.16 (46.4) | 0.3 (12.0) | 0.87 (34.8) | - |
0.25 (0.010) | 1.50 (60.0) | 0.4 (16.0) | 1.12 (44.8) | 0.3 (12.0) |
0.28 (0.011) | 1.88 (75.2) | 0.4 (16.0) | 1.41 (56.4) | 0.35 (14.0) |
0.30 (0.012) | 2.16 (86.4) | 0.4 (16.0) | 1.62 (64.8) | 0.4 (16.0) |
0.35 (0.014) | 2.93 (117.2) | 0.5 (20.0) | 2.20 (88.0) | 0.4 (16.0) |
0.40 (0.016) | 3.83 (153.2) | 0.65 (26.0) | 2.88 (115.2) | 0.4 (16.0) |
0.45 (0.018) | 5.70 (228.0) | 0.85 (34.0) | 4.27 (170.8) | 0.5 (20.0) |
0.50 (0.020) | 7.03 (281.2) | 1.15 (46.0) | 5.27 (210.8) | 0.7 (28.0) |
0.55 (0.022) | 8.51 (340.4) | 1.2 (48.0) | 6.38 (255.2) | 0.9 (36.0) |
0.60 (0.024) | 10.13 (405.2) | 1.3 (52.0) | 7.59 (303.6) | 1.05 (42.0) |
0.65 (0.026) | - | - | 8.91 (356.4) | 1.25 (50.0) |
0.70 (0.028) | - | - | 10.31 (413.6) | 1.3 (52.0) |
0.85 (0.033) | - | - | 15.24 (609.6) | 1.9 (76.0) |
0.90 (0.035) | - | - | 17.09 (683.0) | 2.1 (84.0) |
- Werte für 1.6 mm (0.06 Zoll) Radius basieren auf DNMX-Wendeschneidplatte
Suchen Sie Werkzeugempfehlungen?
Hier finden Sie unsere Zerspanungswerkzeuge chevron_right
Brauchen Sie Beratung?
Stellen Sie uns eine Frage chevron_right
Was es sonst noch über die Grundlagen unserer Metallzerspanung zu lernen gibt?
Registrieren Sie sich für unser kostenloses E-Learning Programm chevron_right
Anwendungstipps zum Außendrehen
Vibrationsanfällige Bauteile
Zerspanung in einem Durchgang (z. B. ein Rohr)
Es wird die Bearbeitung in einem Durchgang empfohlen, um die Schnittkräfte in axialer Richtung gegen das Futter/die Spindel zu leiten.
Beispiel:
Außendurchmesser (AD) von 25 mm (0.984 Zoll)
Innendurchmesser (ID) von 15 mm (0.590 Zoll)
Schnitttiefe ap = 4.3 mm (0.169 Zoll)
Resultierende Rohrwanddicke = 0.7 mm (0.028 Zoll)
AD = 25 mm (0.984 Zoll) | ap 4.3 mm (0.169 Zoll) |
![]() | ID = 15 mm (0.590 Zoll) |
Ein Einstellwinkel von fast 90° (Eintrittswinkel 0°) kann zur Ableitung der Schnittkräfte in axialer Richtung eingesetzt werden. Das führt auch zu einem minimalen Biegemoment des Bauteils.
Zerspanung in zwei Durchgängen
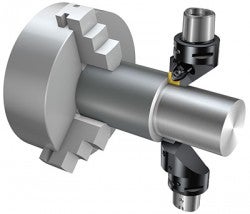
Die synchronisierte Bearbeitung mit oberem und unterem Revolver wird radiale Schnittkräfte ausgleichen und Vibrationen sowie Durchbiegen des Bauteils vermeiden.
Schlanke/dünnwandige Bauteile
Bei der Bearbeitung schlanker/dünnwandiger Bauteile ist Folgendes zu berücksichtigen:
- Einstellwinkel von fast 90° (Eintrittswinkel 0°) wählen. Bereits eine kleine Änderung (von einem 91/-1°- auf einen 95/-5°-Winkel) beeinflusst die Richtung der Schnittkraft während der Bearbeitung
- Die Schnitttiefe ap, sollte größer als der Eckenradius (RE) sein. Ein großer ap Wert steigert die Axialkraft Fz und verringert die radiale Schnittkraft Fx, wodurch Vibrationen hervorgerufen werden
- Verwendung einer Wendeschneidplatte mit scharfer Schneide und kleinem Eckenradius (RE) für niedrige Schnittkräfte
- Verwendung einer Cermet oder PVD-Sorte für Verschleißfestigkeit und Schneidkantenstabilität, die für diese Art von Anwendung erforderlich sind
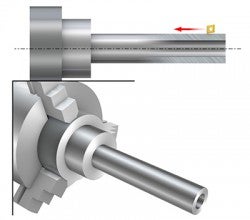
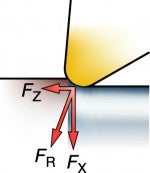
Schulterbearbeitung/Drehen gegen eine Schulter
Folgen Sie den Schritten 1-5, um eine Beschädigung der Schneidkante zu vermeiden. Diese Methode ist sehr vorteilhaft mit CVD-beschichteten Wendeschneidplatten und senkt Schneidkantenbruch erheblich.
Stufen 1-4:
Der Abstand jeder Stufe (1-4) sollte der gleiche wie der Vorschub sein, um Spanstau zu vermeiden.
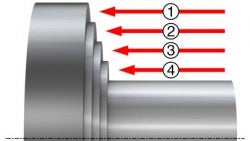
Stufe 5:
Der letzte Schnitt sollte vertikal vom großen zum kleinen Durchmesser erfolgen.
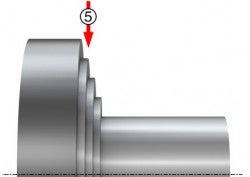
Probleme können auch durch lange Späne bei Plandrehen an Bauteilschultern vom kleinen zum großen Durchmesser entstehen. Das Wechseln des Werkzeugweges kann die Spanrichtung umkehren und das Problem lösen.
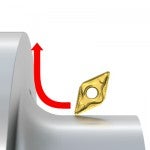
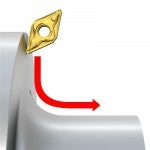
Plandrehen
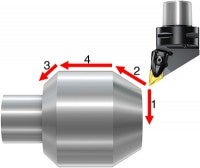
Zuerst die Planbearbeitung (1), dann die Fase (2). Wenn möglich und falls es die geometrischen Voraussetzungen am Bauteil erlauben, mit der Fase (3) beginnen. Das Längsdrehen (4) ist der letzte Schritt und die Wendeschneidplatte hat einen weichen Ein- und Austritt bei der Bearbeitung.
Die Planbearbeitung sollte die erste Anwendung sein, um am Bauteil den Referenzpunkt für den nächsten Durchgang festzulegen.
Gratbildung ist ein häufiges Problem am Ende des Schneidvorgangs (beim Austritt aus dem Werkstück). Durch einen Bauteilaustritt über eine Rampe oder einen Radiuas, kann die Gratbildung minimiert oder sogar ganz vermieden werden.
Eine Fase am Bauteil sorgt für einen reibungslosen Eintritt der Schneidkante (sowohl bei der Planbearbeitung als auch beim Längsdrehen).
Schnittunterbrechungen

Bei Schnittunterbrechung:
- In Anwendungen mit schnellen Unterbrechungen, z. B. an Sechskantstangen, eine PVD-Sorte für bessere Schneidkantenzähigkeit verwenden
- In Anwendungen mit großen Bauteilen und schwerer Schnittunterbrechung eine zähe CVD-Sorte für zusätzliche Gesamtzähigkeit verwenden
- Einen stabilen Spanbrecher für zusätzliche Stabilität gegen Schneidkantenausbrüche verwenden.
- Zur Vermeidung von Kammrissen ist es empfehlenswert, die Kühlschmierstoffzufuhr abzustellen.
Fertigbearbeitung des Bauteils mit Freistich
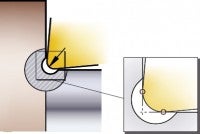
Beim Längs- und Plandrehen den größtmöglichen Eckenradius (RE) verwenden für:
- Stabile Schneidkante, höhere Zuverlässigkeit
- Gute Oberflächenqualität
- Möglichkeit hoher Vorschübe
Nicht die Breite des Freistichs überschreiten. Der Freistich muss als letzter Arbeitsschritt erfolgen um eventuell auftretenden Grat zu entfernen.
Anwendungstipps zum Innendrehen
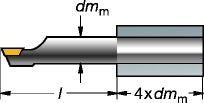
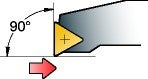
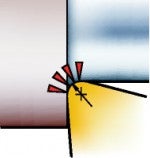
- Größten Bohrstangendurchmesser wählen und gleichzeitig sicherstellen, dass genügend Raum für Spanabfuhr zwischen der Bohrstange und Bohrung vorhanden ist
- Stellen Sie sicher, dass die Spanabfuhr im Verhältnis zu den verwendeten Schnittdaten ausreichend ist und der richtige Spantyp erzeugt wird
- Wählen Sie den kleinsten Überhang und stellen Sie sicher, dass die Länge des Drehadapters die empfohlenen Einspannlängen ermöglicht Die Einspannlänge sollte nie kleiner als 3 x Stangendurchmesser sein
- Verwenden Sie bei der Bearbeitung von vibrationsanfälligen Bauteilen schwingungsgedämpfte Bohrstangen
- Wählen Sie einen Einstellwinkel von fast 90° (Eintrittswinkel 0°) zur Ableitung der Schnittkräfte in axialer Richtung. Der Einstellwinkel beim Innendrehen sollte nicht unter 75° (Eintrittswinkel 0°) liegen
- Die Wendeschneidplatte sollte vorzugsweise über eine positive Grundform und eine positive Wendeschneidplattengeometrie verfügen, um die Werkzeugabdrängung zu minimieren
- Einen Eckenradius wählen, der größer als die Schnitttiefe ist
- Ein unzureichender Schneideneingriff kann zu Reibung und verstärkten Vibrationen während der Bearbeitung führen. Wählen Sie eine Schnitttiefe die größer als der Eckenradius ist.
- Ein übermäßiger Spanquerschnitt (hohe Schnitttiefe und/oder hoher Vorschub) kann durch Werkzeugablenkung zu erhöhten Vibrationen führen
- Wendeschneidplatten mit dünnen Beschichtungen oder unbeschichtete Wendeschneidplatten sorgen normalerweise für geringere Schnittkräfte als Wendeschneidplatten mit hoher Schichtdicke. Dies ist besonders wichtig bei einem großen Durchmesser/Längenverhältnis des Werkzeugs. Eine scharfe Schneidkante verbessert normalerweise die Qualität der Bohrung, indem sie Vibrationen minimiert
- Eine Geometrie mit offenem Spanbrecher wirkt sich häufig vorteilhafter auf das Innendrehen aus
- Eine Wendeschneidplattensorte mit höherer Zähigkeit kann in einigen Situationen verwendet werden, wenn die Gefahr von Spanstau oder Vibrationsneigung besteht
- Berücksichtigen Sie alternative Werkzeugwege, wenn die Spanbildung verbessert werden muss
Suchen Sie Werkzeugempfehlungen?
Hier finden Sie unsere Zerspanungswerkzeuge chevron_right
Brauchen Sie Beratung?
Stellen Sie uns eine Frage chevron_right
Was es sonst noch über die Grundlagen unserer Metallzerspanung zu lernen gibt?
Registrieren Sie sich für unser kostenloses E-Learning Programm chevron_right
Anwendungstipps zum Hartdrehen
Zusätzlich zu den allgemeinen Empfehlungen für das Drehen gibt es weitere Schlüsselfaktoren, die beim Hartdrehen zu berücksichtigen sind (wenn der Produktionsprozess eine eigene Bauteilvorbereitung vor der Härtung enthält):
- Gratbildung vermeiden
- Enge Maßtoleranzen einhalten,
- Fasen und Radienbearbeitung im weichen Zustand
- Abrupte Ein- und Austritte vermeiden
- Ein- oder Austritt mittels Radienprogrammierung
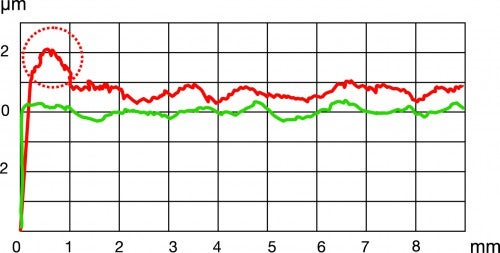
Oberflächenmessungen
X-Achse: Länge des Merkmals
Y-Achse: Durchmesserabweichung
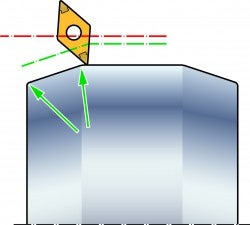
Kritische Oberfläche
Aufspannung
- Eine stabile Maschine, Werkzeugaufspannung und -ausrichtung sind entscheidend
- Bei Bauteilen, die nur am Ende gespannt werden, ist ein Länge-Durchmesser-Verhältnis bis 2:1 akzeptabel. Wird das Bauteil zusätzlich vom Reitstock unterstützt, kann dieses Verhältnis vergrößtert werden
- Beachten, dass eine wärmesymmetrische Spindel- und Reitstockausführung zusätzlich zur hohen Maßgenauigkeit beiträgt.
- Coromant Capto® System verwenden
- Zur Maximierung der Stabilität des Systems, Überhänge minimieren
- Für Innendrehanwendungen Hartmetall-Bohrstangen und Silent Tools in Betracht ziehen
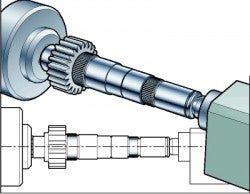
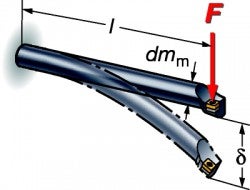
Wendeschneidplatten-Mikrogeometrie
Zwei typische Schneidkantenausführungen für CBN-Wendeschneidplatten sind Typ-S und Typ-T.
- Typ S: Verfügt über höchste Schneidkantenstabilität. Bietet besten Widerstand gegen Mikroausbrüche und gleichbleibende Oberflächenqualität.
- Typ T: Für beste Oberflächengüte bei kontinuierlichen Schnitten und minimierte Gratbildung bei Schnittunterbrechungen. Geringe Schnittkräfte.
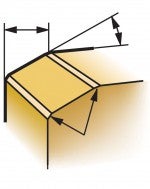
Typ S
Gefast mit leichter Kantenverrundung
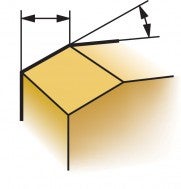
Typ T
Gefast ohne Kantenverrundung
Wendeschneidplatte - Eckengeometrie
- Bei stabilen Bedingungen stets eine Wiper-Geometrie für beste Oberflächengüte verwenden.
- Wendeschneidplatte mit kleinem Einstellwinkel wählen, wenn hohe Produktivität erforderlich ist.
- Eine normale Radius-Wendeschneidplatte sollte nur bei instabilen Bedingungen eingesetzt werden (schlanke Bauteile etc.).
Nass- oder Trockenbearbeitung
Die Hartbearbeitung ohne Kühlschmierstoffzufuhr ist die ideale Situation. Sowohl CBN als auch Keramik-Wendeschneidplatten halten hohen Temperaturen stand und eliminieren so Kosten und Probleme in Zusammenhang mit Kühlschmierstoff.
Bei einigen Anwendungen ist dennoch Kühlschmierstoff erforderlich, etwa um die Wärmestabilität des Bauteils zu kontrollieren. In diesen Fällen sollte während der gesamten Drehanwendung ein kontinuierlicher Kühlschmierstofffluss sichergestellt werden.
Generell wird die bei der Bearbeitung erzeugte Wärme zu (80%) auf den Span und jeweils zu (10%) auf das Bauteil und die Wendeschneidplatte (10%) verteilt. Dies zeigt die Bedeutung einer korrekten Spanabfuhr aus der Schnittzone.
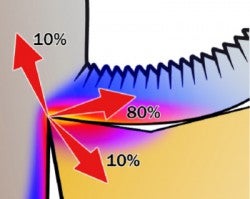
Schnittdaten und Verschleiß
Hohe Wärme in der Schnittzone führt zu reduzierten Schnittkräften. Daher kann eine zu geringe Schnittgeschwindigkeit (weniger Hitze) Wendeschneidplattenbruch verursachen.
Kolkverschleiß beeinflusst die Plattenstabilität, aber nicht in erster Linie die Oberflächengüte der bearbeitenden Bauteile. Im Gegensatz dazu wirkt sich Freiflächenverschleiß graduell auf die Maßtoleranz aus.
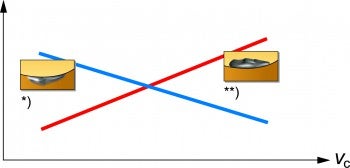
Standzeitanteil
*) Freiflächenverschleiß **) Kolkverschleiß
Kriterien für einen Wendeschneidplattenwechsel
Eine vorab definierte Oberflächengüte (B) ist ein häufiges und praktisches Kriterium für einen Wendeschneidplattenwechsel. Die Oberflächengüte wird automatisch in einer eigens dafür vorgesehenen Messtation gemessen und ein Wert für eine spezifische Oberflächengüte festgelegt.
Setzen Sie für einen optimierten und stabilen Prozess eine vorab definierte Anzahl an Bauteilen (A) als Kriterium für einen Plattenwechsel fest. Dieser Wert sollte 10–20% weniger betragen, als die bei einem optimierten Bearbeitungsprozess bei durchschnittlicher Standzeit erzielte Anzahl. Die exakte Zahl muss für jeden Fall individuell festgelegt werden.
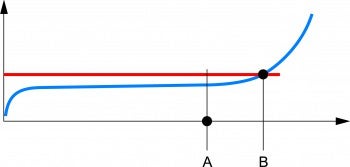
A: Vorbestimmte Anzahl an Bauteilen
B: Vorbestimmte Oberflächengüte
X-Achse: Anzahl an Bauteilen
Y-Achse: Oberflächengüte
Blaue Linie: Wendeschneidplattenverschleiß
Rote Linie: Maximaler Ra/Rz-Wert
Ein-Schnitt-Bearbeitung
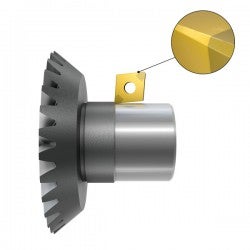
Die Ein-Schnitt „Zerspanungs-“Strategie eignet sich sowohl für die Außen- als auch für die Innenbearbeitung. Allerdings ist eine stabile Aufspannung wichtig, und der Werkzeugüberhang sollte beim Innendrehen nicht mehr als 1xD betragen. Für eine gute Bearbeitung werden gefaste, leicht verrundete Wendeschneidplatten (Typ-S) und mittlere Schnittgeschwindigkeiten sowie Vorschübe empfohlen.
Vorteile
- Schnellstmögliche Bearbeitungszeit
- Eine Werkzeugposition
Nachteile
- Probleme bei der Einhaltung enger Maßtoleranzen
- Kürzere Standzeit (als Zwei-Schnitt-Strategie)
- Toleranzabweichungen aufgrund relativ schnellen Verschleißes
Zwei-Schnitt-Strategie
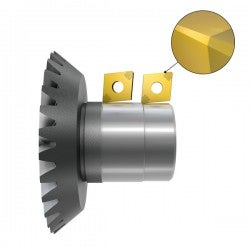
Die Zwei-Schnitt-Strategie erlaubt die unbeaufsichtigte Fertigung qualitativ hochwertiger Oberflächen. Wir empfehlen die Wendeschneidplatten zum Schruppen mit einem Radius von 1.2 mm (0.047 Zoll) und Wendeschneidplatten zum Schlichten mit nur einer Fase (Typ-T). Beide Wendeschneidplatten sollten eine Wiper-Geometrie besitzen.
Vorteile
- Optimierte Werkzeuglösung zum Schruppen und Schlichten
- Höhere Prozesssicherheit, engere Toleranzen und längere Bearbeitungszeiten zwischen den Werkzeugwechseln möglich
Nachteile
- Zwei Wendeschneidplatten erforderlich
- Zwei Werkzeugpositionen
- Ein zusätzlicher Plattenwechsel
Suchen Sie Werkzeugempfehlungen?
Hier finden Sie unsere Zerspanungswerkzeuge chevron_right
Brauchen Sie Beratung?
Stellen Sie uns eine Frage chevron_right
Was es sonst noch über die Grundlagen unserer Metallzerspanung zu lernen gibt?
Registrieren Sie sich für unser kostenloses E-Learning Programm chevron_right