Future tendenze dell'industria aerospaziale
Per decenni, l'aerospaziale è stato un settore in crescita. Negli anni ci sono stati dei periodi di crisi, ma nulla di profondo e pesante quanto il COVID-19. Ora che i mercati sono tornati ai livelli di crescita del 2006, come faranno i costruttori aerospaziali a rimettersi in carreggiata? Si può trovare una risposta nella sostenibilità delle operazioni di produzione. In questa sede Sébastien Jaeger, Industry Solution Manager – Aerospace per l'azienda specializzata in utensili da taglio Sandvik Coromant, spiega come la collaborazione rivestirà un ruolo fondamentale nella ripresa dell'industria aerospaziale.
Prima della pandemia, l'industria aerospaziale è cresciuta costantemente per 14 anni. Non c'è dubbio che le tendenze e il futuro dell'aerospaziale abbiano subito il grave impatto della pandemia da coronavirus, un evento senza precedenti. Con l'esponenziale riduzione dei viaggi di lavoro e di piacere, le linee aeree hanno dovuto adeguarsi a livelli di redditività sostanzialmente inferiori.
Tuttavia, non ci sono solo brutte notizie. Il settore aerospaziale ha iniziato a mostrare segni di miglioramento nella prima metà del 2021; un successo legato a svariati fattori, tra cui la diffusione dei vaccini, le prospettive economiche globali influenzate dalla prosperità cinese e la ripresa dei viaggi di lavoro e piacere. Secondo le stime, il settore tornerà ai livelli pre-crisi entro i prossimi due o tre anni. La velocità della ripresa è destinata a variare a seconda del paese e della regione. Nonostante ciò, il numero di nuovi aerei costruiti nel lungo termine potrebbe comunque risultare ridotto del 25% entro il 2040.
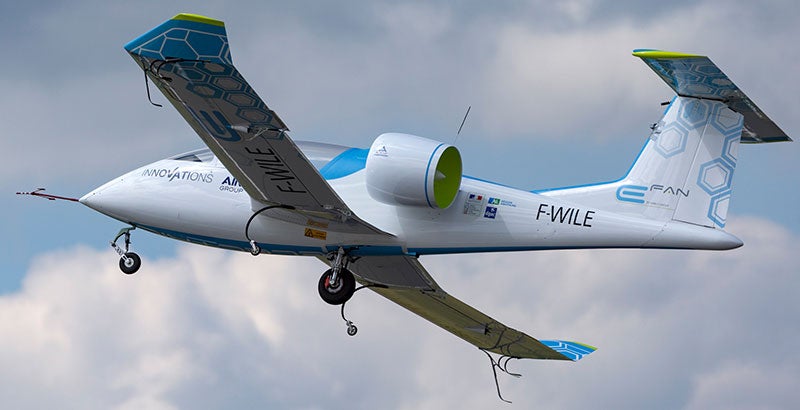
I costruttori stanno adottando diversi approcci alla progettazione dei velivoli elettrificati di domani, come il prototipo Airbus E-Fan di Airbus Group.
Un altro grande cambiamento, dal punto di vista tecnico, è la tendenza a preferire gli aerei a corridoio singolo anziché doppio. Questi sono caratterizzati da una larghezza inferiore e dovranno avere una maggiore autonomia di volo. Motori e telai sono strettamente collegati e interdipendenti, ma possiamo affermare che per quanto riguarda i motori il focus è tutto sulla sostenibilità. Ciò implica una riduzione di peso, rumore ed emissioni e una maggiore efficienza con consumi ridotti. Questi velivoli a corridoio singolo devono adeguarsi a un'ampia gamma di applicazioni, senza aumentare la dimensione dei motori o la loro quantità.
Esistono vari modi per affrontare queste sfide di progettazione. Si possono trovare carburanti alternativi (ad es. carburanti sintetici, biocombustibili o idrogeno) da utilizzare con i serbatoi esistenti. Un approccio a più lungo termine sarebbe adottare un nuovo tipo di architettura, prendendo esempio dai grandi costruttori che presentano nuove tipologie di motori. Poi ci sono i motori elettrici, a batteria o elettromagnetici, oppure i modelli ibridi (motori tradizionali assistiti dall'alimentazione elettrica).
Materiali difficili
L'industria automobilistica, ad esempio, sta già facendo grandi progressi nel campo dei nuovi sistemi elettrici e ibridi. I costruttori (OEM) del settore aerospaziale, invece, ci stanno ancora lavorando e molti di questi sviluppi non saranno ampiamente utilizzati prima del 2035. Nel caso dei velivoli più piccoli, in grado di ospitare da due a dieci persone, queste tecnologie potrebbero fare la loro comparsa in anticipo.
La riduzione di rumorosità, peso ed emissioni influirà sulle prestazioni dei sistemi elettrici, ma ci sono delle sfide da tenere in considerazione. Se un veicolo elettrico (EV) riscontra un problema, può semplicemente fermarsi a lato della strada — questa non è un'opzione a 10,000 piedi di altezza. Inoltre, il peso delle batterie può rappresentare un problema se pensiamo al fatto che l'obiettivo di progettisti e ingegneri è ottenere aerei più leggeri in grado di percorrere distanze superiori. Esistono quindi degli ostacoli tecnici su cui lavorare.
Per le fusoliere degli aerei, gli OEM stanno prendendo due diverse direzioni. Da una parte assistiamo all'aumento dell'uso di alluminio, sebbene i componenti di velivoli richiedano nuovi tipi di alluminio con una maggiore robustezza, resistenza alla fatica e altri attributi. Questo approccio aderisce al tradizionale design dei velivoli che, in parole semplici, prevede un grosso tubo con due ali e un motore.
Un altro approccio coinvolge invece l'esplorazione di altre forme, ad es. ali a delta, fusoliera integrata e ali controventate, o design in cui il motore è maggiormente integrato nella fusoliera. In questo caso gli ingegneri propenderanno più probabilmente per materiali compositi o combinazioni di materiali compositi e ceramici e materiali misti. Il grado di popolarità che questi design acquisiranno resta da vedere. Per ora, possiamo contare sul fatto che l'utilizzo di alluminio e superleghe resistenti al calore (HRSA) aumenterà. Le HRSA vengono generalmente utilizzate per i componenti di velivoli soggetti a requisiti prestazionali estremi. L'elevata resistenza alle alte temperature implica che il materiale riesce a mantenere la propria durezza in presenza di calore intenso.
Tuttavia, anche ai migliori costruttori di componenti aerospaziali può capitare di avere poca esperienza nella produzione di questi materiali tenaci. Ecco dove entrano in gioco le competenze di Sandvik Coromant.
Soluzioni per componenti
Sandvik Coromant mette a disposizione soluzioni per componenti in risposta alle maggiori pressioni esercitate sugli operatori, costretti a svolgere più attività contemporaneamente. Anziché concentrarsi su una sola macchina, i tecnici possono arrivare far funzionare quattro o cinque macchine alla volta, il che dà loro meno tempo e opportunità di concentrarsi su processi specifici. Ma cosa intendiamo per "soluzioni per componenti"? Il termine implica l'adozione di una prospettiva più olistica, che non si limita solamente agli utensili forniti da Sandvik Coromant ma include anche un supporto completo relativo all'intero processo.
Ad esempio, un cliente di Sandvik Coromant operativo nel settore aerospaziale aveva dei problemi nella lavorazione di HRSA. L'approccio adottato dal cliente richiedeva l'impiego di più macchine utensili, con uno scarso controllo truciolo e tempi ciclo prolungati. La durata utensile non era uniforme, i processi erano inaffidabili e l'operazione richiedeva il monitoraggio costante di un operatore.
Per progetti importanti come questo, Sandvik Coromant offre soluzioni suddivise in varie fasi, che includono la considerazione dei requisiti della macchina, l'analisi delle tempistiche per esaminare il costo per componente e l'analisi dei metodi di produzione al collaudo, considerando sia il tempo di lavoro in base al metodo applicato (MTM) che i processi degli utenti finali. Sono incluse anche la programmazione CAM (Computer-Aided Manufacturing) e la gestione di progetti locali o internazionali.
Le analisi hanno rivelato che per risolvere i problemi di truciolabilità occorreva cambiare la strategia di programmazione del cliente. In combinazione con l'utensile, gli specialisti di Sandvik Coromant hanno sviluppato una nuova strategia con curve dinamiche che ci ha permesso di controllare la truciolabilità in ogni momento. Abbiamo chiamato questo nuovo approccio scoop turning e lo abbiamo brevettato.
Lo scoop turning ha offerto al cliente un notevole risparmio. Oltre a un ottimo controllo truciolo, il cliente ha ottenuto anche una riduzione del tempo ciclo dell'80% e ha raddoppiato la durata utensile. Con il passaggio da quattro macchine a una sola, poi, l'esigenza di multi-tasking è stata ridotta, con processi di lavorazione più sicuri e una produzione "green light".
Ciò dimostra come un approccio più olistico possa rappresentare un vantaggio anche economico per i clienti. Anche i software rivestono un ruolo fondamentale, come ad esempio CoroPlus® Tool Guide, parte del portfolio digitale di Sandvik Coromant. I clienti possono prendere decisioni cruciali sulla scelta degli utensili e dei parametri di taglio prima ancora di aver iniziato la produzione.
Una tornitura più sostenibile
I costruttori aerospaziali stanno adottando diversi approcci alla sostenibilità. Nonostante ciò, Sandvik Coromant è riuscita a sviluppare una soluzione personalizzata per un cliente che ha poi portato vantaggi a interi settori.
Per aiutare il cliente a migliorare le prestazioni nelle operazioni di tornitura sulle HRSA, Sandvik Coromant ha sviluppato la qualità di tornitura S205. L'inserto è dotato del rivestimento Inveio® di seconda generazione per garantire un'elevata resistenza all'usura e una lunga durata utensile, mentre la tecnologia di post-trattamento rafforza l'inserto S205 modificandone le proprietà meccaniche. Il materiale presenta uno strato di rivestimento Inveio® con cristalli unidirezionali caratterizzati da strati di atomi più fitti che creano una solida barriera protettiva intorno all'inserto. Questo massimizza la protezione termica e migliora la resistenza alla craterizzazione e all'usura sul fianco.
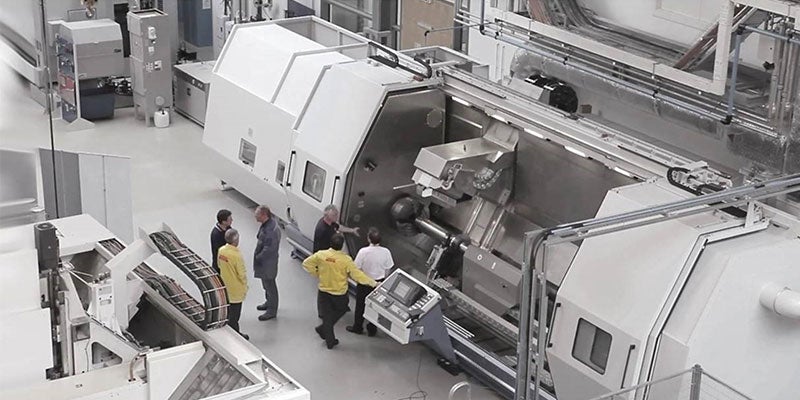
La qualità è adatta alla lavorazione di componenti come dischi delle turbine, anelli e alberi di motori aerospaziali. I nostri clienti hanno aumentato le velocità di taglio del 30-50% con S205 rispetto ad altre qualità concorrenti per la tornitura di HRSA, risultati ottenuti senza compromettere la durata utensile. Da allora S205 ha offerto i propri vantaggi a numerosi costruttori del settore aerospaziale e non solo. Tali risultati sono stati raggiunti grazie a un approccio olistico che coinvolge la metodologia PrimeTurning™ di Sandvik Coromant, che consente la tornitura in tutte le direzioni per massimizzare la produttività.
Nella metodologia PrimeTurningTM l'utensile entra nel componente all'altezza del mandrino e asporta il materiale muovendosi verso l'estremità del componente. Ciò dà la priorità ai sempre fondamentali volumi di truciolo asportato ma significa anche rapidità e qualità nella produzione e nei cambi utensile. Talvolta i clienti hanno completato interi cicli di produzione con solamente un cambio utensile, mentre con un utensile concorrente ne sarebbero serviti cinque.
Forse il settore aerospaziale sta affrontando una delle più grandi crisi finora sperimentate, ma si intravede una luce in fondo al tunnel. Sandvik Coromant continua a sostenere tutti i principali OEM aerospaziali per favorirne la ripresa dopo la pandemia, coniugando sostenibilità, utensili migliori e parametri di taglio ottimizzati con un approccio olistico all'attrezzamento.