Dove l'IoT incontra la sostenibilità
L'associazione Groupe Speciale Mobile Association (GSMA) ha esortato i leader del settore ad aumentare il loro uso della tecnologia intelligente nella corsa verso la neutralità climatica (Net Zero), e prevede che, così facendo, potrebbe contribuire fino al 40% delle riduzioni delle emissioni globali richieste. L'uso di tecnologie intelligenti per ridurre il consumo di energia non è nuovo per il settore manifatturiero, ma le sfide dell'implementazione di queste tecnologie in loco sono state a lungo una barriera all'adozione. Qui, Jörgen Friesendahl, Global Offer Manager per la lavorazione guidata dai dati presso Sandvik Coromant, offre consigli all'industria del taglio dei metalli sull'implementazione di soluzioni per fabbriche intelligenti, sia per ridurre il carbonio che per aumentare la redditività.
Nella sua ricerca sull'IoT (Internet of Things) e la riduzione del carbonio, la GSMA ha stimato che, nel settore manifatturiero, il 16% della riduzione di carbonio necessaria per raggiungere la neutralità climatica (Net Zero) potrebbe essere raggiunto utilizzando processi di produzione intelligente. Questo è l'equivalente di 1,4 gigatonnellate di CO2, o le emissioni di 140 milioni di automobili.
Considerando queste cifre straordinarie, ci si deve chiedere perché, in un settore che per primo ha coniato l’espressione Industria 4.0 oltre un decennio fa, le tecnologie intelligenti non sono state adottate universalmente? In effetti, si dice che solo l'1% dell'industria manifatturiera sta attualmente utilizzando la tecnologia connessa.
L'ostacolo più comune all'adozione delle tecnologie intelligenti nel settore manifatturiero è la mancanza di comprensione della facilità con cui questi strumenti possono essere implementati. Ripensando all'inizio dell'Industria 4.0, un'espressione usata originariamente alla fiera tedesca di Hannover Messe nel 2011, le fabbriche intelligenti erano considerate impianti futuristici che avrebbero avuto poca somiglianza con i siti produttivi reali. Oggi, abbiamo capito che la digitalizzazione non richiede una revisione dell'intero impianto ed è più spesso raggiunta in modo incrementale, attraverso tecnologie IoT scalabili e Big Data.
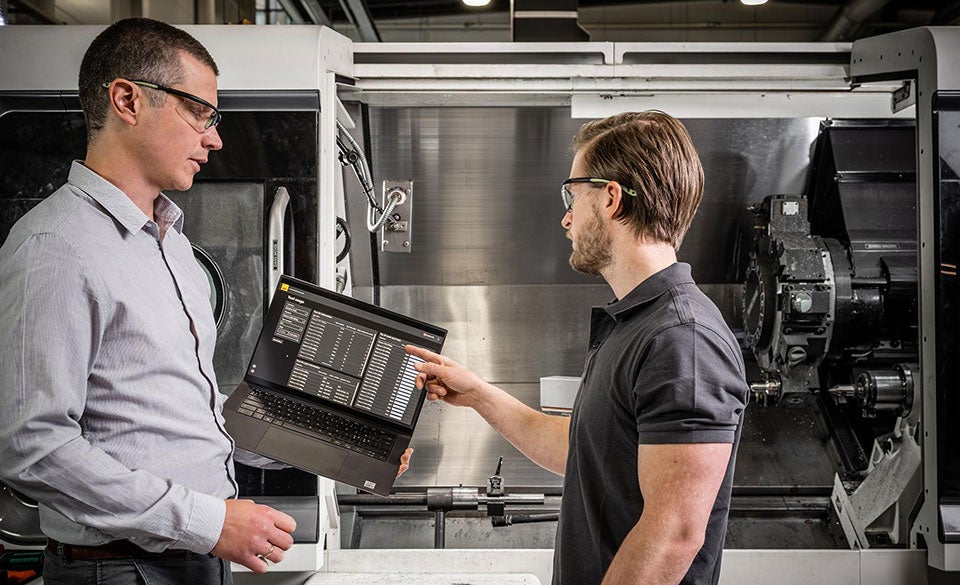
Ottenere dati usando l'IoT
Ogni impianto di produzione, consapevolmente o inconsapevolmente, genera ogni giorno enormi volumi di dati. Senza dubbio, i dati sono la risorsa più preziosa negli sforzi dei produttori per ridurre le emissioni di carbonio. Tuttavia, molti produttori non stanno utilizzando al meglio questa risorsa. Senza dati a livello di stabilimento che evidenziano quanta energia viene utilizzata e dove, come possono i produttori iniziare il percorso verso la riduzione dell'energia?
Un malinteso comune è che tutte le attrezzature debbano essere smart per generare dati con successo. In realtà, anche le strutture che operano con macchinari vecchi di decenni hanno il potenziale per estrarre dati dalle loro linee di produzione; e coloro che operano nel settore sanno che questi impianti sono molto più comuni delle futuristiche fabbriche intelligenti immaginate ad Hannover nel 2011. Questo può richiedere una combinazione di sensori e software intelligente, a seconda di fattori come l'età e il produttore di apparecchiature originali (OEM) delle attrezzature, e i protocolli di comunicazione utilizzati, ma è possibile.
Ottenere una visione del consumo energetico di una struttura è la chiave per identificare i punti critici. Si potrebbe scoprire che piccole modifiche a diverse parti della produzione possono produrre una significativa riduzione del carbonio. Tuttavia, è anche possibile che singoli pezzi delle attrezzature offrano il maggior margine di miglioramento. Ottenere dati da queste aree è fondamentale per ridurre l'energia utilizzata dalle singole macchine, e ci sono varie tecnologie che permettono ai produttori di farlo.
Una di queste soluzioni è la suite di prodotti CoroPlus®, che fa parte dell'offerta di Sandvik Coromant per la lavorazione guidata dai dati. I prodotti sono progettati per aiutare i produttori a migliorare l'efficienza nei processi di taglio dei metalli.
Un obiettivo fondamentale del CoroPlus® Process Control è quello di ridurre il consumo riducendo lo spreco di materiale. Lo strumento monitora le macchine in tempo reale e può attivare azioni secondo protocolli programmati. Immaginiamo che si verifichi un problema predeterminato relativo al processo di lavorazione, con CoroPlus® Process Control, questa tecnologia attiverà automaticamente un'azione correttiva, come l'arresto della macchina per evitare ulteriori sprechi. Inoltre, è dimostrato che condurre la manutenzione utilizzando questa tecnologia migliora l'efficienza operativa fino all'89%.
Energia ed economia
Considerando le sfide e le perdite che i produttori hanno affrontato durante la pandemia di COVID-19, c'è il rischio che la riduzione delle emissioni di carbonio diventi una priorità secondaria, che viene dopo la generazione di profitti necessaria alla ripresa? Il 49% dei dirigenti intervistati nel Commercial Aerospace Insight Report di Accenture prevede che ci vorranno fino a tre anni perché il settore manifatturiero aerospaziale ritorni ai livelli del 2019. Allo stesso modo, il settore manifatturiero automobilistico ha subito un crollo delle vendite di veicoli in quasi tutti i Paesi.
È vero e valido che l'economia di produzione deve sempre essere presa in considerazione quando si investe in nuovi utensili e processi di lavorazione. Tuttavia, le tecnologie giuste possono contribuire ad aumentare i profitti e, al contempo, a ridurre l'energia.
CoroPlus® Machining Insights, per esempio, è stato sviluppato per utilizzare i dati in tempo reale per orientare l'ottimizzazione degli utensili, e quindi le prestazioni e la redditività. In un'officina per il taglio dei metalli, la tecnologia può fornire un accesso istantaneo ai dati su una macchina specifica per dare agli operatori l'opportunità di monitorare l'efficacia complessiva delle risorse (la cosiddetta “Overall Equipment Effectiveness”, in sigla inglese OEE) e le prestazioni. In definitiva, questa supervisione rende le officine di produzione più efficienti e redditizie.
È passato più di un decennio da quando l'espressione Industria 4.0 è stata coniata per la prima volta, e da allora è diventata parte integrante del vocabolario della produzione. Eppure, la ricerca suggerisce che, nonostante le impressionanti opportunità di risparmio energetico che questa tecnologia potrebbe facilitare, molti produttori non riescono a sfruttare questi strumenti. Per raggiungere gli obiettivi mondiali sulle emissioni di carbonio, i produttori devono fare uno sforzo consapevole volto a ridurre il consumo di energia. Alla Sandvik Coromant, vogliamo garantire che i clienti possano implementare con successo questi strumenti per le persone, la redditività e il pianeta.
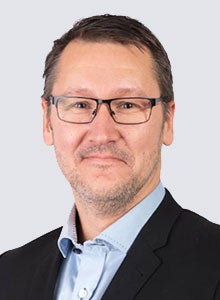
Jörgen Friesendahl
Global Offer Manager for data driven machining at Sandvik Coromant
Has over 30 years’ of experience in the world of metal cutting, mainly within product management, R&D and sales.