Delik delme için ipuçları
Kesme sıvısı beslemesi hakkında ipuçları ve püf noktaları
Delik delme işleminde başarılı bir performans elde etmek için doğru bir kesme sıvısı beslemesinin uygulanması çok önemlidir. Kesme sıvısı beslemesi aşağıdakileri etkiler:
- Talaş tahliyesi
- Delik kalitesi
- Takım ömrü
Kesme sıvısı deposunun hacmi, pompanın dakikada beslediği kesme sıvısı hacminden 5-10 kat daha fazla olmalıdır. Yeterli kesme sıvısı akışına sahip olmak önemlidir.
Hacim kapasitesi bir kronometre ve uygun ölçüde bir kova kullanılarak kontrol edilebilir.
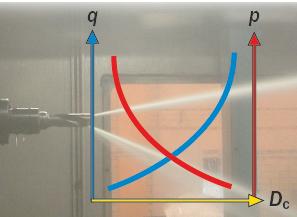
Kesme sıvısı beslemesinde basınç-çap ilişkisi
(basınç kırmızı, çap sarı, hacim mavi)
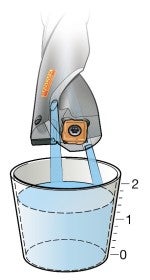
Matkaptan gelen hacmi kontrol edin
- Çözünür yağ (çözelti) daima EP (yüksek basınç) katkı maddeleriyle birlikte kullanılmalıdır. En iyi takım ömrü için yağ-su karışımı %5-12 arasında olmalıdır (paslanmaz çelik ve ısıl dirençli alaşım malzemeleri için %10-15). Kesme sıvısında yağ miktarını arttırırken daima distribütörünüzle görüşüp tavsiye edilen yağ yüzdelerini geçmemeye dikkat edin
- İçten kesme sıvısı beslemesi, uygulanabilir olduğunda, harici uygulanana kıyasla daima daha uygundur
- Katkısız yağ ile yağlama geliştirilir ve paslanmaz çelik delme işlemleri kolaylaşır. Her zaman EP katkı maddeleri kullanın. Hem yekpare karbür hem de değiştirilebilir kesici uçlu matkaplar katkısız yağ ile iyi çalışır
- Basınçlı hava, buhar halinde kesme sıvısı veya MQL (Minimum Miktarda Yağlama) özellikle döküm demir ve alüminyum için uygun koşullarda başarılı olabilir. Yüksek sıcaklıklar nedeniyle düşük kesme hızı önerilir ve bu da takım ömrünü olumsuz yönde etkileyebilir
İçten kesme sıvısı
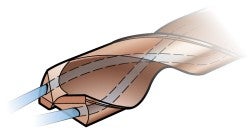
İçten kesme sıvısı, özellikle uzun talaş oluşturan malzemelerde ve derin delikler delindiğinde (>3 x DC) talaş sıkışmasını önlemek için tercih edilir.
Yatay bir matkap matkaptan çıktıktan sonra en az 30 cm (11,81 inç) boyunca aşağı düşmeyen kesme sıvısı akışına sahip olmalıdır.
Harici kesme sıvısı
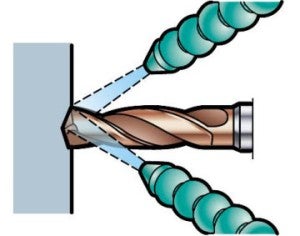
Harici kesme sıvısı, talaş oluşumu iyiyse ve delik derinliği düşükse kullanılabilir. Talaş boşaltmayı iyileştirmek için en az bir kesme sıvısı nozülü (matkap sabitse iki adet) takım eksenine yakın yönlendirilmelidir.
Kesme sıvısı olmadan kuru delik delme için ipuçları
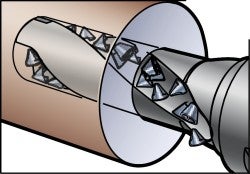
Kuru delik delme genelde önerilmez.
- Çapın 3 katının üzerinde delik derinlikleri için kısa talaşı malzemelerde kullanılabilir
- Tercihen yatay uygulamalarda
- Düşük kesme hızı önerilir
- Takım ömrü azalacaktır
Kuru delik delmenin aşağıdakilerde kesinlikle kullanılması önerilmez:
- Paslanmaz malzemeler (ISO M ve S)
- Uç kısmı değiştirilebilir matkaplar
Yüksek basınçlı kesme sıvısı (HPC) (~70 bar)
Yüksek basınçlı kesme sıvısı kullanmanın avantajları:
- Daha iyi soğutma etkisi sayesinde daha uzun takım ömrü
- İyileştirilmiş talaş tahliyesi ve paslanmaz çelik gibi uzun talaş oluşturan malzemelerde muhtemelen daha uzun takım ömrü
- Daha iyi talaş tahliyesi ile üstün güvenlik
- Verilen bir basınç ve delik ölçüsünde kesme sıvısı beslemesini sürdürebilmek için yeterli akışı sağlar
Talaş kontrolü için ipuçları
Talaş oluşumu ve talaş tahliyesi delik delme işleminde çok önemli konulardır ve bunlar, iş parçası malzemesine, matkap/kesici uç geometrisine, kesme sıvısı basıncına/hacmine ve kesme değerlerine göre değişebilir.
Talaş sıkışması matkapta radyal harekete yol açıp delik kalitesini, matkap ömrünü ve güvenilirliğini etkileyebilir ve matkap/kesici uç kırılmasına yol açabilir.
Daha kalın ve sert talaşlar | ||
Hız | ![]() | Düşük sürtünme nedeniyle daha açık |
ilerleme |
Talaşlar sorunsuz şekilde matkaptan atılabileceğinde talaş oluşumu kabul edilebilir. Bunu anlamanın en iyi yolu delik delme sırasında sesleri dinlemektir. Ses sürekli bir şekilde gelirse talaş tahliyesi başarılıdır, ancak kesintili olarak gelen ses talaş sıkışması olduğu anlamına gelir. İlerleme kuvvetini ya da güç monitörünü kontrol edin. Düzensizlikler varsa sebebi talaş sıkışması olabilir. Talaşlara bakın. Talaşlar kıvrık değil, uzun ve bükülmüş durumdaysa talaş sıkışması oluyor demektir. Deliğe bakın. Talaş sıkışması durumunda düzensiz bozuk bir yüzey gözlenecektir.
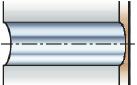
İyi talaş tahliyesi sağlanmış delik
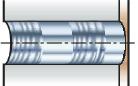
Talaş sıkışmasından etkilenen delik
Talaş sıkışmasını önlemek için ipuçları:
- Doğru kesme değerleri ve matkap/uç geometrisi kullandığınızdan emin olun
- Talaş şeklini inceleyin – İlerleme ve hızı ayarlayın
- Kesme sıvısı akışını ve basıncını kontrol edin
- Kesici kenarları kontrol edin. Talaş kırıcı tümüyle kavramadığında kesici kenar üzerindeki hasarlar ve çentiklenme uzun talaşlara neden olabilir
- Yeni iş parçası partisinden dolayı işlenebilirliğin değişip değişmediğini kontrol edin – kesme değerlerini ayarlayın
Mükemmel, kabul edilir ve kabul edilemez talaşlar
Değiştirilebilir kesici uçlu matkaplar
Merkezi kesici uç tanımlanması kolay konik bir talaş oluşturur. Çevresel kesici uç, tornalama ile oluşana benzer bir talaş oluşturur.
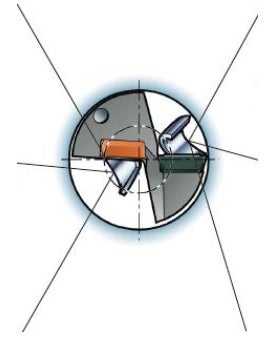
Merkezi şerit | Çevresel talaş |
![]() Mükemmel | ![]() Mükemmel |
![]() Kabul edilir | ![]() Kabul edilir |
![]() Talaş sıkışması | ![]() Talaş sıkışması |
Yekpare karbür matkaplar
Merkezden kesici kenarın çevresine kadar bir talaş oluşturulur.
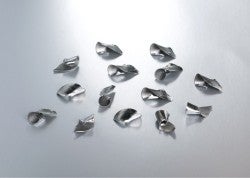
Mükemmel
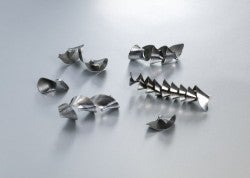
Kabul edilir
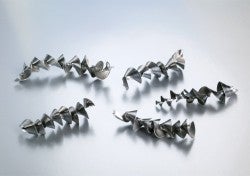
Talaş sıkışması
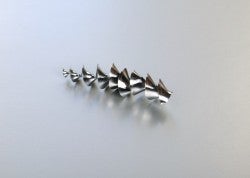
Başlangıç talaşı
Not: İş parçasına girişteki başlangıç talaşı daima uzundur ve sorun oluşturmaz.
Uç kısmı değiştirilebilir matkaplar
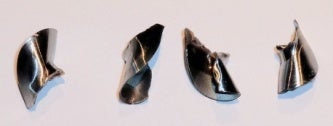
Mükemmel
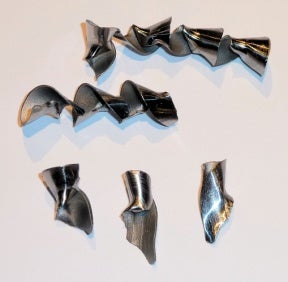
Kabul edilir
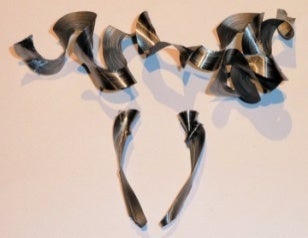
Kabul edilemez, talaş sıkışması riski
İlerlemeler ve hızlar için ipuçları ve püf noktaları
vc (m/dak)
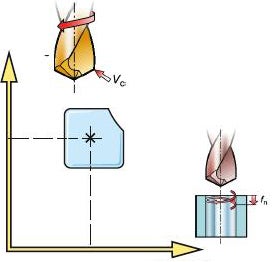
fn (mm/dev)
Kesme hızının etkileri – vc, (m/dak (ft/dak))
Kesme hızı, malzeme sertliği ile birlikte takım ömrünü ve güç tüketimini etkileyen temel faktördür.
- Kesme hızı, takım ömrünü belirleyen en büyük faktördür
- Kesme hızı, gücü Pc (kW) ve torku Mc (Nm) etkiler
- Yüksek hız, özellikle dış köşede yüksek sıcaklığa ve daha fazla serbest yüzey aşınmasına neden olur
- Yüksek hız, düşük karbonlu çelik gibi uzun talaş oluşturan yumuşak malzemelerde talaş oluşumu için avantajlıdır
- Çok yüksek kesme hızı:
- Çok hızlı serbest yüzey aşınması
- Plastik deformasyon
- Kötü delik kalitesi ve kötü delik toleransı - Çok düşük kesme hızı:
- Talaş yığılması
- Kötü talaş tahliyesi
- Kesmede daha uzun süre
İlerlemenin etkileri – fn (mm/dev (inç/dev))
- Talaş oluşumunu, yüzey kalitesini ve delik kalitesini etkiler
- Gücü Pc (kW) ve torku Mc (Nm) etkiler
- Yüksek ilerleme, ilerleme kuvvetini etkiler Ff (N) ve şartlar kararlı olmadığında dikkat edilmelidir
- Mekanik ve termal gerilimlere katkı yapar
- Yüksek ilerleme hızı:
- Daha sert talaş kırma
- Kesmede daha kısa süre
- Daha az takım aşınması ancak daha yüksek matkap kırılma riski
- Düşük delik kalitesi - Düşük ilerleme hızı:
- Daha uzun, ince talaşlar
- Kalitede iyileşme
- Hızlı takım aşınması
- Kesmede daha uzun süre
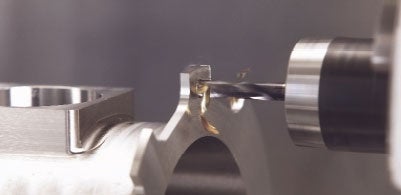
İnce/zayıf bir parçada delik delerken ilerleme hızı düşük tutulmalıdır.
Yüksek delik kalitesi elde etmek için ipuçları
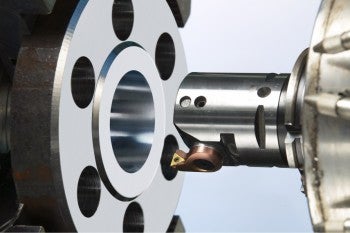
Talaş tahliyesi
Talaş tahliyesinin yeterli düzeyde olduğundan emin olun. Talaş sıkışması delik kalitesini ve güvenilirlik/takım ömrünü etkiler. Matkap/kesici uç geometrisi ve kesme değerleri çok önemlidir.
Kararlılık, takım kurulumu
Mümkün olan en kısa matkabı kullanın. Minimum salgıya sahip rijit ve hassas bir takım tutucu kullanın. Tezgah fener milinin iyi durumda olduğundan ve iyi hizalandığından emin olun. Parçanın sabit ve stabil olduğundan emin olun. Düzensiz, açılı yüzeyler ve çapraz delikler için doğru ilerleme hızları belirleyin.
Takım ömrü
Kesici uç aşınmasını kontrol edin ve önceden belirlenmiş bir takım ömrü programı belirleyin. Delik delmeyi kontrol etmek için en etkin yöntem bir ilerleme kuvveti monitörünün kullanılmasıdır.
Bakım
Kesici uç bağlama vidasını düzenli olarak değiştirin. Kesici ucu değiştirmeden önce uç yuvasını temizleyin ve tork anahtarı kullandığınızdan emin olun. Yekpare karbür matkapları tekrar bilemeden önce maksimum aşınmayı geçmeyin.
Farklı malzemeler için delik delme ipuçları ve teknikleri
- Düşük karbonlu çelik
- Östenitik ve duplex paslanmaz çelikler
- CGI (Kompakt Grafit Demir)
- Alüminyum alaşımlar
- Titanyum ve Isıl Dirençli Alaşımlar
- Sert çelikler
Düşük karbonlu çelikte delik delme için ipuçları

Problem: Genelde kaynaklı parçalarda kullanılan düşük karbonlu çeliklerde talaş oluşumu sorun yaratabilir. Çeliğin sertliği, karbon ve kükürt muhtevası ne kadar az olursa o kadar uzun talaşlar oluşur.
Öneriler: Talaş oluşumunda sorun yaşanırsa hızı vc arttırın ve ilerlemeyi fn düşürün (not: normal çeliklerde ilerleme artırılmalıdır).
Diğer: Yüksek basınçlı ve dahili kesme sıvısı kullanın.
Östenitik ve duplex paslanmaz çelikte delik delme için ipuçları

Problem: Östenitik, duplex ve süper duplex malzemeler talaş tahliyesinde problemlere sebep olabilirler.
Öneriler: Doğru geometri çok önemlidir çünkü talaşların düzgün bir şekilde oluşturulmasını sağlar ve tahliyelerine yardımcı olur. Genel anlamda keskin bir kesici kenar tercih edilir. Talaş oluşumunda sorun yaşanırsa ilerlemenin fn artırılması talaşların daha kolay kırılmasını sağlar.
Diğer: Yüksek basınçlı içten kesme sıvısı.
CGI'de (Kompakt Grafit Demir) delik delme için ipuçları

Problem: CGI için genelde ekstra özen göstermeye gerek yoktur. Gri döküm demirden daha büyük talaşlar oluşturur, ancak bunlar iyi kırılır. Kesme kuvvetleri daha yüksektir ve bu da takım ömrünü etkiler. Aşınmaya ekstra dayanıklı kaliteler gereklidir. Köşe aşınması tüm döküm demirlerinde olduğu gibi tipiktir.
Öneriler: Talaş oluşumunda sorun yaşanırsa hızı arttırın, vc, ve ilerlemeyi düşürün, fn.
Diğer: İçten kesme sıvısı.
Alüminyum alaşımda delik delme için ipuçları

Problem: Çapak oluşumu ve talaş tahliyesi sorun yaratabilir. Yapışma nedeniyle kötü takım ömrü oluşabilir.
Öneriler: En iyi talaş oluşumu için düşük ilerleme ve yüksek hız kullanın.
Yetersiz takım ömrünü önlemek için farklı kaplamaları test edip yapışmayı en aza indirmek gerekli olabilir. Bu kaplamalar içinde elmas kaplamalar bulunabilir veya hiç kaplama kullanılmayan belirli durumlar (alt tabakaya bağlı olarak) da olabilir.
Diğer: Yüksek basınçta emülsiyon veya buhar halinde kesme sıvısı kullanın.
Titanyum ve Isıl Dirençli Alaşımlarda delik delme için ipuçları

Problem: Delik yüzeyinin işleme ile sertleşmesi (pekleşme) daha sonraki işlemleri etkiler. İyi talaş tahliyesi elde etmek zor olabilir.
Öneriler: Titanyum alaşımları için bir geometri seçerken keskin bir kesici kenar tercih edilir. Nikel bazlı alaşımlar için sağlam bir geometri çok önemlidir. İşin sertleşmesi bir sorun oluşturursa ilerleme hızını artırmaya çalışın.
Diğer: Yüksek basınçlı (70 bara kadar) kesme sıvısı, performansı güçlendirir.
Sert çelikte delik delme için ipuçları

Problem: Kabul edilir takım ömrü elde etme.
Öneriler: Sıcaklığı azaltmak için daha düşük kesme hızı. Kolayca tahliye edilebilen kabul edilir talaşları elde etmek için besleme hızını ayarlayın.
Diğer: Yüksek karışımlı emülsiyon.
Delik toleransı için ipuçları
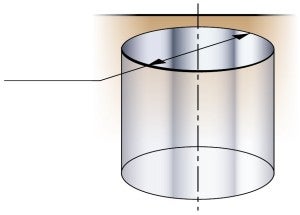
Bir deliğin ölçüleri üç parametreye ayrılabilir:
- Anma değeri (teorik olarak tam değer)
- Tolerans genişliği (ISO'ya göre IT olarak gösterilir)
- Toleransın konumu (ISO'ya göre büyük harflerle gösterilir)
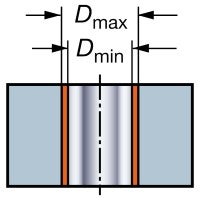
Dmaks eksi Dmin tolerans genişliğidir, IT olarak da adlandırılır.
Çap aralığı, D (mm)
Takım genişliği | D>3-6 | D>6-10 | D>10-18 | D>18-30 | D>30-50 | D>50-80 | D>80-120 | D>120-180 | D>180-250 |
IT5 | 0,005 | 0,006 | 0,008 | 0,009 | 0,011 | 0,013 | 0,015 | 0,018 | 0,020 |
IT6 | 0,008 | 0,009 | 0,011 | 0,013 | 0,016 | 0,019 | 0,022 | 0,025 | 0,029 |
IT7 | 0,012 | 0,015 | 0,018 | 0,021 | 0,025 | 0,030 | 0,035 | 0,040 | 0,046 |
IT8 | 0,018 | 0,022 | 0,027 | 0,033 | 0,039 | 0,046 | 0,054 | 0,063 | 0,072 |
IT9 | 0,030 | 0,036 | 0,043 | 0,052 | 0,062 | 0,074 | 0,087 | 0,100 | 0,115 |
IT10 | 0,048 | 0,058 | 0,070 | 0,084 | 0,100 | 0,120 | 0,140 | 0,160 | 0,185 |
IT11 | 0,075 | 0,090 | 0,110 | 0,130 | 0,160 | 0,190 | 0,220 | 0,250 | 0,290 |
IT12 | 0,120 | 0,150 | 0,180 | 0,210 | 0,250 | 0,300 | 0,350 | 0,400 | 0,460 |
IT13 | 0,180 | 0,220 | 0,270 | 0,330 | 0,390 | 0,460 | 0,540 | 0,630 | 0,720 |
Çap aralığı, D (inç)
Takım genişliği | D>0,118-0,236 | D>0,236-0,394 | D>0,394-0,709 | D>0,709-1,181 | D>1,181-1,969 | D>1,969-3,150 | D>3,150-4,724 | D>4,724-7,087 | D>7,087-9,843 |
IT5 | 0,0005 | 0,0002 | 0,0003 | 0,0004 | 0,0004 | 0,0005 | 0,0006 | 0,0007 | 0,0008 |
IT6 | 0,0003 | 0,0004 | 0,0004 | 0,0005 | 0,0006 | 0,0007 | 0,0009 | 0,0010 | 0,0011 |
IT7 | 0,0005 | 0,0006 | 0,0007 | 0,0008 | 0,0010 | 0,0012 | 0,0014 | 0,0016 | 0,0018 |
IT8 | 0,0007 | 0,0009 | 0,0011 | 0,0013 | 0,0015 | 0,0018 | 0,0021 | 0,0025 | 0,0028 |
IT9 | 0,0012 | 0,0014 | 0,0017 | 0,0020 | 0,0024 | 0,0029 | 0,0034 | 0,0039 | 0,0045 |
IT10 | 0,0019 | 0,0023 | 0,0028 | 0,0033 | 0,0039 | 0,0047 | 0,0055 | 0,0063 | 0,0073 |
IT11 | 0,0030 | 0,0035 | 0,0043 | 0,0051 | 0,0063 | 0,0075 | 0,0087 | 0,0098 | 0,0114 |
IT12 | 0,0047 | 0,0059 | 0,0071 | 0,0083 | 0,0098 | 0,0118 | 0,0138 | 0,0157 | 0,0181 |
IT13 | 0,0071 | 0,0087 | 0,0106 | 0,0129 | 0,0154 | 0,0181 | 0,0213 | 0,0248 | 0,0283 |
- IT-sayısı azaldıkça, tolerans da daha dardır
- Bir IT sınıfı için tolerans daha büyük çaplarda büyür
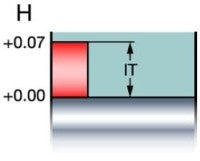
Bir örnek:
Anma değeri: 15,00 mm
Tolerans genişliği: 0,07 mm (ISO'ya göre IT 10)
Pozisyon: 0 ile artı arası (ISO'ya göre H)
Delik ve eksen toleransları
Delik toleransı genellikle delik içerisine yerleştirilebilecek olan bir mili toleransına bağlıdır.
Örnek:
Mil ø20 mm (0,787 inç) h7
Delik ø20 mm (0,787 inç) h7
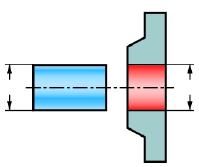
Mil tolerans konumu, delik toleransına karşılık gelen küçük harflerle tanımlanır. Aşağıdaki şekil resmin tamamını görmenizi sağlar:
En yaygın | ||
Milden daha büyük delik | ![]() | Delikten daha büyük mil |
Boşluklu geçme | | Kaygan geçme | Sıkı geçme | | Müdahale |
Boşluk (rulmanlar) | ![]() | Kavrama (=negatif boşluk (sabit bağlantılar) |