İş parçası malzemeleri
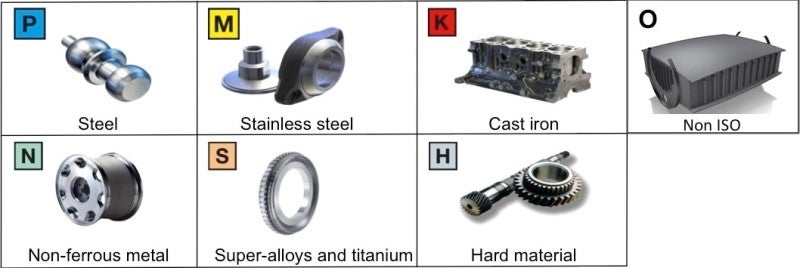
İş parçası malzeme grupları
Talaşlı imalat endüstrisi, çok farklı malzemelerden işlenen son derece geniş çeşitlilikte parçalar üretir. Her malzemenin, alaşım elementlerinden, ısıl işlemden, sertlikten vb. etkilenen kendine özgü özellikleri vardır. Bunlar da kesici takım geometrisi, kalite ve kesme değerleri seçimini etkiler. Bu seçimi kolaylaştırmak için, iş parçası malzemeleri ISO standardına göre altı ana gruba bölünmüştür ve her grup işlenebilirlik açısından benzersiz özelliklere sahiptir:
ISO P – Çelik, alaşımsız malzemelerden yüksek alaşımlı malzemelere kadar değişen ve çelik dökümler ile ferritik ve martensitik paslanmaz çelikleri içeren en büyük malzeme grubudur. İşlenebilirlik genellikle iyidir, ancak malzeme sertliğine, karbon içeriğine vb. bağlı olarak çok farklılık gösterir.
ISO M – Paslanmaz çelikler, minimum %12 krom ile alaşımlı malzemelerdir. Diğer alaşımlar nikel ve molibden içerebilir. Ferritik, martensitik, östenitik ve östenitik-ferritik (dubleks) gibi farklı koşullar, geniş bir malzeme yelpazesi oluşturur. Tüm bu malzemeler arasındaki ortak nokta, kesme kenarlarının çok fazla ısıya, çentik aşınmasına ve talaş yığılmasına maruz kalmasıdır.
ISO K – Dökme demir, çeliğin aksine kısa talaş oluşturan bir malzeme türüdür. Gri dökme demirler (GCI) ve dövülebilir dökme demirlerin (MCI) işlenmesi oldukça kolayken, sfero dökme demirler (NCI), kompakt dökme demirler (CGI) ve östemperlenmiş dökme demirler (ADI) daha zordur. Tüm dökme demirler, kesme kenarı için çok aşındırıcı olan SiC içerir.
ISO N – Demir dışı metaller, alüminyum, bakır, pirinç vb. gibi daha yumuşak metallerdir. Si içeriği %13 olan alüminyum çok aşındırıcıdır. Genel olarak, keskin kenarlı kesici uçlar için yüksek kesme hızları ve uzun takım ömrü beklenebilir.
ISO S – Isıya dayanıklı süper alaşımlar çok sayıda yüksek alaşımlı demir, nikel, kobalt ve titanyum bazlı malzemeler içerir. Yapışkandırlar, talaş yığılması oluştururlar, çalışma sırasında sertleşirler (iş sertleşmesi) ve ısı üretirler. ISO M malzemelerine çok benzerler ancak kesilmeleri çok daha zordur ve kesici uç kenarlarının takım ömrünü azaltırlar.
ISO H – Bu grup, sertliği 45-65 HRc arasında olan çelikleri ve ayrıca 400-600 HB civarında kokilli dökme demirleri içerir. Sertlik, işlemeyi zorlaştırır. Malzemeler kesme sırasında ısı üretir ve kesme kenarı için çok aşındırıcıdır.
O (Diğer): ISO dışı. Termoplastikler, termosetler, GFRP (Cam Elyaf Takviyeli Polimer/Plastik), CFRP (Karbon Fiber Takviyeli Plastik), karbon fiber kompozitler, aramid elyaf takviyeli plastik, sert kauçuk, grafit (teknik). Çeşitli endüstriler, özellikle havacılık endüstrisinde, kompozitleri daha fazla kullanıyor.
MC kodlarını kullanarak iş parçası malzemesi sınıflandırması
Malzemeleri sadece altı farklı gruba ayırmak, doğru kesici takım geometrisini, kaliteyi ve kesme değerlerini seçmek için yeterli bilgi sağlamaz. Bu nedenle malzeme gruplarının alt gruplara ayrılması gerekir. Sandvik Coromant, çeşitli tedarikçilerden, standartlardan ve pazarlardan gelen malzemeleri tanımlamak ve tanımlamak için CMC-kod sistemini (Coromant Malzeme Sınıflandırması) kullanmıştır. CMC sistemi ile malzemeler işlenebilirlik durumuna göre sınıflandırılır ve Sandvik Coromant buna uygun takımlama ve işleme değerleri konusunda da tavsiyelerde bulunur.
Verimliliği arttırmaya yardımcı olacak daha spesifik tavsiyelerde bulunmak için Sandvik Coromant yeni bir malzeme sınıflandırması oluşturdu. Daha detaylı bir yapıya sahiptir, daha fazla alt grup içerir ve tip, karbon içeriği, üretim süreci, ısıl işlem, sertlik vb. konularda ayrı bilgilere sahiptir.
MC kod yapısı
Yapı, MC kodunun harf ve rakamların bir kombinasyonunu kullanarak çeşitli iş parçası malzemesi özelliklerini ve karakteristiklerini temsil edebileceği şekilde ayarlanmıştır.
Örnek 1
P1.2.Z.AN kodu
P , çelik için ISO kodudur
1 alaşımsız çelik malzeme grubudur
2 , karbon içeriği için malzeme alt grubudur >%0,25 ≤ %0,55 C
Z üretim sürecidir: dövme / haddelenmiş / soğuk çekilmiş
AN , tavlanmış, sertlik değerleri ile tedarik edilen ısıl işlemdir
Örnek 2
N1.3.C.AG
N , demir dışı metaller için ISO kodudur
1 alüminyum malzeme grubudur
3 , Si içeriği %1-13 olan alüminyum alt grubudur
C üretim sürecidir: döküm
AG ısıl işlem içindir: yaşlandırma
Sadece malzeme bileşimini değil, aynı zamanda mekanik özellikleri şüphesiz etkileyen üretim sürecini ve ısıl işlemi de tanımlayarak, daha kesin bir açıklama mevcuttur. Bu daha sonra iyileştirilmiş kesme değeri önerileri oluşturmak için kullanılabilir.
İşlenebilirlik tanımı
Bir malzemenin işlenebilirliğini, yani işlenebilirliğini belirlemek için genellikle tanımlanması gereken üç ana faktör vardır.
- İş parçası malzemesinin metalurjik/mekanik açıdan sınıflandırılması.
- Mikro ve makro düzeyde kullanılacak kesme kenarı geometrisi.
- Kesici takım malzemesi (kalite) ve uygun bileşenleri, ör. kaplanmış semente karbür, seramik, CBN veya PCD, vb.
Yukarıdaki seçimler, eldeki malzemenin işlenebilirliği üzerinde en büyük etkiye sahip olacaktır. İlgili diğer faktörler şunlardır: kesme değerleri, kesme kuvvetleri, malzemeye ısıl işlem, yüzey kabuğu, metalürjik kalıntılar, takım tutma ve genel işleme koşulları, vb.
İşlenebilirliğin, kaliteler veya sayılardan farklı olarak doğrudan bir tanımı yoktur. Geniş anlamda, işlenecek iş parçası malzemesinin yeteneğini, kesme kenarında oluşturduğu aşınmayı ve elde edilebilecek talaş oluşumunu içerir. Bu açılardan, düşük alaşımlı bir karbon çeliğinin kesilmesi, daha zorlu östenitik paslanmaz çeliklere kıyasla daha kolaydır. Düşük alaşımlı çeliğin, paslanmaz çeliğe kıyasla daha iyi işlenebilirliğe sahip olduğu düşünülmektedir. "İyi işlenebilirlik" kavramı genellikle kesintisiz kesme işlemi ve adil takım ömrü anlamına gelir. Belirli bir malzeme için işlenebilirlik değerlendirmelerinin çoğu, pratik testler kullanılarak yapılır ve sonuçlar, yaklaşık olarak aynı koşullar altında başka bir malzeme türünün sonuçlarıyla karşılaştırılır. Bu testlerde mikro yapı, bulaşma eğilimi, takım tezgahı, stabilite, gürültü, takım ömrü vb. gibi diğer faktörler de dikkate alınmaktadır.
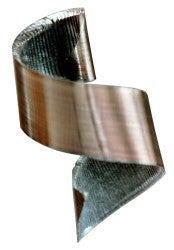
ISO P çelik
- Çelikler için MC kodları
- Alaşımsız çelik – P 1.1-1.5
- Düşük alaşımlı çelikler – P 2.1-2.6
- Yüksek alaşımlı çelikler – P 3.0-3.2
ISO P çelik nedir?
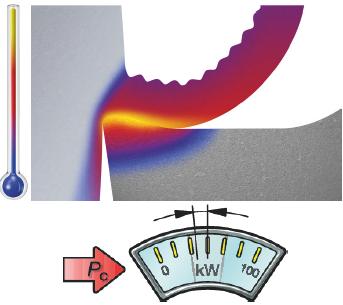
- Çelik, talaşlı imalat alanındaki en büyük iş parçası malzeme grubudur
- Çelikler sertleştirilmemiş veya 400 HB'ye kadar ortak sertlikte sertleştirilmiş ve temperlenmiş olabilir. Sertliği yaklaşık 48 HRC'nin üzerinde ve 62-65 HRC'ye kadar olan çelikler ISO H'ye aittir
- Çelik, ana bileşen olarak demir içeren bir alaşımdır (Fe bazlı)
- Alaşımsız çelikler %0,8'den daha düşük karbon içeriğine sahiptir ve başka alaşım elementleri olmadan yalnızca demirden (Fe) oluşur
- Alaşımlı çelikler %1,7'den daha düşük karbon içeriğine sahiptir ve Ni, Cr, Mo, V ve W gibi alaşım elementleri içerir
- Düşük alaşımlı çelikler %5'ten daha az alaşım elementleri içerir
- Yüksek alaşımlı çelikler %5'ten fazla alaşım elementi içerir
Genel olarak işlenebilirlik
- Çeliğin işlenebilirliği, alaşım elemanlarına, ısıl işleme ve üretim sürecine (dövme, haddelenmiş, döküm vb.) bağlı olarak farklılık gösterir.
- Genel olarak, talaş kontrolü nispeten kolay ve sorunsuzdur
- Düşük karbonlu çelikler, yapışkan ve keskin kesme kenarları gerektiren daha uzun talaşlar üretir
- Özgül kesme kuvveti kc1: 1400-3100 N/mm
- Kesme kuvvetleri ve dolayısıyla bunları işlemek için gereken güç sınırlı bir aralıkta kalır
Alaşım elemanları
C sertliği etkiler (daha yüksek içerik aşındırıcı aşınmayı artırır). Düşük karbon içeriği %<0,2, yapışkan aşınmasını artırır, bu da talaş yığılmasına ve kötü talaş kırılmasına neden olur.
Cr, Mo, W, V, Ti, Nb (karbür şekillendiriciler) – aşındırıcı aşınmayı artırır.
O'nun işlenebilirlik üzerinde büyük bir etkisi vardır; Metalik olmayan, oksidik ve aşındırıcı kalıntılar oluşturur.
Al, Ti, V, Nb çeliklerin ince taneli işlemlerinde kullanılır. Çeliği daha tok ve işlenmesi daha zor hale getirirler.
Ferritteki P, C, N, sünekliği düşürür, bu da yapışkan aşınmasını artırır.
Olumlu etki
Otomat çeliğinde (düşük erime noktasına sahip) Pb, talaş ve kesici uç arasındaki sürtünmeyi azaltır, aşınmayı azaltır ve talaş kırılmasını iyileştirir.
Ca, Mn (+S) yumuşak yağlama sülfürleri oluşturur. Yüksek S içeriği, işlenebilirliği ve talaş kırmayı iyileştirir.
Sülfür (S) işlenebilirlik üzerinde olumlu bir etkiye sahiptir. %0,001 ile %0,003 arasındaki küçük farklar işlenebilirlik üzerinde önemli etkilere sahip olabilir. Bu etki otomat çeliklerinde kullanılır. Yaklaşık %0,25'lik kükürt içeriği tipiktir. Kükürt, talaş ve kesme kenarı arasında yağlama tabakası oluşturacak yumuşak manganez sülfür (MnS) kalıntıları oluşturur. MnS ayrıca talaş kırılmasını da iyileştirecektir. Kurşun (Pb) da benzer bir etkiye sahiptir ve genellikle %0,25 civarında olan otomat çeliklerinde S ile birlikte kullanılır.
Hem olumlu hem de olumsuz
Si, Al, Ca, aşınmayı artıran oksit kalıntıları oluşturur. Çelikteki kalıntılar, toplam bileşimin çok küçük bir yüzdesini temsil etseler de işlenebilirlik üzerinde önemli bir etkiye sahiptir. Bu etki hem olumsuz hem de olumlu olabilir. Örneğin, demir eriyiğini deokside etmek için alüminyum (Al) kullanılır. Bununla birlikte, alüminyum sert aşındırıcı alümina (Al2O3) oluşturur ve bu da işlenebilirlik üzerinde zararlı bir etkiye sahiptir (bir kesici uç üzerindeki alüminyum kaplamayı karşılaştırın). Bununla birlikte, bu olumsuz etki, aşındırıcı parçacıkların etrafında yumuşak bir kabuk oluşturacak olan Kalsiyum (Ca) eklenerek önlenebilir.
- Dökme çelik , kum ve cüruf içerebilen pürüzlü bir yüzey yapısına sahiptir ve kesme kenarının tokluğuna yüksek talep getirir
- Haddelenmiş çelik , oldukça büyük bir tane boyutu sergiler, bu da yapıyı düzensiz hale getirir ve kesme kuvvetlerinde değişikliklere neden olur
- Dövme çelik daha küçük bir tane boyutuna sahiptir ve yapı olarak daha homojendir, bu da kesildiğinde daha az sorun yaratır
Çelikler için MC kodları
Çelikler, işlenebilirlik açısından, alaşımsız, düşük alaşımlı, yüksek alaşımlı ve sinterlenmiş çelikler olarak sınıflandırılır.
MC kodu | Malzeme grubu | Malzeme alt grubu | İmalat prosesi | Isıl işlem | Nom | Spesifik kesme kuvveti, kc1 (N/mm2) | mc | ||||
P1.1.Z.AN | 1 | alaşımsız Mn<1.65 | 1 | <=%0.25 C | Z | Dövme/haddelenmiş/soğuk çekilmiş | AN | Tavlı | 125 HB | 1500 | 0,25 |
P1.1.Z.HT | 1 | 1 | Z | HT | Sertleştirilmiş + temperlenmiş | 190 HB | 1770 | 0,25 | |||
P1.2.Z.AN | 1 | 2 | >0,25... <=%0,55 C | Z | Dövme/haddelenmiş/soğuk çekilmiş | AN | Tavlı | 190 HB | 1700 | 0,25 | |
P1.2.Z.HT | 1 | 2 | Z | HT | Sertleştirilmiş + temperlenmiş | 210 HB | 1820 | 0,25 | |||
P1.3.Z.AN | 1 | 3 | yüksek karbonlu, %>0,55 C | Z | Dövme/haddelenmiş/soğuk çekilmiş | AN | Tavlı | 190 HB | 1750 | 0,25 | |
P1.3.Z.HT | 1 | 3 | Z | HT | Sertleştirilmiş + temperlenmiş | 300 HB | 2000 | 0,25 | |||
P1.4.Z.AN | 1 | 4 | Otomat çeliği | Z | Dövme/haddelenmiş/soğuk çekilmiş | AN | Tavlı | 220 HB | 1180 | 0,25 | |
P1.5.C.HT | 1 | 5 | Tüm karbon içeriği (döküm) | C | döküm | HT | işlenmemiş | 150 HB | 1400 | 0,25 | |
P1.5.C.AN | 1 | 5 | C | AN | Sertleştirilmiş + temperlenmiş | 300 HB | 2880 | 0,25 | |||
P2.1.Z.AN | 2 | Düşük alaşımlı (alaşım elementleri <=%5) | 1 | <=%0.25 C | Z | Dövme/haddelenmiş/soğuk çekilmiş | AN | Tavlı | 175 HB | 1700 | 0,25 |
P2.2.Z.AN | 2 | 2 | >0,25... <=%0,55 C | Z | AN | 240 HB | 1950 | 0,25 | |||
P2.3.Z.AN | 2 | 3 | yüksek karbonlu, %>0,55 C | Z | AN | 260 HB | 2020 | 0,25 | |||
P2.4.Z.AN | 2 | 4 | Otomat çeliği | Z | AN | 225 HB | | ||||
P2.5.Z.HT | 2 | 5 | Tüm karbon içeriği (sertleştirilmiş ve temperlenmiş) | Z | Dövme/haddelenmiş/soğuk çekilmiş | HT | Sertleştirilmiş + temperlenmiş | 330 HB | 2000 | 0,25 | |
P2.6.Z.UT | 2 | 6 | Tüm karbon içeriği (döküm) | C | döküm | UT | işlenmemiş | 200 HB | 1600 | 0,25 | |
P2.6.Z.HT | 2 | 6 | C | HT | Sertleştirilmiş + temperlenmiş | 380 HB | 3200 | 0,25 | |||
P3.0.Z.AN | 3 | Yüksek alaşımlı (alaşım elementleri %>5) | 0 | Ana grup | Z | Dövme/haddelenmiş/soğuk çekilmiş | AN | Tavlı | 200 HB | 1950 | 0,25 |
P3.0.Z.HT | 3 | 0 | Z | HT | Sertleştirilmiş + temperlenmiş | 380 HB | 3100 | 0,25 | |||
P3.0.C.UT | 3 | 0 | C | döküm | UT | işlenmemiş | 200 HB | 1950 | 0,25 | ||
P3.0.C.HT | 3 | 0 | C | HT | Sertleştirilmiş + temperlenmiş | 340 HB | 3040 | 0,25 | |||
P3.1.Z.AN | 3 | 1 | HSS | Z | Dövme/haddelenmiş/soğuk çekilmiş | AN | Tavlı | 250 HB | 2360 | 0,25 | |
P3.2.C.AQ | 3 | 2 | Manganlı çelik | C | döküm | AQ | tavlanmış/söndürülmüş veya tavlanmış | 300 HB | 3000 | 0,25 | |
P4.0.S.NS | 4 | sinterlenmiş çelikler | 0 | Ana grup | S | Sinterlenmiş | NS | Belirtilmemiş | 150 HB |
Alaşımsız çelik – P 1.1-1.5
Tanım
Alaşımsız çeliklerde karbon içeriği genellikle sadece %0,8 iken, alaşımlı çeliklerde ek alaşım elementleri bulunur. Sertlik 90 ila 350HB arasında değişir. Daha yüksek karbon içeriği (%>0,2) malzemenin sertleşmesini sağlar.
Ortak bileşenler
Baskın kullanımlar şunları içerir: inşaat çeliği, yapısal çelik, derin çekilmiş ve damgalanmış ürünler, basınçlı kap çeliği ve çeşitli dökme çelikler. Genel kullanımlar şunları içerir: akslar, şaftlar, borular, dövmeler ve kaynaklı yapılar (C<%0,25).
İşlenebilirlik
Düşük karbonlu çeliklerde (%0,25'<) talaş kırma ve bulaşma eğilimlerindeki zorluklara özel dikkat gösterilmesi gerekir. Yüksek kesme hızları ve pozitif kesme yüzeyi ve ince kaplamalı kaliteler ile keskin kenarlar ve/veya geometriler bulaşma eğilimini azaltacaktır. Tornalamada, talaş kırılmasını iyileştirmek için kesme derinliğinin köşe radyüsüne yakın veya daha büyük kalması tavsiye edilir. Genel olarak işlenebilirlik sertleştirilmiş çelikler için çok iyidir. Ancak, kesme kenarlarında nispeten büyük yanak aşınması oluşturma eğilimindedirler.
Düşük alaşımlı çelikler – P 2.1-2.6
Tanım
Düşük alaşımlı çelikler, şu anda talaşlı imalatta kullanılan en yaygın malzemelerdir. Grup hem yumuşak hem de sertleştirilmiş malzemeleri içerir (50 HRc'ye kadar).
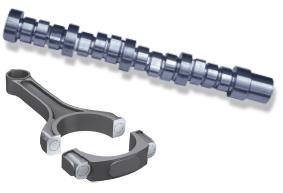
Ortak bileşenler
Daha yüksek sıcaklıklar için Mo ve Cr alaşımlı basınçlı kap çelikleri kullanılır. Genel kullanımlar şunları içerir: akslar, şaftlar, yapısal çelikler, borular ve dövmeler. Otomotiv endüstrisi için parça örnekleri şunlardır: biyel kolları, kam milleri, cv mafsalları, tekerlek göbeği, direksiyon pinyonları.
İşlenebilirlik
Düşük alaşımlı çeliklerin işlenebilirliği, alaşım içeriğine ve ısıl işleme (sertliğe) bağlıdır. Gruptaki tüm malzemeler için en yaygın aşınma mekanizmaları krater ve yanak aşınmasıdır.
Sertleştirilmiş malzemeler kesme bölgesinde daha fazla ısı üretir ve kesme kenarında plastik deformasyona neden olabilir.
Yüksek alaşımlı çelikler – P 3.0-3.2
Tanım
Yüksek alaşımlı çelikler, toplam alaşım içeriği %5'in üzerinde olan karbon çeliklerini içerir. Bu grup hem yumuşak hem de sertleştirilmiş malzemeleri içerir (50 HRc'ye kadar).
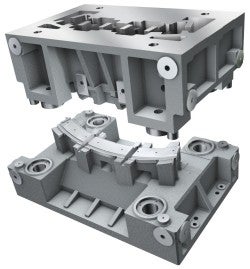
Ortak bileşenler
Bu çeliklerin tipik kullanımları şunları içerir: takım tezgahı parçaları, kalıplar, hidrolik bileşenler, silindirler ve kesici takımlar (HSS).
İşlenebilirlik
Genel olarak, işlenebilirlik daha yüksek alaşım içerikleri ve sertlikte azalır. Örneğin, %12-15 alaşım elementlerinde ve 450 HB'ye kadar sertlikte, kesme kenarının plastik deformasyona dayanması için iyi bir ısı direncine ihtiyacı vardır.
ISO M paslanmaz çelik
- Paslanmaz çelik için MC kodları
- Ferritik ve martensitik paslanmaz çelik – P5.0-5.1
- Östenitik ve süper östenitik paslanmaz çelik – M1.0-2.0
- Dubleks paslanmaz çelik – M 3.41-3.42
ISO M paslanmaz çelik nedir?
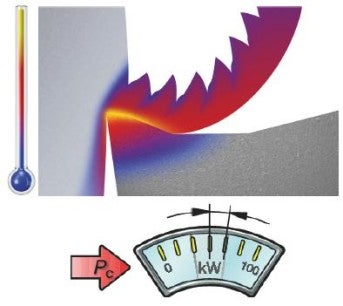
- Ana bileşen olarak demir (Fe) elementi içeren bir alaşım
- %12'den yüksek krom içeriğine sahip
- Genel olarak düşük karbon içeriğine sahiptir (C ≤ %0,05)
- Çeşitli Nikel (Ni), Krom (Cr), Molibden (Mo), Niyobyum (Nb) ve Titanyum (Ti) ilaveleri, korozyona karşı direnç ve yüksek sıcaklıklarda mukavemet gibi farklı özellikler sağlar
- Krom, çeliğin yüzeyinde pasifleştirici bir Cr2O3 tabakası oluşturmak için oksijen (O) ile birleşir ve bu da malzemeye aşındırıcı olmayan bir özellik sağlar
Genel olarak işlenebilirlik
Paslanmaz çeliklerin işlenebilirliği, alaşım elemanlarına, ısıl işleme ve imalat süreçlerine (dövme, döküm vb.) bağlı olarak farklılık gösterir. Genel olarak, işlenebilirlik daha yüksek alaşım içeriği ile azalır, ancak tüm paslanmaz çelik gruplarında serbest işleme veya işlenebilirliği geliştirilmiş malzemeler mevcuttur.
- Uzun talaş oluşturan malzeme
- Ferritik/martensitik malzemelerde talaş kontrolü makuldür, östenitik ve duplex tiplerde daha karmaşık hale gelir
- Spesifik kesme kuvveti: 1800-2850 N/mm
- İşleme yüksek kesme kuvvetleri, talaş yığılması, ısı ve işleme ile sertleşmiş yüzeyler oluşturur
- Daha yüksek nitrojen (N) içerikli östenitik yapı, mukavemeti arttırır ve korozyona karşı bir miktar direnç sağlar, ancak işlenebilirliği düşürürken, deformasyon sertleşmesi artar
- İşlenebilirliği artırmak için Sülfür (S) ilaveleri kullanılır
- Yüksek C-içeriği (%>0,2) nispeten geniş serbest yüzey aşınması sağlar
- Mo ve N işlenebilirliği azaltır. Bununla birlikte, asit saldırılarına karşı direnç sağlarlar ve yüksek sıcaklık dayanımına katkıda bulunurlar
- SANMAC (Sandvik ticari adı), korozyon direncinden ödün vermeden sülfür ve oksitlerin hacim payını optimize ederek işlenebilirliğin iyileştirildiği bir malzemedir
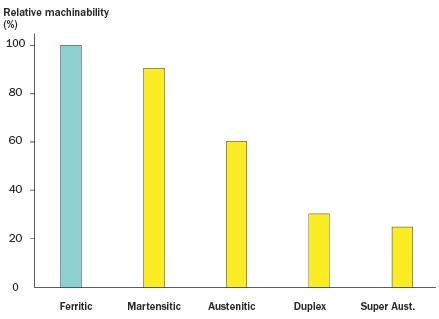
Paslanmaz çelik için MC kodları
MC kodu | Malzeme grubu | Malzeme alt grubu | İmalat prosesi | Isıl işlem | Nom | özgül kesme kuvveti, kc1 (N/mm2) | MC | ||||
P5.0.Z.AN | 5 | paslanmaz çelik ferritik/martensitik | 0 | Ana grup | Z | Dövme/haddelenmiş/soğuk/çekilmiş | AN | Tavlı | 200 HB | 1800 | 0,21 |
P5.0.Z.HT | 5 | 0 | Z | HT | Sertleştirilmiş + temperlenmiş | 330 HB | 2300 | 0,21 | |||
P5.0.Z.PH | 5 | 0 | Z | PH | presepitatif sertleşmiş | 330 HB | 2800 | 0,21 | |||
P5.0.C.UT | 5 | 0 | C | Döküm | UT | İşlenmemiş | 250 HB | 1900 | 0,25 | ||
P5.0.C.HT | 5 | 0 | C | HT | Sertleştirilmiş + temperlenmiş | 330 HB | 2100 | 0,25 | |||
P5.1.Z.AN | 5 | 1 | Otomat çeliği | Z | Dövme/haddelenmiş/soğuk | AN | Tavlı | 200 HB | 1650 | 0,21 | |
M1.0.Z.AQ | 1 | Östenitik | 0 | Ana grup | Z | Dövme/haddelenmiş/soğuk/çekilmiş | AQ | Tavlanmış/söndürülmüş veya tavlanmış | 200 HB | 2000 | 0,21 |
M1.0.Z.PH | 1 | 0 | Z | PH | presepitatif sertleşmiş | 300 HB | 2400 | 0,21 | |||
M1.0.C.UT | 1 | 0 | C | Döküm | UT | İşlenmemiş | 200 HB | 1800 | 0,25 | ||
M1.1.Z.AQ | 1 | 1 | Geliştirilmiş işlenebilirlik (SANMAC gibi) | Z | Dövme/haddelenmiş/soğuk/çekilmiş | AQ | Tavlanmış/söndürülmüş veya tavlanmış | 200 HB | 2000 | 0,21 | |
M1.1.Z.AQ | 1 | 2 | Otomat çeliği | Z | AQ | 200 HB | 1800 | 0,21 | |||
M1.3.Z.AQ | 1 | 3 | Ti-stabilize | Z | AQ | 200 HB | 1800 | 0,21 | |||
M1.3.C.AQ | 1 | 3 | C | Döküm | AQ | 200 HB | 1800 | 0,25 | |||
M2.0.Z.AQ | 2 | Süper östenitik Ni>=%20 | 0 | Ana grup | Z | Dövme/haddelenmiş/soğuk/çekilmiş | AQ | 200 HB | 2300 | 0,21 | |
M2.0.C.AQ | 2 | 0 | C | Döküm | AQ | 200 HB | 2150 | 0,25 | |||
M3.1.Z.AQ | 3 | Dubleks (östenitik/ferritik) | 1 | %>60 ferrit (temel kural N<%0.10) | Z | Dövme/haddelenmiş/soğuk/çekilmiş | AQ | Tavlanmış/söndürülmüş veya tavlanmış | 230 HB | 2000 | 0,21 |
M3.1.C.AQ | 3 | 1 | C | Döküm | AQ | 230 HB | 1800 | 0,25 | |||
M3.2.Z.AQ | 3 | 2 | %<60 ferrit (temel kural N>=%0.10) | Z | Dövme/haddelenmiş/soğuk/çekilmiş | AQ | 260 HB | 2400 | 0,21 | ||
M3.2.C.AQ | 3 | 2 | C | Döküm | AQ | 260 HB | 2200 | 0,25 |
İş parçası malzeme grubunun tanımlanması
Bir paslanmaz çeliğin elde ettiği mikro yapı, esas olarak, ana alaşım bileşenleri Krom (Cr) ve Nikel'in (Ni) en önemli olduğu kimyasal bileşimine bağlıdır (şemaya bakınız). Gerçekte, östenit veya ferriti stabilize etmeye çalışan diğer alaşım bileşenlerinin etkisinden dolayı varyasyon geniş olabilir. Yapı ayrıca ısıl işlemle veya bazı durumlarda soğuk işlemle değiştirilebilir. Çökeltme sertleşmesi ferritik veya östenitik paslanmaz çelik, daha yüksek bir gerilme mukavemetine sahiptir.
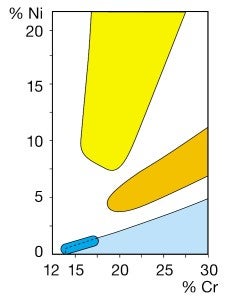

Östenitik çelikler

Östenitik-ferritik (dubleks) çelikler

Ferritik krom çelikleri

Martensitik krom çelikleri
Ferritik ve martensitik paslanmaz çelik – P5.0-5.1
Tanım
İşlenebilirlik açısından ferritik ve martensitik paslanmaz çelikler ISO P olarak sınıflandırılır. Normal Cr içeriği %12-18'dir. Diğer alaşım elementlerinin sadece küçük ilaveleri mevcuttur.
Martensitik paslanmaz çelikler nispeten yüksek karbon içeriğine sahiptir ve bu da onları sertleştirilebilir kılar. Ferritik çelikler manyetik özelliklere sahiptir. Kaynaklanabilirlik hem ferritik hem de martensitik için düşüktür ve korozyona karşı orta ila düşük dirençlidir, bu da daha büyük bir Cr içeriği ile artar.
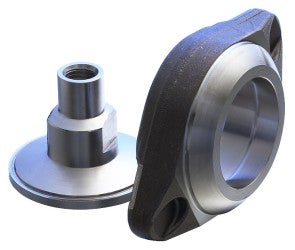
Ortak bileşenler
Genellikle korozyon direncine sınırlı bir talep getiren uygulamalarda kullanılır. Ferritik malzeme, sınırlı Ni içeriği nedeniyle nispeten düşük maliyetlidir. Uygulama örnekleri şunlardır: pompalar, türbinler, buhar ve su türbinleri, somunlar, cıvatalar, sıcak su ısıtıcıları, korozyon direnci konusundaki düşük gereksinimler nedeniyle kağıt hamuru ve gıda işleme endüstrileri için şaftlar.
Martensitik çelikler sertleştirilebilir ve çatal bıçak takımı, tıraş bıçakları, cerrahi aletler vb. kenarlar için kullanılır.
İşlenebilirlik
Genel olarak işlenebilirlik iyidir ve düşük alaşımlı çeliklere çok benzer. Bu nedenle ISO P malzemesi olarak sınıflandırılır. Yüksek karbon içeriği (%>0,2) malzemenin sertleşmesini sağlar. İşleme, bir miktar talaş yığılması ile yanak ve krater aşınması yaratacaktır. ISO P kaliteleri ve geometrileri iyi çalışır.
Östenitik ve süper östenitik paslanmaz çelik – M1.0-2.0
Tanım
Östenitik çelikler, paslanmaz çeliklerin birincil grubudur; en yaygın bileşim %18 Cr ve %8 Ni'dir (örn.18/8-çelikler, tip 304). Korozyona karşı daha iyi dirençli bir çelik, genellikle "aside dayanıklı çelik" (tip 316) olarak adlandırılan% 2-3 molibden eklenerek oluşturulur. MC grubu ayrıca %20'nin üzerinde Ni içeriğine sahip süper östenitik paslanmaz çelikleri de içerir. Östenitik çökeltme sertleştirme çelikleri (PH), ısıl işlem görmüş durumda östenitik bir yapıya ve yaklaşık %1 alüminyum (Al) ile %>16 Cr içeriğine ve %>7 Ni içeriğine sahiptir. Tipik bir çökeltme sertleştirilmiş çelik 17/7 PH çeliktir.
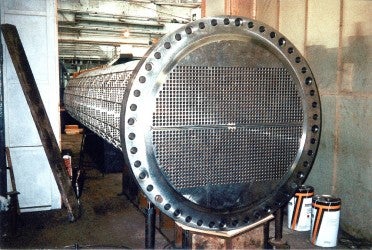
Ortak bileşenler
Korozyona karşı iyi direncin gerekli olduğu bileşenlerde kullanılır. Çok iyi kaynaklanabilirlik ve yüksek sıcaklıklarda iyi özellikler. Uygulamalar şunları içerir: kimyasal, kağıt hamuru ve gıda işleme endüstrileri ve uçaklar için egzoz manifoldları. İyi mekanik özellikler soğuk işlemle iyileştirilir.
İşlenebilirlik
İşlerken sertleşme sert yüzeyler ve sert talaşlar oluşturur ve bu da çentik aşınmasına yol açar. Aynı zamanda yapışma oluşturur ve talaş yığılması (BUE) oluşturur. %60 bağıl işlenebilirlik oranına sahiptir. Sertleşme durumu, kaplama ve alt tabaka malzemesini kenardan yırtabilir, bu da çentiklenmeye ve kötü yüzey kalitesine neden olur. Östenit, kırılması zor olan sert, uzun ve sürekli talaşlar üretir. S eklenmesi işlenebilirliği artırır, ancak korozyona karşı direncin azalmasına neden olur. Pozitif geometriye sahip keskin kenarlar kullanın. İşle sertleştirilmiş tabakanın altında kesin. Kesme derinliğini sabit tutun. İşlendiğinde çok fazla ısı üretir.
Dubleks paslanmaz çelik – M 3.41-3.42
Tanım
Ferritik paslanmaz Cr bazlı bir çeliğe Ni eklenerek, hem ferrit hem de östenit içeren karışık bir baz yapı/matris oluşturulacaktır. Buna dubleks paslanmaz çelik denir. Dubleks malzemeler yüksek gerilme mukavemetine sahiptir ve çok yüksek korozyon direncini korur. Süper dubleks ve hiper dubleks gibi tanımlamalar, daha yüksek alaşım elementi içeriğini ve hatta daha iyi korozyon direncini gösterir. Dubleks çeliklerde %18 ile %28 arasında bir Cr içeriği ve %4 ile %7 arasında bir Ni içeriği yaygındır ve %25-80'lik bir ferritik pay üretecektir. Ferrit ve östenit fazı genellikle oda sıcaklığında sırasıyla% 50-50 oranında bulunur.
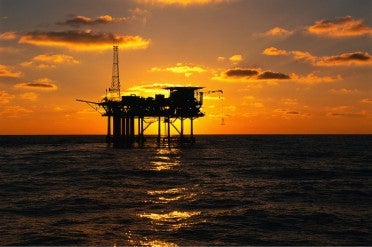
Ortak bileşenler
Kimya, gıda, inşaat, medikal, selüloz ve kağıt yapım endüstrileri için makinelerde ve asit veya klor içeren işlemlerde kullanılır. Genellikle açık deniz petrol ve gaz endüstrisi ile ilgili ekipmanlar için kullanılır.
İşlenebilirlik
Bağıl işlenebilirlik, yüksek akma noktası ve yüksek çekme mukavemeti nedeniyle genellikle %30 ile zayıftır. %60'ın üzerindeki yüksek ferrit içeriği işlenebilirliği artırır. İşleme, talaş çekiçlemesine neden olabilen ve yüksek kesme kuvvetleri oluşturabilen güçlü talaşlar üretir. Kesme sırasında çok fazla ısı üretir ve bu da plastik deformasyona ve ciddi krater aşınmasına neden olabilir.
Çentik aşınmasını ve çapak oluşumunu önlemek için küçük giriş açıları tercih edilir. Takım bağlama ve iş parçası sabitlemede stabilite esastır.
ISO K dökme demir
- Dökme demir için MC kodları
- Dövülebilir dökme demir (MCI) K 1.1-1.2 ve gri dökme demir (GCI) K 2.1-2.3
- Sfero Dökme Demir (NCI) K 3.1-3.5
- Sıkıştırılmış grafit demir (CGI) K 4.1-4.2
- Östemperlenmiş Sünek Demir (ADI) K 5.1- 5.3
ISO K dökme demir nedir?
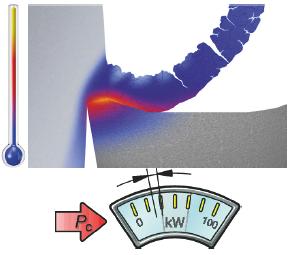
5 ana dökme demir türü vardır:
- Gri Dökme Demir (GCI)
- Dövülebilir Dökme Demir (MCI)
- Sfero Dökme Demir (NCI)
- Sıkıştırılmış grafit demir (CGI)
- Östemperlenmiş Sünek Demir (ADI)
Dökme demir, nispeten yüksek bir Si yüzdesine (%1-3) sahip bir Fe-C bileşimidir. Karbon içeriği, östenitik fazda C'nin maksimum çözünürlüğü olan %2'nin üzerindedir. Cr (Krom), Mo (Molibden) ve V (Vanadyum), mukavemeti ve sertliği artıran, ancak işlenebilirliği azaltan karbürler oluşturur.
Genel olarak işlenebilirlik
- Çoğu koşulda iyi talaş kontrolüne sahip kısa talaş oluşturan malzeme. Spesifik kesme kuvveti: 790 – 1350 N/mm
- Özellikle kum kalıntıları bulunan dökme demirlerde daha yüksek hızlarda işleme, aşındırıcı aşınmaya neden olur
- NCI, CGI ve ADI, normal GCI'ye kıyasla farklı mekanik özellikler ve matriste grafit varlığı nedeniyle ekstra dikkat gerektirir
- Dökme demirler genellikle negatif tipte kesici uçlarla işlenir, çünkü bunlar güçlü kenarlar ve güvenli uygulamalar sağlar
- İyi aşınma direnci için karbür alt tabakalar sert olmalı ve kaplamalar kalın alüminyum oksit tiplerinde olmalıdır
- Dökme demirler geleneksel olarak kuru olarak işlenir, ancak esas olarak karbon ve demirden kaynaklanan toz kirliliğini minimumda tutmak için ıslak koşullarda da kullanılabilir. Kesme sıvısı teminli uygulamalara uygun kaliteler de mevcuttur
Sertliğin etkisi
- Dökme demirler için işlenebilirlik ile ilgili sertliğin etkisi, diğer malzemelerde olduğu gibi aynı kurallara uyar
- Örneğin, ADI (östemperlenmiş sünek demir) ve CGI (sıkıştırılmış grafit demir) ile NCI (sfero dökme demir) 300-400 HB'ye kadar sertliklere sahiptir
- HB. MCI ve GCI ortalama 200-250 HB
- Beyaz dökme demir, karbonun serbest karbon olarak mevcut olmak yerine bir karbür Fe3C (sementit) oluşturmak üzere demir ile reaksiyona girdiği hızlı soğutma hızlarında 500 HB'nin üzerinde bir sertliğe ulaşabilir. Beyaz dökme demirler çok aşındırıcıdır ve işlenmesi zordur
Dökme demir için MC kodları
İşlenebilirlik açısından dökme demirler dövülebilir, gri, sfero, sıkıştırılmış grafit demir (CGI) ve östemperlenmiş sünek demir (ADI) türleri olarak sınıflandırılır. Daha yüksek sertliklerin bazıları sfero dökme demirlerde ve ADI'lerde bulunabilir.
MC Kodu | Malzeme grubu | Malzeme alt grubu | İmalat süreci | Isıl işlem | Nom | Özgül kuvvet, kc1(N/mm2) | mc | ||||
K1.1.C.NS | 1 | Dövülebilir | 1 | Düşük çekme dayanımı | C | Döküm | NS | Belirtilmemiş | 200 HB | 780 | 0,28 |
K1.2.C.NS | 1 | 2 | Yüksek çekme dayanımı | C | NS | 260 HB | 1020 | 0,28 | |||
K2.1.C.UT | 2 | Gri | 1 | Düşük çekme dayanımı | C | Döküm | UT | İşlenmemiş | 180 HB | 900 | 0,28 |
K2.2.C.UT | 2 | 2 | Yüksek çekme dayanımı | C | UT | 245 HB | 1100 | 0,28 | |||
K2.3.C.UT | 2 | 3 | Östenitik | C | UT | 175 HB | 1300 | 0,28 | |||
K3.1.C.UT | 3 | Nodüler | 1 | Ferritik | C | Döküm | UT | İşlenmemiş | 155 HB | 870 | 0,28 |
K3.2.C.UT | 3 | 2 | Ferritik/perlitik | C | UT | 215 HB | 1200 | 0,28 | |||
K3.3.C.UT | 3 | 3 | Perlitik | C | UT | 265 HB | 1440 | 0,28 | |||
K3.4.C.UT | 3 | 4 | Martensitik | C | UT | 330 HB | 1650 | 0,28 | |||
K3.5.C.UT | 3 | 5 | Östenitik | C | UT | 190 HB | |||||
K4.1.C.UT | 4 | CGI | 1 | Düşük çekme dayanımı (perlit <%90) | C | Döküm | UT | İşlenmemiş | 160 HB | 680 | 0,43 |
K4.2.C.UT | 4 | 2 | Yüksek çekme dayanımı (perlit >=%90) | C | UT | 230 HB | 750 | 0,41 | |||
K5.1.C.NS | 5 | ADI | 1 | Düşük çekme dayanımı | C | Döküm | NS | Belirtilmemiş | 300 HB | ||
K5.2.C.NS | 5 | 2 | Yüksek çekme dayanımı | C | NS | 400 HB | |||||
K5.3.C.NS | 5 | 3 | Ekstra yüksek çekme dayanımı | C | NS | 460 HB |
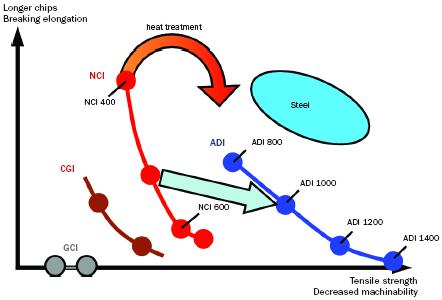
Östemperleme ısıl işlemi, sünek demiri (NCI) östemperlenmiş sünek demire (ADI) dönüştürür.
Dövülebilir dökme demir (MCI) K 1.1-1.2 ve gri dökme demir (GCI) K 2.1-2.3
Tanım
Dövülebilir dökme demir, beyaza yakın bir demir matrisinden üretilir ve daha sonra iki adımda ısıl işleme tabi tutulur, bir ferrit + perlit + temperlenmiş karbon yapısı üretir ve gri dökme demirdeki daha fazla kırılmaya neden olan katmanlı yapıya kıyasla düzensiz grafit tanelerine yol açar. Bu, dövülebilir malzemenin çatlamaya karşı daha az hassas olduğu ve kopma mukavemeti ve uzama değerlerinin daha yüksek olduğu anlamına gelir.
Gri dökme demir, tipik pul formunda grafite sahiptir ve ana özellikleri şunlardır: düşük darbe dayanımı (kırılgan davranış); iyi ısı iletkenliği, motor çalışırken daha az ısı ve kesme işleminde düşük ısı; İyi sönümleme özellikleri, motordaki titreşimleri emer.
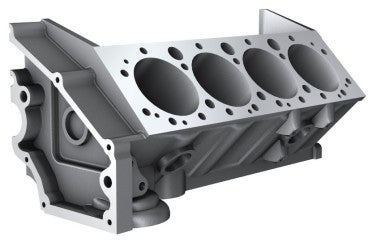
Ortak bileşenler
MCI'dan üretilen bileşenler şunları içerir: aks yatakları, palet tekerlekleri, boru bağlantı parçaları ve yüksek mukavemetli dişliler. GCI'dan üretilen bileşenler şunları içerir: kızartma tavaları, motor blokları, kompresör silindirleri, dişliler ve dişli kutusu muhafazaları.
İşlenebilirlik
Dövülebilir dökme demir, GCI'den daha yüksek bir gerilme mukavemetine sahiptir ve işlenebilirliği açısından NCI'ye benzer, ancak her ikisi de genellikle mükemmel işleme özelliklerine sahiptir. Genel olarak, perlitik bir yapıya sahip dökme demir aşındırıcı aşınmayı arttırırken, ferritik yapılar yapışkan aşınmayı arttırır.
Gri dökme demir düşük darbe dayanımına sahiptir, düşük kesme kuvvetleri oluşturur ve işlenebilirliği çok iyidir. Kesme işleminde aşınma sadece aşınma ile oluşur; Kimyasal aşınma yoktur. Gri dökme demir, mekanik özelliklerini iyileştirmek için genellikle Cr ile alaşımlanır. Daha yüksek mukavemet, işlenebilirliğin azalmasına neden olacaktır.
Sfero Dökme Demir (NCI) K 3.1-3.5
Tanım
Sfero dökme demir küresel şekilli grafite sahiptir ve ana özellikleri iyi sertliktir (Young modülü); iyi darbe dayanımı = sert malzeme, kırılgan değil; iyi gerilme mukavemeti; kötü sönümleme özellikleri, motordaki titreşimleri emmez; Kötü ısı iletkenliği, kesme işleminde daha yüksek ısı. GCI ile karşılaştırıldığında, NCI'deki grafit, daha yüksek gerilme özelliklerine ve tokluğa katkıda bulunan nodüller şeklinde görünür.
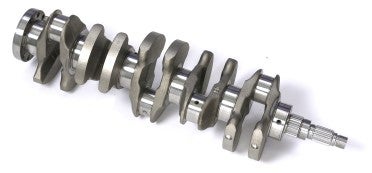
Ortak bileşenler
Göbekler, borular, makaralar, egzoz manifoldları, krank milleri, diferansiyel muhafazaları, yatak kapakları, egzoz manifoldları, yatak plakaları, turboşarj muhafazaları, debriyaj plakaları ve volanlar.
Turboşarj gövdeleri ve egzoz manifoldları genellikle ısıya daha dayanıklı olan SiMo alaşımlı dökme demirden yapılır.
İşlenebilirlik
Sfero dökme demir, talaş yığılması konusunda güçlü bir eğilime sahiptir. Bu eğilim, daha yüksek ferritik içeriğe sahip daha yumuşak NCI malzemeleri için daha güçlüdür. Yüksek ferritik içerikli ve darbeli kesimlere sahip parçaları işlerken, yapışma aşınması genellikle baskın aşınma mekanizmasıdır. Bu, kaplamanın pullanması ile ilgili sorunlara neden olabilir.
Yapışma sorunu, daha yüksek perlitik içeriğe sahip daha sert NCI malzemelerinde daha az belirgindir. Burada sürtünme aşınması ve/veya plastik deformasyon meydana gelme olasılığı daha yüksektir.
Sıkıştırılmış grafit demir (CGI) K 4.1-4.2
Tanım
CGI, hem artan mukavemet hem de ağırlık azaltma taleplerini karşılayabilen ve yine de makul işlenebilirliğini koruyabilen bir malzemedir. CGI'nın termal ve sönümleme özellikleri NCI ve GCI arasındadır. Metal yorgunluğuna karşı direnç, gri demirin iki katıdır. CGI'daki grafit parçacıkları, gri dökme demirde olduğu gibi uzatılmış ve rastgele yönlendirilmiştir, ancak daha kısa, daha kalın ve yuvarlatılmış kenarlara sahiptirler. CGI'daki mercan benzeri morfoloji, grafit parçacıklarının yuvarlatılmış kenarları ve düzensiz engebeli yüzeyleri ile birlikte, grafit ve demir matris arasında güçlü bir yapışma sağlar. CGI'da mekanik özelliklerin gri dökme demire göre çok gelişmiş olmasının nedeni budur. Perlitik içeriği %90'ın altında olan CGI en yaygın olanıdır.
Ortak bileşenler
CGI, daha fazla güç emebilen daha hafif ve daha güçlü malzemelerin gerekli olduğu motor üretimi için çok uygundur. Tek başına motor bloğu ağırlığı, GCI'dan yapılana kıyasla yaklaşık yüzde 20 oranında azaltılabilir. Diğer örnekler silindir kapakları ve disk frenlerdir.
İşlenebilirlik
İşlenebilirlik açısından bakıldığında, sıkıştırılmış grafit demir gri ve sfero dökme demir arasındadır. Gri dökme demire göre iki ila üç kat daha fazla germe dayanımı ve daha düşük ısıl iletkenlik ile CGI işleme, kesme bölgesinde daha yüksek kesme kuvvetleri ve daha fazla ısı üretir. CGI malzemesindeki titanyum içeriğinin artması takım ömrünü olumsuz etkiler.
En yaygın işleme operasyonları yüzey frezeleme ve silindir delik işlemedir. Silindir delik işleme yerine dairesel frezeleme yöntemine geçilmesi hem takım ömrünü hem de verimliliği artırabilir.
Östemperlenmiş Sünek Demir (ADI) K 5.1- 5.3
Tanım
Östemperlenmiş sünek demir, ısıl işlem görmüş dökme demir ailesini oluşturur. Östemperleme ısıl işlemi, sünek demiri, özellikleri mükemmel mukavemet, tokluk ve yorulma özelliklerini içeren östemperlenmiş sünek demire (ADI) dönüştürür. ADI, birim ağırlık başına alüminyumdan daha güçlüdür ve çelik kadar aşınmaya karşı dirençlidir. Çekme ve akma dayanımı değerleri standart sünek demirin iki katıdır. Yorulma mukavemeti %50 daha yüksektir ve bilyeli dövme veya fileto haddeleme ile artırılabilir.
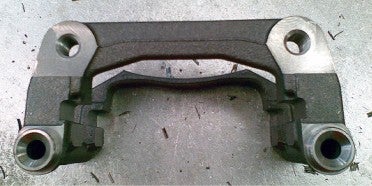
Ortak bileşenler
ADI dökümleri, üstün performansı nedeniyle çelik dövme ve dökümlerin, kaynaklı imalatların, karbonlanmış çeliğin ve alüminyumun yerini giderek daha fazla alıyor. Baskın kullanımları, süspansiyon ve şanzıman parçaları vb. için kullanıldığı otomotiv endüstrisindedir. Ayrıca güç/enerji ile madencilik ve inşaat sektörlerinde de kullanılmaktadır.
İşlenebilirlik
NCI ile karşılaştırıldığında takım ömründe %40-50 oranında azalma beklenebilir. ADI'nin çekme mukavemeti ve sünekliği çeliğe yakındır, ancak talaş oluşturma süreci ADI'yi sünek demir (parçalı talaş oluşumu) olarak sınıflandırır. ADI'nin mikro sertliği, karşılaştırılabilir sertlikteki çeliklerle karşılaştırıldığında daha yüksektir. Daha yüksek ADI kaliteleri, mikro yapıda sert parçacıklar içerir. Yüksek mukavemet ve süneklik nedeniyle yüksek termal ve mekanik yükler, segmentlere ayrılmış talaş oluşum süreci nedeniyle aşınmayı kesme kenarı yakınında ve üst tırmıkta aşınmaya neden olur. Talaş oluşumu sırasındaki sertleşme, yüksek dinamik kesme kuvvetlerine neden olur. Kesme kenarı sıcaklığı, aşınmayı belirlemek için güçlü bir faktördür.
ISO N demir içermeyen malzemeler
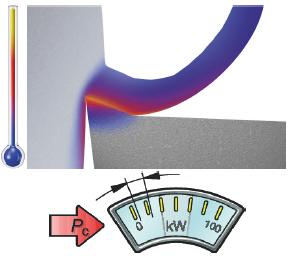
ISO N demir içermeyen malzemeler nelerdir?
- Bu grup, yüksek mukavemetli bronzlar (>225HB) hariç, sertliği 130 HB'nin altında olan demir dışı, yumuşak metalleri içerir
- %12-13'ten daha az silikon (Si) içeren alüminyum (Al) alaşımları en büyük kısmı temsil eder
- MMC: Metal Matris Kompozit: Al + SiC (%20-30)
- Magnezyum bazlı alaşımlar
- Bakır:%99,95 Cu içeren elektrolitik bakır
- Bronz: Kalaylı bakır (Sn) (%10-14) ve/veya alüminyum (%3-10)
- Pirinç: Çinko (Zn) (%40-15) ile bakır (%60-85)
Alüminyumun işlenebilirliği
- Uzun talaş oluşturan malzeme
- Alaşım olarak kullanıldığında talaş kontrolü nispeten daha kolaydır
- Saf Al yapışkandır ve keskin kesme kenarları ve yüksek Vc gerektirir.
- Spesifik kesme kuvveti: 350–700 N/mm
- Kesme kuvvetleri ve dolayısıyla bunları işlemek için gereken güç düşüktür
- Malzeme, Si içeriği %7-8'in altında olduğunda ince taneli, kaplamasız karbür kalitelerle ve daha yüksek Si içerikli alüminyum için PCD uçlu kalitelerle işlenebilir
- Daha yüksek Si içeriği >%12 olan aşırı ötektik Al çok aşındırıcıdır
Ortak bileşenler
Motor bloğu, silindir kafası, şanzıman gövdeleri, muhafazalar, havacılık sanayi şasi parçaları.
N-malzemeler için MC kodları
MC kodu | Malzeme grubu | Malzeme alt grubu | İmalat prosesi | Isıl işlem | Nom | Spesifik kesme kuvveti, kc1 (N/mm2) | mc | ||||
N1.1.Z.UT | 1 | Alüminyum bazlı alaşımlar | 1 | Ticari olarak saf | Z | Döküm | UT | İşlenmemiş | 30 HB | 350 | 0,25 |
N1.2.Z.UT | 1 | 2 | AlSi alaşımları, Si<=%1 | Z | UT | 60 HB | 400 | 0,25 | |||
N1.2.Z.AG | 1 | 2 | Z | AG | Yaşlandırılmış | 100 HB | 650 | 0,25 | |||
N1.2.S.UT | 1 | 2 | S | Sinterlenmiş | UT | İşlenmemiş | 75 HB | 410 | 0,25 | ||
N1.2.C.NS | 1 | 2 | C | Döküm | NS | Belirtilmemiş | 80 HB | 410 | 0,25 | ||
N1.3.C.UT | 1 | 3 | AlSi dökme alaşımlar, Si<=%1 ve <%13 | C | UT | İşlenmemiş | 75 HB | 600 | 0,25 | ||
N1.3.C.AG | 1 | 3 | C | AG | Yaşlandırılmış | 90 HB | 700 | 0,25 | |||
N1.4.C.NS | 1 | 4 | AlSi dökme alaşımlar, Si>=%13 | C | NS | Belirtilmemiş | 130 HB | 700 | 0,25 | ||
N2.0.C.UT | 2 | Magnezyum bazlı alaşımlar | 0 | Ana grup | C | Döküm | UT | İşlenmemiş | 70 HB | ||
N3.1.U.UT | 3 | Bakır bazlı alaşımlar | 1 | Kurşunsuz bakır alaşımları (elektrolitik bakır dahil) | U | Belirtilmemiş | UT | İşlenmemiş | 100 HB | 1350 | 0,25 |
N3.2.C.UT | 3 | 2 | Kurşunlu pirinç ve bronz (Pb<=%1) | C | Döküm | UT | 90 HB | 550 | 0,25 | ||
N3.3.S.UT | 3 | 2 | S | Sinterlenmiş | UT | 35 HB | |||||
N3.3.U.UT | 3 | 3 | Serbest kesim bakır bazlı alaşımlar (Pb>1%) | U | Belirtilmemiş | UT | 110 HB | 550 | 0,25 | ||
N3.4.C.UT | 3 | 4 | Yüksek mukavemetli bronzlar (>225HB) | C | Döküm | UT | 300 HB | ||||
N4.0.C.UT | 4 | Çinko bazlı alaşımlar | 0 | Ana grup | C | Döküm | UT | İşlenmemiş | 70 HB |
ISO S, HRSA ve titanyum
- S malzemeler için MC kodları
- HRSA malzemeleri – S 1.0-3.0
- Titanyum– S 4.1-4.4
ISO S, HRSA ve titanyum nedir?
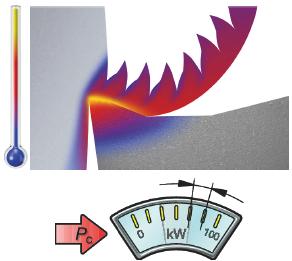
- ISO S grubu, ısıya dayanıklı süper alaşımlar (HRSA) ve titanyum olarak ikiye ayrılabilir
- HRSA malzemeleri üç gruba ayrılabilir: Nikel bazlı, demir bazlı ve kobalt bazlı alaşımlar
- Durum: tavlanmış, çözelti ısıl işlem görmüş, yaşlandırılmış, haddelenmiş, dövme, döküm
- Özellikler: artan alaşım içeriği (Co, Ni'den daha fazla), ısıya karşı daha iyi direnç, artan gerilme mukavemeti ve daha yüksek korozyon direnci ile sonuçlanır
Genel olarak işlenebilirlik
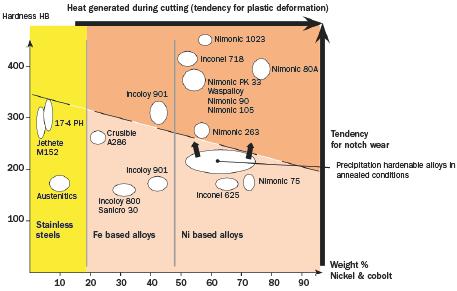

= Paslanmaz çelikler

= Isıl işlem görmüş (yaşlandırılmış)

= Çözelti işlemi (tavlanmış)
- Her birinin fiziksel özellikleri ve işleme davranışı, hem alaşımın kimyasal yapısı hem de üretim sırasında aldığı hassas metalürjik işleme nedeniyle önemli ölçüde değişir
- Tavlama ve yaşlandırma özellikle sonraki işleme özellikleri üzerinde etkilidir
- Zor talaş kontrolü (parçalı talaşlar)
- Spesifik kesme kuvveti: HRSA için 2400–3100 N/mm ve titanyum için 1300–1400 N/mm
- Kesme kuvvetleri ve gereken güç oldukça yüksektir
Yaşlandırma
Daha yüksek mukavemet elde etmek için, ısıya dayanıklı alaşımlar "çökeltme sertleştirilebilir".
Malzemenin yüksek sıcaklıklarda işlenmesiyle, yani yaşlandırma işlemiyle, alaşımda küçük metaller arası parçacıklar çökeltilir. Bu parçacıklar kristal yapıdaki hareketi engelleyecek ve sonuç olarak malzemenin deforme olması daha zor olacaktır.
S-malzemeler için MC kodları
İşlenebilirlik açısından HRSA çelikleri demir, nikel ve kobalt bazlı malzemeler olarak sınıflandırılır. Titanyum, ticari olarak saf alfa alaşımları ve yakın alfa alaşımları, alfa / beta alaşımları ve beta alaşımları olarak ikiye ayrılır.
MC kodu | Malzeme grubu | Malzeme alt grubu | İmalat prosesi | Isıl işlem | nom | Özgül kesme kuvveti,kc1 (N/mm2) | mc | ||||
S1.0.U.AN | 1 | Demir bazlı alaşımlar | 1 | Ana grup | U | Belirtilmemiş | AN | Tavlı | 200 HB | 2400 | 0,25 |
S1.0.U.AG | 1 | 2 | U | AG | Yaşlandırılmış | 280 HB | 2500 | 0,25 | |||
S2.0.Z.AN | 2 | Nikel bazlı alaşımlar | 0 | Ana grup | Z | Dövme/haddelenmiş/soğuk çekilmiş | AN | Tavlı | 250 HB | 2650 | 0,25 |
S2.0.Z.AG | 2 | 0 | Z | AG | Yaşlandırılmış | 350 HB | 2900 | 0,25 | |||
S2.0.Z.UT | 2 | 0 | Z | UT | İşlenmemiş | 275 HB | 2750 | 0,25 | |||
S2.0.C.NS | 2 | 0 | C | Döküm | NS | Belirtilmemiş | 320 HB | 3000 | 0,25 | ||
S3.0.Z.AN | 3 | Kobalt bazlı alaşımlar | 0 | Ana grup | Z | Dövme/haddelenmiş/soğuk çekilmiş | AN | Tavlı | 200 HB | 2700 | 0,25 |
S3.0.Z.AG | 3 | 0 | Z | AG | Yaşlandırılmış | 300 HB | 3000 | 0,25 | |||
S3.0.C.NS | 3 | 0 | C | Döküm | NS | Belirtilmemiş | 320 HB | 3100 | 0,25 | ||
S4.1.Z.UT | 4 | Titanyum bazlı alaşımlar | 1 | Ticari olarak saf (>99,5% Ti) | Z | Dövme/haddelenmiş/soğuk çekilmiş | UT | İşlenmemiş | 200 HB | 1300 | 0,23 |
S4.2.Z.AN | 4 | 2 | Alfa ve alfaya yakın alaşımlar | Z | AN | Tavlı | 320 HB | 1400 | | ||
S4.3.Z.AN | 4 | 3 | Alfa/Beta alaşımları | Z | AN | 330 HB | 1400 | ||||
S4.3.Z.AG | 4 | 3 | Z | AG | Yaşlandırılmış | 375 HB | 1400 | ||||
S4.4.Z.AN | 4 | 4 | Beta alaşımları | Z | AN | Tavlı | 330 HB | 1400 | | ||
S4.4.Z.AG | 4 | 4 | Z | AG | Yaşlandırılmış | 410 HB | 1400 | | |||
S5.0.U.NS | 3 | Tungsten bazlı | 0 | Ana grup | U | Belirtilmemiş | NS | Belirtilmemiş | 120 HB | | |
S6.0.U.NS | 3 | Molibden bazlı | 0 | Ana grup | U | Belirtilmemiş | NS | Belirtilmemiş | 200 HB |
HRSA malzemeleri – S 1.0-3.0
Tanım
Yüksek sıcaklıklarda sertliklerini ve mukavemetlerini koruyan yüksek korozyon dirençli malzemeler. Malzeme 1000 °C'ye kadar kullanılır ve yaşlandırma işlemiyle sertleştirilir.
- Nikel bazlı versiyon en yaygın kullanılanıdır - bir uçak motorunun ağırlığının %50'sinden fazlası. Çökeltme sertleştirilmiş malzemeler şunları içerir: Inconel 718, 706 Waspalloy, Udimet 720. Çözelti güçlendirilmiş (sertleştirilemez) şunları içerir: Inconel 625
- Demir bazlı malzeme östenitik paslanmaz çeliklerden evrimleşir ve en zayıf sıcak mukavemet özelliklerine sahiptir: Inconel 909 Greek Ascolloy ve A286
- Kobalt bazlı malzemeler en iyi sıcak sıcaklık performansına ve korozyon direncine sahiptir ve ağırlıklı olarak tıp endüstrisinde kullanılmaktadır: Haynes 25 (Co49Cr20W15Ni10), Stellite 21, 31
- HRSA malzemelerindeki ana alaşım elementleri
Ni: Yüksek sıcaklıklarda metal yapı ve malzeme özelliklerini stabilize eder
Co, Mo, W: yüksek sıcaklıklarda mukavemeti artırın
Cr, Al, Si: oksidasyona ve yüksek sıcaklık korozyonuna karşı direnci artırır
C: sürünme mukavemetini arttırır
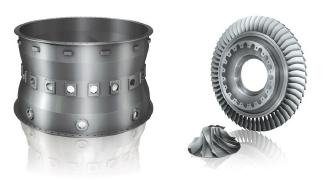
Ortak bileşenler
Yanma ve türbin bölümlerinde havacılık motor ve güç gaz türbinleri, petrol ve gaz denizcilik uygulamaları, tıbbi bağlantı implantları, yüksek korozyon dirençli uygulamalar.
İşlenebilirlik
HRSA malzemelerinin işlenebilirliği aşağıdaki sıraya göre zorluk derecesi artar: demir bazlı malzemeler, nikel bazlı malzemeler ve kobalt bazlı malzemeler. Tüm malzemeler yüksek sıcaklıklarda yüksek mukavemete sahiptir ve kesme sırasında yüksek ve dinamik kesme kuvvetleri yaratan parçalı talaşlar üretir.
Zayıf ısı iletkenliği ve yüksek sertlik, işleme sırasında yüksek sıcaklıklara neden olur. Yüksek mukavemet, deformasyon sertleşmesi ve yapışma sertleşmesi özellikleri maksimum kesme derinliğinde çentik aşınması ve kesme kenarı için son derece aşındırıcı bir ortam yaratır.
Karbür kaliteleri, plastik deformasyona karşı iyi direnç sağlamak için iyi kenar tokluğuna ve kaplamanın alt tabakaya iyi yapışmasına sahip olmalıdır. Genel olarak, geniş giriş açısına sahip kesici uçlar kullanın (yuvarlak kesici uçlar) ve pozitif kesici uç geometrisi seçin. Tornalama ve frezelemede, uygulamaya bağlı olarak seramik kaliteleri kullanılabilir.
Titanyum– S 4.1-4.4
Tanım
Titanyum alaşımları, mevcut yapılara ve alaşım elementlerine bağlı olarak dört sınıfa ayrılabilir.
- İşlem görmemiş, ticari olarak saf titanyum
- Alfa alaşımları – Al, O ve/veya N ilaveleri ile
- Beta alaşımları – Mb, Fe, V, Cr ve/veya Mn ilaveleri
- Her iki sınıfın bir karışımının mevcut olduğu karışık a+ß alaşımları
Ti-6Al-4V tipi karışık α+β alaşımları, başta havacılık sektörü olmak üzere genel amaçlı uygulamalarda şu anda kullanılmakta olan titanyum alaşımlarının çoğunluğunu oluşturmaktadır. Titanyum, çelik yoğunluğunun %60'ında mükemmel korozyon direnci ile yüksek mukavemet/ağırlık oranına sahiptir. Bu, daha ince duvarların tasarlanmasını sağlar.
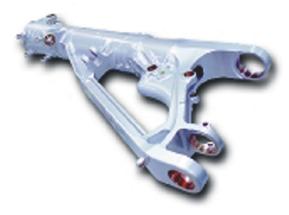
Ortak bileşenler
Titanyum, diğer inşaat malzemelerinin çoğunda önemli korozyon saldırılarına neden olabilecek çok zorlu ortamlarda kullanılabilir. Bunun nedeni, çok dayanıklı olan ve yüzeyi yaklaşık 0,01 mm kalınlığında bir tabaka halinde kaplayan titanyum oksit TiO2'dir. Oksit tabakası hasar görürse ve oksijen mevcutsa, titanyum oksidi hemen yeniden oluşturur. Havacılık alanındaki ısı eşanjörleri, tuz giderme ekipmanları, jet motoru parçaları, iniş takımları ve yapısal parçalar için uygundur.
İşlenebilirlik
Titanyum alaşımlarının işlenebilirliği, genel çeliklere ve paslanmaz çeliklere kıyasla zayıftır ve bu da kesici takımlara özel talepler getirir. Titanyumun ısıl iletkenliği zayıftır; Yüksek sıcaklıklarda mukavemet korunur, bu da kesme kenarında yüksek kesme kuvvetleri ve ısı oluşturur. Sürtünme eğilimi olan çok makaslı, ince talaşlar, kesme kenarına yakın konsantre kesme kuvvetleri oluşturarak kesme yüzeyinde dar bir temas alanı oluşturur. Çok yüksek kesme hızı, talaş ile kesici takım malzemesi arasında kimyasal reaksiyona neden olur ve bu da ani kesici uç çentikleri/kırılmaları ile sonuçlanabilir. Kesici takım malzemeleri iyi sıcak sertliğe, düşük kobalt içeriğine sahip olmalı ve titanyum ile reaksiyona girmemelidir. Genellikle ince taneli, kaplanmamış karbür kullanılır. İyi kenar tokluğuna sahip pozitif/açık bir geometri seçin.
ISO H sertleştirilmiş çelik
ISO H sertleştirilmiş çelik nedir?
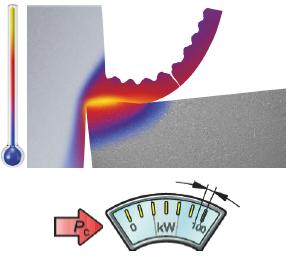
- Bu malzeme grubu, sertlikleri >45 – 68 HRC olan sertleştirilmiş ve temperlenmiş çelikleri içerir
- Yaygın çelikler arasında karbonlama çeliği (~60 HRc), bilyalı rulman çeliği (~60 HRc) ve takım çeliği (~68 HRc) bulunur. Sert dökme demir türleri arasında beyaz dökme demir (~50 HRc) ve ADI/Kymenite (~40 HRc) bulunur. İnşaat çeliği (40–45 HRc), Mn çelik ve farklı sert kaplama türleri, yani stellit, P/M çeliği ve semente karbür de bu gruba aittir
- Genelde sert parça tornalama 55-68 HRC aralığındadır
İşlenebilirlik
- Sertleştirilmiş çelik, işleme açısından en küçük gruptur ve ince talaş işleme en yaygın işleme operasyonudur. Spesifik kesme kuvveti: 2550–4870 N/mm. İşlem genellikle adil talaş kontrolü sağlar. Kesme kuvvetleri ve güç gereksinimleri oldukça yüksektir
- Kesici takım malzemesinin plastik deformasyona (sıcak sertlik), kimyasal kararlılığa (yüksek sıcaklıklarda), mekanik mukavemete ve aşındırıcı aşınmaya karşı dirence karşı iyi bir dirence sahip olması gerekir. CBN bu özelliklere sahiptir ve taşlama yerine tornalamaya olanak tanır
- Karma veya yayla güçlendirilmiş seramik, iş parçasının orta düzeyde yüzey kalitesi taleplerine sahip olduğu ve sertliğin karbür için çok yüksek olduğu tornalamada da kullanılır
- Semente karbür frezeleme ve delik delme uygulamalarında baskındır ve yaklaşık 60 HRc'ye kadar kullanılır
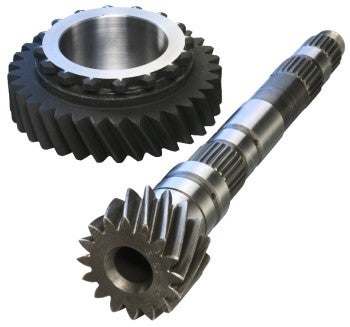
Ortak bileşenler
Tipik bileşenler şunları içerir: şanzıman milleri, dişli kutusu muhafazaları, direksiyon pinyonları, damgalama kalıpları.
Sertleştirilmiş çelik için MC kodları
| |||||||||||
MC kodu | Malzeme grubu | Malzeme alt grubu | İmalat prosesi | Isıl işlem | Nom | Spesifik kesme kuvveti, kc1 (N/mm2) | mc | ||||
H1.1.Z.HA | 1 | Çelikler (ekstra sert) | 1 | Sertlik derecesi 50 | Z | Dövme/haddelenmiş/soğuk çekilmiş | HA | Sertleştirilmiş (+temperlenmiş) | 50 HRc | 3090 | 0,25 |
H1.2.Z.HA | 1 | 2 | Sertlik derecesi 55 | Z | HA | 55 HRc | 3690 | 0,25 | |||
H1.3.Z.HA | 1 | 3 | Sertlik derecesi 60 | Z | HA | 60 HRc | 4330 | 0,25 | |||
H1.4.Z.HA | 1 | 4 | Sertlik derecesi 63 | Z | HA | 63 HRc | 4750 | 0,25 | |||
H2.0.C.UT | 2 | soğutulmuş dökme demir | 0 | Ana grup | C | döküm | UT | işlenmemiş | 55 HRc | 3450 | 0,28 |
H3.0.C.UT | 3 | stellitler | 0 | Ana grup | C | döküm | UT | belirtilmemiş | 40 HRc | | |
H4.0.S.AN | 4 | Ferro-TiC | 0 | Ana grup | S | sinterlenmiş | AN | tavlı | 67 HRc | | |