Varma ratkaisu mikrovikojen voittamiseen
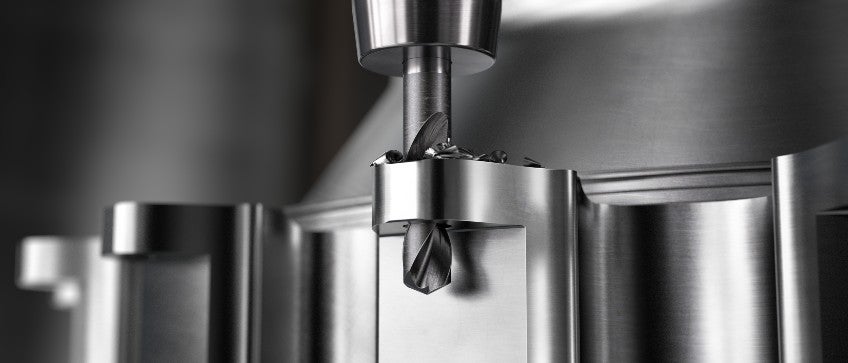
Entistä paremmin suunnitellun kovametalliporan testaaminen avaa uusia reikien laatuun liittyviä mahdollisuuksia.
”Mittaa kahdesti ja leikkaa kerran” on tuttu lausahdus valmistuksen maailmassa, mutta vaikeiden materiaalien koneistuksessa se on helpommin sanottu kuin tehty. Siksi eräs johtava globaali ilmailualan valmistaja kääntyi metallin lastuamisen maailmanlaajuisen johtajan puoleen, kun se halusi karsia porausprosesseistaan pois kokonaisen toisen vaiheen ja samalla parantaa ilmailualan komponenttiensa reikien laatua. Nyt Sandvik Coromantin globaali tuotepäällikkö James Thorpe kertoo, miten poramallin avulla voidaan tuottaa laadukkaampia reikiä.
Reikien tekeminen on kaikista yleisin koneistusprosessi, mutta sitä pidetään myös eniten itsestäänselvyytenä. Monissa konepajoissa ei ole nähty syytä vaihtaa tai päivittää olemassa olevia reikien valmistusjärjestelmiä, joten niissä on käytetty samoja työkaluja ja lastuamisparametreja vuodesta toiseen. Tämä kaikki on nyt kuitenkin muuttumassa koronapandemian odottamattomien vaikutusten myötä. Valmistajat ovat kokeneet odottamattomia ja pysyviä asiakasmarkkinoiden muutoksia, joten niillä on nyt tarve mukauttaa tuotantoaan.
Useimmat valmistajat tarkastelevat nyt esimerkiksi uusia toimittajakantoja ja tuotteita. Siksi aikoinaan tiettyihin tuotantoalueisiin erikoistuneiden konepajojen CNC-sorveissa ja jyrsimissä on nyt alettu käsitellä monipuolisemmin erilaisia kovia ja haastavia materiaaleja. Samalla valmistajien on myös etsittävä uusia tapoja kasvattaa tuottoa ja nopeuttaa työkiertoja tuotteiden laadusta tinkimättä.
Valmistajien on siis uudistettava koko reikien valmistusprosessinsa.
Katse kohti valkoista kerrosta
Reikäpinnan eheys on todellinen haaste ilmailuteollisuuden valmistajille ja yleisen tekniikan alalla toimiville yrityksille, jotka haluavat laajentaa toimintaansa ilmailualan puolelle. Reiän parempi laatu ehkäisee komponenttivikoja, ja siihen vaikuttavat etenkin reikien koneistuksessa tai viimeistelyssä käytettävät valmistusprosessit.
Työkaluratkaisut ja porien teräsärmän geometriat kehittyvät jatkuvasti tiukimpien valmistusta ja osien laatua koskevien vaatimusten täyttämiseksi. Myös lastuamisnesteen käyttöä parannetaan työkalun kuumentumisen hillitsemiseksi. Kokeissa onkin käynyt ilmi, että kaikilla näillä tekijöillä voidaan hallita työkappaleen aineen niin sanottua valkoista kerrosta.
Nimityksen keksi eräs ilmailuteollisuuden johtava globaali valmistaja, joka on myös Sandvik Coromantin asiakas. Nimitys viittaa ohueen, erittäin hienorakeiseen rakenteeseen, jonka poran kuumuus saa aikaan porattavassa komponentissa. Valkoinen kerros saattaa muuttaa materiaalin pintaominaisuuksia, ja sitä ei myöskään pidetty hyväksyttävänä asiakkaan laadunhallintaprosesseissa.
Valmistajalla on tiukka porattujen reikien viimeistelyprosessi turbiinikiekkojen, kompressorien, rumpujen ja akselien kaltaisten ilmailuteollisuuden komponenttien käsittelyssä. Siksi valmistaja päätti ryhtyä yhteistyöhön Sandvik Coromantin kanssa saadakseen selville, miksi valkoinen kerros muodostuu ja miten sitä voidaan hallita.
Kokeita haluttiin tehdä myös muista kuin laadunhallintaan liittyvistä syistä. Asiakkaan ylemmän johdon tasolla haluttiin nopeuttaa kokonaiskäsittelyaikaa ja kasvattaa tuottoa karsimalla käsittelystä pois kokonainen toissijainen koneistusprosessi.
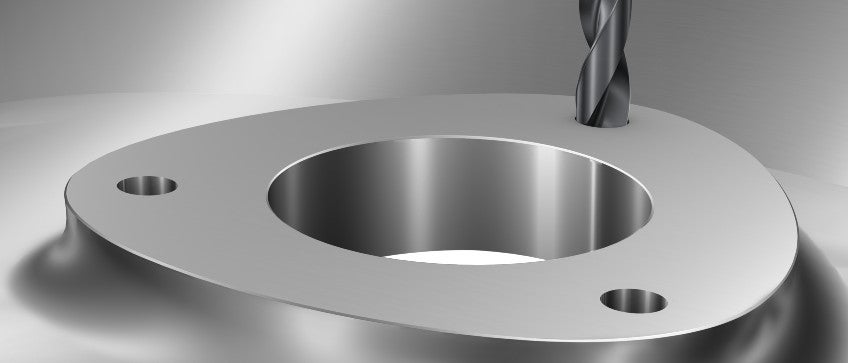
Reikäpinnan eheys on todellinen haaste ilmailuteollisuuden valmistajille ja yleisen tekniikan yrityksille, jotka haluavat laajentaa toimintaansa ilmailualan puolelle. HRSA-kotelon kohoumaporaus onnistuu -SM-geometrialla varustetulla CoroDrill 860 ‑poralla erinomaisesti
.
Toinen vaihe
Toissijainen prosessi seuraa sen jälkeen, kun reikä on porattu kovametalliporalla, ja prosessiin voi sisältyä kalvintaa, pistojyrsintää tai loppujyrsintää työkappaleen viimeistelemiseksi. Toissijainen vaihe tarvitaan mittatarkkuuden sijaan pääasiassa pinnan eheyttä koskevien vaatimusten täyttämiseksi eli esimerkiksi valkoisen kerroksen kaltaisten ongelmien hillitsemiseksi. Poikkeuksena tästä on kuitenkin toleranssiltaan tiukkojen reikien koneistus, jossa mittatarkkuus on tärkeämpi tekijä.
Toissijaisen prosessin käyttäminen on kokonaiskustannusten näkökulmasta vieläkin kalliimpaa kuin pienten lastuamisarvojen ylläpitäminen, joka on toinen keino pinnan eheyden säilyttämiseen. Siksi Sandvik Coromantin asiakas halusi selvittää, voitaisiinko prosessista hankkiutua kokonaan eroon. Jos toimittajan tuotteella voidaan tehdä oikeankokoisia reikiä ilman lisäprosesseja, toimittaja saa vankan liiketoiminta-aseman, kun osakustannuksia voidaan vähentää merkittävästi.
Valkoisen kerroksen aiheuttajien ja mahdollisten ratkaisujen selvittäminen sisälsi neljä koetta, joissa porattiin erittäin lujaa, nikkelistä ja kromista valmistettua Inconel 718 ‑materiaalia, joka on ilmailuteollisuuden suosima raaka-aine. Kyseessä oli ensimmäinen kerta, kun asiakas toteutti tällaisen selvityksen.
Kokeissa arvioitiin poraamista Sandvik Coromantin CoroDrill® R840- ja CoroDrill® R846 ‑täysikovametalliporilla. Kumpaakin käytettiin kahdella erilaisella lastuamisparametrijoukolla. Toisen poran syöttö oli 58 mm/min ja kiertonopeus 829 kierr./min, kun taas toisella poralla arvot olivat 98 mm/min ja 757 kierr./min. Sekä lastuamisvoimia, vääntömomenttitietoja että valkoisen kerroksen paksuutta mitattiin koko kokeiden ajan.
Sittemmin CoroDrill R840:n on korvannut -GM-geometrialla varustettu CoroDrill® 860, ja CoroDrill R846:n seuraajaksi on tullut CoroDrill® 860 -SM-geometrialla. Molemmat näistä uuden sukupolven työkaluista on suunniteltu pidentämään työkalujen kestoikää entisestään reikien laadusta tinkimättä.
Tulosten pohjalta saatiin arvokasta tietoa siitä, mikä vaikuttaa valkoisen kerroksen paksuuteen. Huomionarvoista oli etenkin se, että CoroDrill R846 aiheutti kaarevien ja radiaalisten teräsärmiensä ansiosta vähemmän valkoisen kerroksen muodostumista. CoroDrill R840:n suorien teräsärmien ja teräsärmäviisteen puolestaan uskotaan liittyvän suurempaan lastuamisvoimaan, vääntömomenttiin ja valkoisen kerroksen paksuuteen. Riippuu siis poran muotoilusta, voidaanko korkea reikien laatu ja pienempi valkoinen kerros saavuttaa lastuamisarvoista tinkimättä.
Globaalin ilmailuteollisuusvalmistajan ja Sandvik Coromantin kokeissa saatiin mielenkiintoista tietoa valkoisesta kerroksesta, ja lisäksi yritys on nyt onnistunut karsimaan joitakin toissijaisia prosessejaan, kuten kalvinnan ja pistojyrsinnän, minkä ansiosta se on säästänyt sekä aikaa että rahaa. Kaiken lisäksi tulokset ovat osoittaneet Sandvik Coromantin CoroDrill 860 ‑sarjan kovametalliporien muotoilun toimivuuden.
Parempaa muotoilua
Sarjaan kuuluu edellä mainittu -GM-geometrialla varustettu CoroDrill 860, joka on suunniteltu hyväksi yleisporaksi haastavien ISO P-, M-, K- ja H-materiaalien poraamiseen kaikilla teollisuudenaloilla. CoroDrill 860 -SM-geometrialla on optimoitu kuumalujien superseosten (HRSA:t), titaanin ja Inconelin kaltaisten ISO S ‑laatujen koneistukseen. Porasta on tullut erityisen suosittu ilmailuteollisuudessa.
Sandvik Coromantin insinöörit suunnittelivat -GM-geometrialla varustetun CoroDrill 860:n ja -SM-geometrialla varustetun CoroDrill 860:n sen periaatteen pohjalta, että pidempi työkalujen kestoikä ja parempi reikien laatu riippuvat poran muotoilusta. -GM-geometrialla varustetussa CoroDrill 860 ‑porassa on uraauurtava kiillotettu lastu-ura, joka parantaa lastujen poistamista, varmistaa erinomaisen ydinlujuuden ja vähentää terään kohdistuvia voimia porauksen aikana.
-SM-geometrialla varustetulla CoroDrill 860 ‑poralla on puolestaan uusi laatu sekä optimoitu ja viimeistelty kärkigeometria, joka pidentää työkalujen kestoikää vaikeasti koneistettavien HRSA-materiaalien käsittelyssä entisestään. Näin lopputulokseksi saadaan parempi reikien laatu.
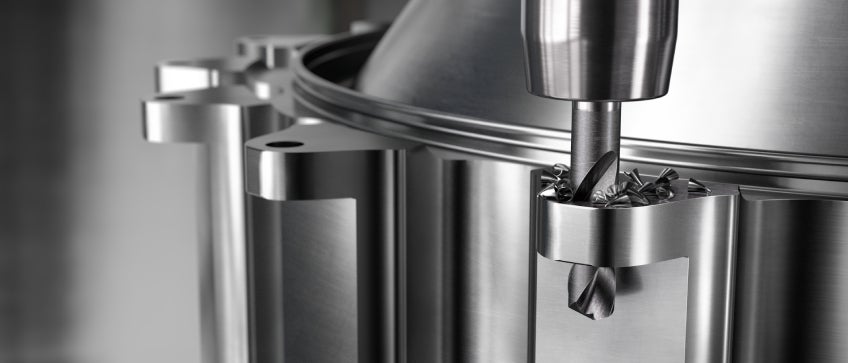
-SM-geometrialla varustettu CoroDrill 860 on suunniteltu sen periaatteen pohjalta, että pidempi työkalujen kestoikä ja parempi reikien laatu riippuvat poran muotoilusta.
CoroDrill 860:n tehokkuus on jo todistettu ennen markkinoille saattamista toteutetuissa kokeissa useilla eri toimialoilla. Ranskalainen mekaaniseen tekniikkaan erikoistunut yritys kokeili -GM-geometrialla varustettua CoroDrill 860 ‑poraa AISI 4140 ‑rakenneteräksen käsittelyssä. Poralla onnistuttiin tekemään laadukkaita reikiä sekä koveralla että kuperalla sisäänsyötöllä, ja sekä suoruus- että toleranssitulokset olivat erinomaiset. Yritys on sittemmin solminut Sandvik Coromantin kanssa uuden liikesuhteen.
Toinen Sandvik Coromantin asiakas, italialainen yleiseen tekniikkaan erikoistunut valmistaja, onnistui kasvattamaan tuottavuutta yli 45 prosenttia kilpailevaan poraan verrattuna käyttämällä -GM-geometrialla varustettua CoroDrill 860 ‑poraa lujan 34CrNiMo6-terässeoksen koneistuksessa. Myös työkalujen kestoikä saatiin kaksinkertaistettua. -SM-geometrialla varustetulla CoroDrill 860 ‑poralla on saatu aikaan vaikuttavia tuloksia myös Inconel 718:n koneistuksessa. Puolan Katowicessä tehdyissä kokeissa -SM-geometrialla varustetulla CoroDrill 860 ‑poralla saavutettiinkin 180 prosenttia parempi työkalujen kestoikä kuin CoroDrill R840:llä.
Erinomainen työkalujen tehokkuus on saavutettavissa kaikilla toimialoilla, kuten ilmailuteollisuudessa tai yleisessä tekniikassa, kunhan tarvittuun tehtävään valitaan asianmukaisesti suunniteltu pora. Sandvik Coromantin CoroPlus®-työkaluoppaan kaltaisilla verkkopohjaisilla lisätyökaluilla voidaan tarjota lisää tukea. Käyttämällä työkalua verkkoselaimessa ja syöttämällä halutun työkappaleen aineen sekä reiän halkaisijan ja syvyyden käyttäjät voivat löytää tarpeisiinsa parhaan täyskovametallisen työkalun ja sopivimmat lastuamisarvot.
Vaikka ”mittaa kahdesti ja leikkaa kerran” ‑periaatteen mukainen poraaminen onkin jäänyt vielä saavuttamatta, -GM-geometrialla varustettu CoroDrill 860 ja -SM-varustettu CoroDrill 860 auttavat valmistajia poraamaan uusilla tavoilla.