Un avenir plus vert pour l'aéronautique
Les équipementiers doivent adopter une approche globale de l'avion de demain.
Une forte pression pèse sur l'industrie aéronautique, l'un des principaux responsables des émissions de CO2 dans le monde, pour qu'elle produise des avions plus écologiques, plus légers et capables de parcourir de plus longues distances. Toutefois, pour y parvenir, il faut travailler avec de l'aluminium et des superalliages réfractaires difficiles à usiner. Sébastien Jaeger, Directeur Solution industrielle – Aéronautique pour Sandvik Coromant, explique ici comment les équipementiers de cette industrie peuvent adopter des solutions d'outillage avancées pour usiner durablement ces composants difficiles.
Selon le Forum économique mondial (FEM), « atteindre les objectifs d'émissions nettes de CO2 nulles à l'horizon 2050 contribuera non seulement à créer un avenir écologiquement durable, mais aussi à préserver la résilience financière et la compétitivité du secteur de l'aviation dans son ensemble. » Cependant, bien que l'e-mobilité se soit progressivement imposée dans l'automobile, et qu'en août 2021 les ventes de véhicules électriques aient dépassé les ventes de véhicules diesel au Royaume-Uni, ces avancées prendront plus de temps à se concrétiser dans l'aéronautique.
De manière générale, l'utilisation des avions électriques ne devrait pas se généraliser avant 2035. Selon Lonely Planet, bien qu'easyJet espère utiliser des avions électriques sur les trajets de moins de 500 km d'ici à 2030 et que la Norvège souhaite rendre tous les vols court-courriers électriques d'ici à 2040, « nous ne sommes pas près de voler sur des avions gros-porteurs rechargeables sur les longs-courriers : les batteries sont tout simplement trop lourdes. »
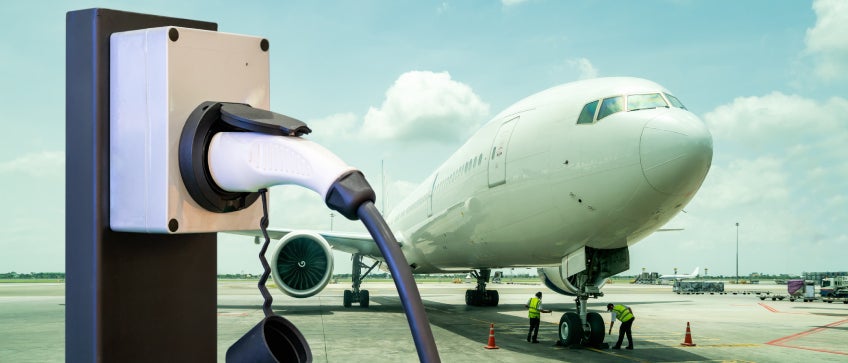
L'utilisation des avions électriques devrait se généraliser d'ici 2035.
Ainsi, si les batteries doivent devenir plus légères pour être envisageables, il incombe également aux équipementiers de fabriquer des composants plus légers pour contrebalancer le problème. Nous sommes certains que l'aluminium, et plus précisément de nouveaux types d'aluminium dotés d'une plus grande solidité, d'une meilleure résistance à la fatigue et d'autres attributs, permettra d'alléger ces systèmes.
Nous constatons également une utilisation accrue des nouveaux superalliages réfractaires. En fait, les superalliages réfractaires sont déjà utilisés dans les pièces d'avion qui doivent répondre à des exigences de performance extrêmes, car ils conservent leur dureté dans les conditions de chaleur intense. Les propriétés de ces matières s'avéreront essentielles, car l'une des approches pour un transport aérien plus durable consistera à faire brûler les moteurs plus fort et plus chaud.
Les composants doivent également être fabriqués avec des tolérances plus serrées et des conceptions plus variées. Comme pour les automobiles électriques, la conception des avions électriques de demain, notamment les fuselages et les moteurs, variera davantage d'un constructeur à l'autre que celle des avions à moteur à combustion interne existants. En ce qui concerne le fuselage, certains équipementiers explorent les concepts de forme delta, de corps d'aile mixte et d'aile haubanée. D'autres équipementiers s'en tiennent à la conception traditionnelle « un gros tube, des ailes et un moteur ».
Les moteurs se présenteront également sous différentes formes : moteurs électriques, alimentés par batterie ou électromagnétiques, ou encore moteurs hybrides dans lesquels les moteurs traditionnels sont assistés par des moteurs électriques. Les équipementiers devront fabriquer un nombre croissant de composants avec des tolérances serrées et trouver de nouveaux moyens de réduire le bruit, le poids et les émissions, autant de facteurs qui influencent les performances des systèmes électriques. Mais les composants en aluminium et en superalliages réfractaires sont difficiles à usiner, et il sera donc difficile d'y parvenir de manière durable et rentable.
Des progrès rapides
Une solution pour produire des avions plus légers et plus économes en carburant consiste à utiliser les techniques de fabrication additive (FA). La fabrication additive permet de créer des pièces sur mesure de forme très complexe et des produits fonctionnels avec des tolérances serrées. Les pièces difficiles à usiner, comme les treillis, peuvent ainsi être usinées plus facilement. Selon les conclusions de la société de logiciels Dassault Systemes, « dans le secteur aéronautique, la réduction du poids grâce aux processus de fabrication additive peut entraîner des économies d'énergie allant jusqu'à 25 % », tandis que « chaque kilogramme de poids en moins sur un vol peut permettre d'économiser jusqu'à 3 000 dollars de carburant par an ».
Mais la fabrication additive elle-même est-elle durable ? Une étude, cosignée par le département d'ingénierie de la fabrication de l'université technique roumaine de Cluj-Napoca, décrit la fabrication additive comme « une excellente alternative aux méthodes de fabrication traditionnelle telles que le moulage par injection, le moulage sous pression ou l'usinage ». Cette étude précise également : « La fabrication additive est susceptible de réduire les coûts et d'être plus économe en énergie que les processus conventionnels. »
La fabrication additive aura également un effet déterminant sur la méthode et la diversité de la fabrication des produits. Les avantages sont multiples : réduction des émissions de carbone, diminution de la quantité de matériaux utilisés et baisse du transport, car les pièces peuvent être fabriquées sur place plutôt qu'importées.
Les fabricants peuvent également produire des pièces aéronautiques plus complexes, plus compactes et plus innovantes grâce au prototypage rapide. Le prototypage rapide fait référence à plusieurs techniques, mais l'objectif est de produire rapidement un prototype 3D tangible à partir d'un fichier de conception assistée par ordinateur (CAO). Grâce à ces prototypes, il est possible d'effectuer des essais en petit volume de nouveaux matériaux avant la fabrication à grande échelle. Ainsi, les composants sont fabriqués avec un niveau d'innovation, de qualité et de précision maximal.
Nous avons étudié les méthodes que les équipementiers aéronautiques peuvent adopter pour fabriquer des composants plus complexes. Mais qu'en est-il du choix d'outils adaptés à la tâche, en particulier pour l'usinage d'aluminium et de superalliages réfractaires ?
Ces matériaux nécessitent l'utilisation d'outils présentant une plus grande résistance à l'usure et une durée de vie plus longue. C'est pourquoi Sandvik Coromant a développé la nuance S205 pour les plaquettes en acier destinées au tournage. La métallurgie de la nuance S205 intègre une couche Inveio® de cristaux unidirectionnels très serrés, qui crée une solide barrière protectrice autour de la plaquette et renforce ses propriétés mécaniques. La plaquette a déjà fait ses preuves dans la fabrication d'une série de composants aéronautiques, notamment des disques, des anneaux et des arbres de turbine de moteur. Les clients de Sandvik Coromant ont déjà fait état de vitesses de coupe 30 à 50 % plus élevées avec la nuance S205 par rapport aux superalliages réfractaires concurrents.
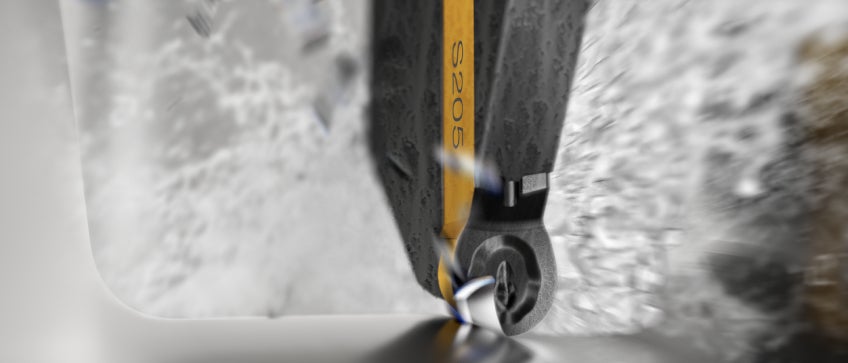
Une approche globale
Nous avons étudié les process et les outils de fabrication, mais comment combiner au mieux les deux ? Après tout, l'élaboration d'une solution entièrement intégrée peut être une perte de temps si les systèmes ne sont pas conçus pour fonctionner ensemble.
C'est pourquoi Sandvik Coromant accompagne ses clients de l'aéronautique en leur proposant une solution à composants. La solution se déroule en plusieurs étapes, notamment l'examen des besoins en machines et les calculs de temps pour déterminer le coût par composant. Également, l'analyse des méthodes de fabrication à la mise en route, en relation à la fois avec les méthodes de mesure du temps et les process des utilisateurs finaux. La solution à composants inclut également la programmation de la fabrication assistée par ordinateur (FAO) et la gestion de projets locaux ou transfrontaliers.
Pour un client de Sandvik Coromant qui rencontrait des problèmes de rupture des copeaux dans sa production, la solution à composants nous a permis d'identifier la cause et de trouver une solution. Pour ce client, les spécialistes de Sandvik Coromant ont élaboré une nouvelle stratégie avec des courbes d'entraînement dynamiques qui nous ont permis de maîtriser la rupture des copeaux à chaque instant. Nous avons appelé cette nouvelle approche « scoop turning » et nous en détenons à présent le brevet. Avec le scoop turning, le client a réussi à réduire de 80 % le temps de cycle avec un excellent contrôle des copeaux et une durée de vie de l'outil doublée.
De plus, le client a pu ramener son utilisation de quatre à une seule machine. Il a ainsi pu réduire le recours au multitâche, avec des process d'usinage plus sûrs et une production Green light production. Le recours à un nombre réduit de machines et la possibilité de réaliser des séries de production avec moins de changements d'outils, grâce à des nuances plus résistantes comme la S205, seront les clés d'une production aéronautique plus durable.
Les logiciels joueront également un rôle essentiel, comme le CoroPlus® Tool Guide qui fait partie du portefeuille numérique de Sandvik Coromant. Les clients peuvent ainsi décider du choix de l'outil et des paramètres de coupe avant même d'avoir commencé la production.
Boucler la boucle
Outre les nouvelles approches en matière d'outils et de fabrication, les équipementiers aéronautiques peuvent également se tourner vers la fabrication. Selon un rapport de l'Air Transport Action Group (ATAG), Kaiser, qui est la société qui fournit l'aluminium à Boeing, utilise désormais un système de recyclage en circuit fermé, l'un des plus grands programmes de ce type dans l'industrie. Kaiser estime que, grâce à ce programme, environ dix millions de kilogrammes de chutes et de déchets métalliques seront réutilisés par l'industrie, chaque année.
Sandvik Coromant a lancé son propre système circulaire de recyclage des outils en carbure, qui consiste à racheter les outils en carbure usagés des clients et à les réutiliser pour en fabriquer de nouveaux. Ainsi, la majeure partie des matières premières utilisées dans les outils en carbure cémenté de Sandvik Coromant proviennent des rebuts. Nos activités sont plus durables dans un environnement où les ressources sont limitées, et nous réduisons la quantité de déchets. Grâce à cette approche, nous avons constaté que la fabrication d'outils à partir de carbure recyclé utilise 70 % d'énergie en moins et émet 40 % de CO2 en moins.
Une pression croissante pèse sur l'industrie aéronautique pour qu'elle fabrique des avions plus écologiques, plus légers et capables de parcourir de plus longues distances. Toutefois, avec les bons process et outils, sans parler d'une approche plus globale de la fabrication, les équipementiers de l'aéronautique peuvent contribuer à construire un avenir plus vert pour l'aéronautique.