Matériaux de coupe

Introduction
Le choix d'un matériau et d'une nuance de coupe est un facteur important pour la réussite d'une opération d'usinage.
Pour effectuer un bon choix pour une application donnée, il convient d'avoir une connaissance de base des propriétés des matériaux de coupe et de leurs performances. Les critères de choix incluent la matière à usiner, le type et la taille de la pièce, les conditions d'usinage et l'état de surface requis pour chaque opération.
Cette rubrique donne des informations utiles sur les matériaux de coupe, leurs propriétés et leurs utilisations.
Les matériaux de coupe ont des propriétés différentes en termes de dureté, de ténacité et de résistance à l'usure. Ils sont divisés en un grand nombre de nuances dotées de propriétés spécifiques. De manière générale, les matériaux de coupe doivent posséder les propriétés suivantes :
- Dureté : résistance à l'usure en dépouille et à la déformation
- Ténacité : résistance à la rupture
- Neutralité chimique : absence de réaction chimique avec la matière usinée
- Stabilité chimique : résistance à l'oxydation et à la diffusion
- Résistance aux variations thermiques brusques
Matériau de coupe : carbure cémenté
- Revêtement – CVD
- Revêtement – PVD
- Carbure cémenté
Qu'est-ce que le carbure cémenté ?
Le carbure cémenté représente 80 à 90 % de toutes les plaquettes. La popularité de ce matériau de coupe est due autant à sa ténacité et sa résistance à l'usure qu'à sa capacité à être formé en géométries complexes.
Le carbure cémenté revêtu comporte un substrat en carbure cémenté et un revêtement de surface. L'ensemble constitue une nuance optimisée pour un champ d'applications donné.
Les nuances carbure cémenté revêtues sont le premier choix pour toute une variété d'outils et d'applications.
Revêtement – CVD
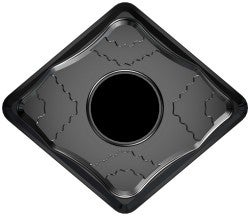
Définition et propriétés
CVD signifie dépôt chimique en phase vapeur. Ce type de revêtement est donc créé par réaction chimique à haute température, 700 à 1050°C.
Les revêtements CVD ont une grande résistance à l'usure et une forte adhérence au substrat carbure.
Le premier revêtement de ce type était composé d'une couche unique de carbure de titane (TiC). Les revêtements d'oxyde d'aluminium (Al2O3) et de nitrure de titane (TiN) sont plus récents. Les revêtements CVD de dernière génération incluent le carbonitrure de titane (MT-Ti(C,N) et MT-TiCN, aussi appelés revêtements MT-CVD). Ils ont été développés pour améliorer les propriétés des nuances, notamment grâce à leur capacité à protéger l'interface avec le substrat carbure cémenté.
Les revêtements CVD modernes combinent plusieurs couches MT-Ti(C,N), Al2O3 et TiN. Les propriétés des revêtements ont fait l'objet de recherches pour améliorer leur adhérence, leur ténacité et leur résistance à l'usure au moyen d'optimisations de la micro structure et de post traitements. Voir la technologie Inveio™.
MT-Ti(C,N) - Résistance à l'usure par abrasion grâce à la dureté. Usure en dépouille réduite.
CVD-Al2O3 - Neutralité chimique avec faible conductivité thermique, résistance à l'usure en cratère. Fait office de barrière thermique améliorant la résistance à la déformation plastique.
CVD-TiN - Meilleure résistance à l'usure et facilite la détection de l'usure.
Post traitements - Meilleure ténacité d'arête dans les coupes interrompues, réduction de la tendance au collage.
Applications
Les nuances avec revêtement CVD sont le premier choix dans une grande variété d'applications où la résistance à l'usure est importante. Il s'agit d'applications de tournage général et d'alésage dans les aciers pour lesquelles les revêtements CVD épais apportent une meilleure résistance à l'usure en cratère, d'applications de tournage d'aciers inoxydables et d'applications de fraisage de matières ISO P, M et K. En perçage, les nuances CVD sont généralement utilisées sur la plaquette périphérique.
Revêtement – PVD
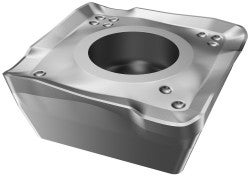
Définition et propriétés
Les revêtements PVD sont obtenus par dépôt physique en phase vapeur à température relativement basse (400 à 600°C). Ce procédé consiste à faire évaporer un métal qui entre alors en réaction avec un gaz, par exemple de l'azote, pour former une couche dure de nitrure sur la surface des plaquettes.
Ces revêtements sont très durs et ils améliorent la résistance à l'usure. Leurs contraintes de compression augmentent aussi la ténacité d'arête et la résistance à l'usure en peigne. Voir la technologie Zertivo™.
Les principaux composants des revêtements PVD sont décrits ci-dessous. Les revêtements modernes combinent plusieurs de ces composants sous la forme de couches successives ou de revêtements lamellaires. Les revêtements lamellaires comportent de nombreuses couches fines, de l'ordre du nanomètre, qui constituent un revêtement encore plus dur.
PVD-TiN - Le nitrure de titane a été le premier revêtement PVD utilisé. Il possède des propriétés polyvalentes et une couleur dorée.
PVD-Ti(C,N) - Le carbonitrure de titane est plus dur que le nitrure de titane. Il apporte une meilleure résistance à l'usure en dépouille.
PVD-(Ti,Al)N - Le nitrure de titane aluminium a une grande dureté qui se combine à une résistance à l'oxydation. La résistance générale à l'usure est meilleure.
PVD-oxyde - Utilisé pour sa neutralité chimique et sa meilleure résistance à l'usure en cratère.
Applications
Les nuances avec revêtement PVD sont recommandées pour leurs arêtes à la fois tenaces et vives. Elles sont aussi particulièrement bien adaptées à l'usinage de matières collantes. Leurs champs d'applications sont nombreux ; ils incluent les fraises monobloc en bout et les forets monobloc ainsi que la majorité des nuances pour les gorges, le filetage et le fraisage. Les nuances à revêtement PVD sont aussi très largement utilisées pour les applications de finition ainsi que pour la plaquette centrale des forets à plaquettes indexables.
Carbure cémenté
Définition et propriétés
Le carbure cémenté est un produit de la métallurgie des poudres. Il est composé de particules de carbure de tungstène (WC) mélangées à un liant riche en cobalt métallique (Co). Les carbures cémentés utilisés pour la coupe des métaux comportent plus de 80 % de WC en phase solide. D'autres carbonitrures cubiques peuvent aussi être utilisés, surtout dans les nuances frittées gradientes. Le corps en carbure cémenté est formé soit par pressage de poudre, soit par moulage par injection. Il est ensuite fritté pour atteindre sa pleine densité.
La taille des grains de carbure (WC) est le paramètre le plus important pour la ténacité et la dureté des nuances. Plus le grain est fin, plus la nuance est dure, pour une teneur en liant constante.
La teneur en liant cobalt et sa composition contrôle la ténacité et la résistance à la déformation plastique de la nuance. A taille de grain égale, plus la teneur en liant est élevée, plus la nuance est tenace et plus elle est sensible à la déformation plastique. Si la teneur en liant est trop faible, le matériau devient friable.
Les carbonitrures cubiques, aussi appelés phase γ, sont en général ajoutés pour augmenter la résistance à chaud et pour former des gradients.
Les gradients servent à améliorer à la fois la résistance à la déformation plastique et la ténacité d'arête. Les carbonitrures cubiques concentrés dans l'arête améliorent à dureté à chaud. Un substrat avec un liant riche en carbure de tungstène au delà de l'arête réduit la formation de fissures et les fractures dues au martèlement des copeaux.
Applications
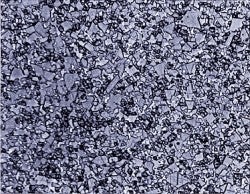
Grain WC de taille moyenne à grosse
Une taille de grain carbure moyenne à grosse confère au carbure cémenté une dureté à chaud et une ténacité élevées. Avec des revêtements CVD ou PVD, ces substrats permettent de décliner des nuances pour tous les champs d'applications.
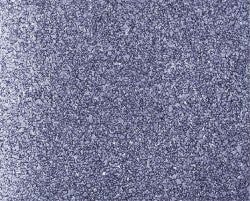
Grain fin et grain submicronique
Les substrats à grain carbure fin ou submicronique servent à créer des arêtes vives avec revêtement PVD augmentant leur résistance. Les nuances de ce type ont aussi une très bonne résistance aux charges thermiques et mécaniques cycliques. Elles sont beaucoup utilisées pour les forets carbure monobloc, les fraises en bout carbure monobloc, les plaquettes de tronçonnage et gorges, le fraisage et la finition.
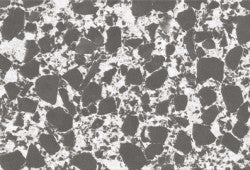
Carbure cémenté gradient
L'avantage des propriétés doubles des gradients est exploité conjointement avec des revêtements CVD pour produire des nuances de premier choix pour le tournage, le tronçonnage et les gorges dans les aciers et les aciers inoxydables.
Matériau de coupe carbure cémenté non revêtu
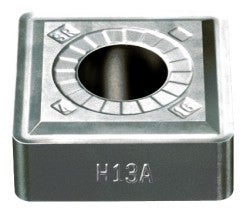
Qu'est-ce que le carbure cémenté non revêtu ?
Les nuances carbure non revêtues représentent une très petite partie du programme complet de nuances. Ces nuances sont composées de WC/Co ou peuvent contenir un volume élevé de carbonitrures cubiques.
Applications
Les applications typiques sont l'usinage des superalliages réfractaires et alliages de titane, et le tournage de matières trempées à faible vitesse.
L'usure des nuances carbure cémenté non revêtu est rapide mais contrôlée, avec un auto affûtage.
Matériau de coupe cermet
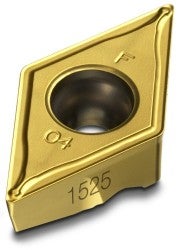
Qu'est-ce que le cermet ?
Une nuance cermet est composée de carbure cémenté avec particules dures à base de titane. Le nom cermet est composé à partir du mot céramique et du mot métal. À l'origine, le cermet était un composé de TiC et de nickel. Les nuances cermet modernes ne contiennent plus de nickel. Elles ont une structure basée sur des particules de carbonitrure de titane Ti(C,N), une seconde phase solide de (Ti,Nb,W)(C,N) et un liant cobalt riche en W.
Le Ti(C,N) apporte une meilleure résistance à l'usure à la nuance, la seconde phase solide augmente la résistance à la déformation plastique et la teneur en cobalt contrôle la ténacité.
Par rapport au carbure cémenté, le cermet possède une meilleure résistance à l'usure et une tendance réduite au collage. Mais il a aussi une moins bonne résistance à la compression et aux chocs thermiques. Les nuances cermet peuvent aussi avoir un revêtement PVD pour une meilleure résistance à l'usure.
Applications
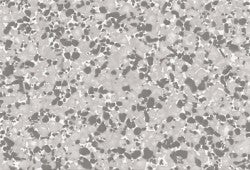
Les nuances cermet s'utilisent dans les applications avec des matières collantes où le risque d'arête rapportée est élevé. Leur schéma d'usure avec auto affûtage permet de conserver des forces de coupe réduites même après un temps de coupe prolongé. Dans les opérations de finition, la durée de vie d'outil est longue et les tolérances sont serrées. Les états de surface obtenus sont brillants.
Les applications typiques sont la finition des aciers inoxydables, des fontes nodulaires, des aciers bas carbone et des aciers ferritiques. Les cermets peuvent aussi servir pour résoudre les problèmes dans toutes les matières ferreuses.
Indications utiles :
- Utiliser une faible avance et une faible profondeur de coupe
- Changement d'arête lorsque l'usure en dépouille atteint 0.3 mm
- Ne pas utiliser d'arrosage afin d'éviter les fissures thermiques et les fractures
Matériau de coupe céramique
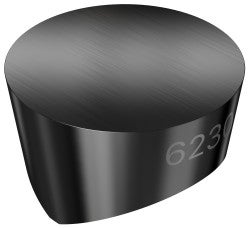
Qu'est-ce que la céramique ?
Tous les outils de coupe céramique ont une excellente résistance à l'usure à grande vitesse de coupe.
Il existe toute une gamme de nuances céramiques pour une grande variété d'applications.
Les céramiques à base d'oxyde contiennent de l'oxyde l'aluminium (Al2O3) additionné de zirconium (ZrO2) pour l'inhibition des fissures. Ce matériau a une très grande stabilité chimique mais il manque de résistance aux chocs thermiques.
(1) Les céramiques mélangées sont renforcées par l'ajout de carbures cubiques ou de carbonitrures (TiC, Ti(C,N)). Elles ont une meilleure ténacité et une bonne conductivité thermique.
(2) Les céramiques à whiskers contiennent des whiskers de carbure de silicium (SiCw) qui renforcent considérablement leur ténacité et autorisent l'utilisation de l'arrosage. Les céramiques à whiskers sont idéales pour l'usinage des alliages à base nickel.
(3) Les céramiques au nitrure de silicium(Si3N4) sont un autre groupe de nuances de coupe céramique. Leurs cristaux allongés les renforcent et leur confèrent une ténacité élevée. Les nuances au nitrure de silicium conviennent à l'usinage des fontes grises, cependant leur manque de stabilité chimique limite leur utilisation dans d'autres matières.
Les nuances Sialon(SiAlON) combinent la résistance des céramiques avec un réseau de nitrure de silicium auto renforçant et une stabilité chimique importante. Les nuances sialon sont idéales pour l'usinage des superalliages réfractaires.
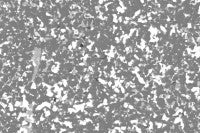
(1) Céramiques mélangées
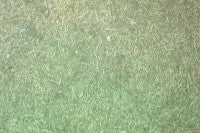
(2) Céramiques renforcées de fibres (Whiskers)
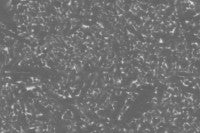
(3) Céramiques au nitrure de silicium
Applications
Les nuances céramique conviennent à une grande variété d'applications et de matières. Les applications les plus courantes sont le tournage à grande vitesse, mais ces nuances conviennent aussi à l'usinage de gorges et au fraisage. Les propriétés spécifiques des nuances céramique autorisent une productivité élevée si elles sont appliquées correctement. Les applications et la mise en œuvre des nuances céramiques à bon escient sont des critères importants pour la réussite.
Les limites générales des céramiques incluent la résistance aux chocs thermiques et la ténacité.
Matériau de coupe nitrure de bore cubique polycristallin
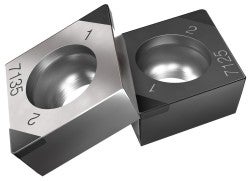
Qu'est-ce que le nitrure de bore cubique polycristallin ?
Le nitrure de bore cubique polycristallin (CBN) est un matériau de coupe qui possède une très grande résistance à la chaleur et peut être utilisé à de très grandes vitesses de coupe. Il possède aussi une bonne résistance aux chocs thermiques et une ténacité élevée.
Les nuances CBN modernes sont des matériaux composites à base de céramique avec une teneur en CBN de 40 à 65 %. Le liant céramique augmente la résistance à l'usure du CBN qui serait sujet à l'usure chimique autrement. Un autre groupe de nuances est constitué par les nuances à forte teneur en CBN, de l'ordre de 85 à presque 100 %. Ces nuances peuvent contenir un liant métallique pour améliorer leur ténacité.
Les plaquettes CBN ont un insert CBN brasé sur une plaquette en carbure cémenté. La technologie Safe-Lok™ assure la stabilité des inserts CBN sur les plaquettes négatives.
Applications
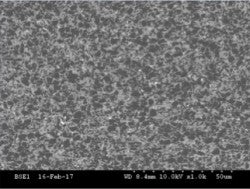
Les nuances CBN sont très utilisées pour le tournage de finition des aciers trempés d'une dureté supérieure à 45 HRc. Pour les matières d'une dureté supérieure à 55 HRc, le CBN est le seul matériau de coupe capable de remplacer les méthodes traditionnelles de rectification. Dans les aciers plus doux, d'une dureté inférieure à 45 HRc, la résistance à l'usure du CBN est moins bonne en raison de la présence d'une plus grande quantité de ferrite dans la matière.
Le CBN s'utilise aussi pour l'ébauche des fontes grises à grande vitesse, tant en tournage qu'en fraisage.
Matériau de coupe diamant polycristallin
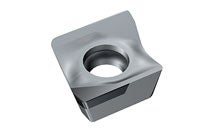
Qu'est-ce que le diamant polycristallin ?
Le diamant polycristallin ou PCD est un matériau composé à partir de particules de diamant liées avec un liant métallique. Le diamant est le plus dur de tous les matériaux, et donc le plus résistant à l'usure par abrasion. Il offre une bonne résistance à l'usure mais il manque de stabilité chimique à haute température ; en outre, il se dissout facilement dans le fer.
Applications
Les outils PCD sont réservés aux matières non ferreuses telles que les aluminiums à forte teneur en silicium, les matériaux composites à matrice métallique (MMC) et les plastiques renforcés à la fibre de carbone (CFRP). Le PCD peut aussi être utilisé pour la super finition du titane avec arrosage abondant.
Nuances Sandvik Coromant
Les plaquettes et nuances de coupe Sandvik Coromant sont décrites ici.
Vous trouverez dans cette rubrique toutes les informations nécessaires pour choisir les plaquettes et nuances en fonction de l'application.