Machining a gear wheel
Challenge: Reduce the cycle time for machining a gear wheel.
Result: InvoMilling™ with CoroMill® 162, supported by roughing with CoroMill® 331, shortened the machining time considerably.
One of our customers, a company that produces gear wheels, had previously used end-milling process with non-profiled solid carbide end mills for creating the involute profile of the gear teeth. Since machining gears with end mills requires many passes, the method is rather inefficient. The company contacted Sandvik Coromant representatives in order to apply a more productive machining method.
The combination of application knowledge, the latest machining techniques and specialized tools provided a time-saving solution. By using InvoMilling for creating the involute form of the gear teeth, the complete gear wheel could be machined in a much shorter time than before.
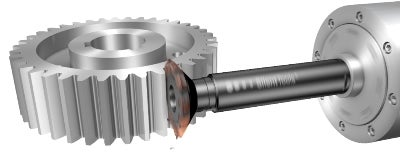
Component | Gear wheel, spur gear |
Workpiece material | Steel, AISI 1045, P1.2.Z.AN |
Module, mm (DP) | 12 (4.23) |
Number of teeth, z | 38 |
Tip diameter, da, mm (inch) | 480.13 (18.902) |
Face width, b, mm (inch) | 140 (5.512) |
46%
SHORTER
MACHINING
TIME
Results | InvoMilling solution | End-milling solution | ||
Cutter body: 162-140Q32-60 Insert: 176M60-150612E-PM 1030 | ||||
Cycle time, hours | 3.75 | 7 |
