Dişli üretimi

Dişliler nasıl üretilir?
Değişen dişli üretimi ortamında, en verimli ve hassas işleme yönteminin ve dişli takımının seçilmesi çok önemlidir. Parça, üretim süreçleri ve parti boyutları takımın ve dişli üretimi yönteminin seçimini belirler.
Dişli üretimi, genelde dar boyut toleransları elde etmede zorluk yaşanan yumuşak kademe işlemi sırasında gerçekleştirilir. Sertleştirilmiş kademe için dikkatli bir hazırlık daha sorunsuz sert parça tornalama işlemi sağlar ve ardından dişlilerde sert işleme yapılır. Sert parça tornalamada öngörülebilir işleme ve iyi yüzey ince işlemesi esastır. Bütün bunlar düşük maliyet ile birleştirilmelidir.
E-mobilite, yeni iletim tasarımı ve aynı anda hem esneklik hem de verimlilik ihtiyacı nedeniyle dişli işleme süreci, büyük ölçüde değişecek. Odak, yaygın konvansiyonel dişli takım tezgahlarından uzaklaşacak, bunun yerine, dişli/kama parçalarının çok amaçlı işlemesi norm haline gelecektir. Sıyırarak şekillendirme yöntemi, vargelleme, broşlama ve kama haddelemenin yerini aldığı için bir dereceye kadar azdırma işlemi ile birlikte odaklanacaktır.Dişli kalitesi
Dişliler genelde işlemeden sonra dişli çarklar için standart tolerans koşullarına göre sınıflandırılır. Silindirik dişli sınıflandırmasında en yaygın standart DIN 3962'dir ve farklı dişli parametreleri ölçülür ve 1–12 ölçeğinde sınıflandırılır. Müşteriye özgü başka standartlar da yaygındır, ancak bunlar DIN 3962 standardıyla aşağı yukarı aynı değerlendirme parametrelerini kullanır.
Dişli kalitesi sınıfı genel olarak parça ihtiyaçlarına göre belirlenir ve dişli çarkın uygulama alanına bağlıdır.
İyi dişli kalitesi için diğer koşullar:
- Yüksek kaliteli takımlar
- Temiz temas yüzeyleri
- Takım ve iş parçasında minimum salgı
- Stabil bağlama
- Hassas ve stabil tezgah
Dişli üretimi nasıl uygulanır
Dişli takım profilinin genelde özel dişli çarklara göre üretilmesi gerekir. Yani, diş boşluğunun boyutu ve şekli takım ile tamamen eşleşmelidir.
Bir dişli frezeleme takımı siparişi verirken dikkat edilmesi gereken önemli noktalar:
- Modül boyutu
- Basınç açısı
- Dişli diş profili (tümsek, uç boşluğu veya uç pahı)
- Dişli tepesi değişiklik faktörü
- Uç ve kök çapı
- Helis açısı
- Dişli kalite koşulları
- Olası takım çap aralığı (min-maks.)
- Bağlama tipi ve boyutu
Eksiksiz bir dişli çark çözümü tercih edilir ve gereken tüm bilgileri sağlar.
Dişli üretimi yöntemleri
Yeni kesme teknolojileri ile birlikte, dişli üretim çalışmalarında yakın zamanda değişiklikler olacaktır. Teknolojideki bu değişime üreticilerin vereceği tepki geleceğin rekabet yapısını belirleyecektir.
- InvoMilling™
- Sıyırarak şekillendirme yöntemi
- Küçük ve orta hacimli boyutlar için disk kesme
- Dişli azdırma
InvoMilling™
InvoMilling™ nedir ?
Dişli işleme, genelde ilgili dişli profili için özel takımlar gerektirir. InvoMilling ™, dış dişlileri, kamaları ve düz konik dişlileri işleme işlemidir ve standart tezgahlarda kurum içi frezeleme sağlar. Takımı değiştirmek yerine CNC programını değiştirerek, birçok dişli profili için bir takım seti kullanılabilir. Çok amaçlı tezgahlar ya da beş eksenli işleme merkezleri kullanılarak tüm parçalar tek bir kurulumda işlenebilir, böylece InvoMilling™ tedarik sürelerini kısaltabilir ve toplam üretim süresini önemli ölçüde kısaltabilir.InvoMilling™ avantajları
- Esneklik – farklı dişli profilleri için aynı takımlar
- Çok amaçlı tezgahlarda ve beş eksenli işleme merkezlerinde dişli işleme
- Tek bir tezgahta ve tek kurulumda tüm parçalar
- Daha fazla çevre dostu - kuru çalışır, kesim yağı kullanmaz
InvoMilling™ işlemi ne zaman kullanılmalı
- Çiftli helisel dişliler, balıksırtı dişliler ve düz konik dişliler ile dış dişli ve kama işleme
- Özel takımlara veya tezgahlara ihtiyaç duyulmadan dişli parçaların üretilmesi gerektiğinde
- Kısa tedarik süreleri çok önemli olduğunda
- Serbest yüzey düzeltmeli veya düzeltmesiz olarak kullanılabilir
- Modül aralığı: 0,8‒100
- Kabadan inceye talaş işlemleri için
- Küçük ve orta boy partiler için
InvoMilling™ nasıl uygulanır
Filmi izleyin ve InvoMilling™ CAD/CAM yazılımıyla üç kolay adımda nasıl tamamlanmış bir CNC programı oluşturulacağını görün:
- Parça çiziminizden dişli verilerini aktararak dişli geometrinizi tanımlayın.
- İşleme stratejinizi seçin, kaba ve ince işleme operasyonlarını ekleyin ve takım kütüphanesinden kullanılacak takımları seçin.
- Tezgahınız için CNC programı oluşturmadan önce işleme prosesini simüle edip takım yollarını doğrulayın.
Sıyırarak şekillendirme yöntemi
Sıyırarak şekillendirme nedir?
Sıyırarak şekillendirme yöntemi, vargellemeye göre birkaç kat daha hızlı ve broşlamaya göre daha esnek bir sürekli kesim işlemidir. Power Skiving bir konsept olarak yaklaşık yüz yıldır biliniyor olsa da, geliştirilmesi için yeni adımlar atılması yakın zamanda olmuştur. Daha güçlü ve rijit tezgahlarda ve senkronize iş millerinde görülen hızlı gelişmenin sonucunda, power skiving artarak yaygınlaşmaktadır.
Power Skiving hem iç, hem de dış dişlilere ve kamalara uygulanabilir; ancak bu yöntem, delik işleme konusunda özellikle verimlidir. Kısa tedarik süresinin karar vermede belirleyici olduğu seri üretimde bu yöntem daha da avantaj sağlar. Küçük ile orta adetlerdeki üretim için esnek InvoMilling™ teknolojisi önerilir.Sıyırarak şekillendirme yönteminin avantajları
- Üretim süresini kısaltan, kaliteyi artıran ve taşıma ve lojistik maliyetlerini azaltan tek bir kurulumla işleme
- Parça tasarımında daha fazla özgürlük sağlayan kenarlara yakın işleme yeteneği
- Çevre ve operatör dostu
- Kuru koşullarda çok verimli çalışır
- Broşlama, vargelleme ve azdırma işlemlerine kıyasla önemli ölçüde azaltılmış toplam üretim süresi
- Yönetilebilir ve öngörülebilir parça işleme
- Elde edilen parça kalitesi eşdeğer dişli frezeleme çözümleriyle eşit ve hatta onlardan daha iyi düzeydedir
- Özel tezgahlar, çok amaçlı tezgahlar ve işleme merkezlerinde uygulanabilir
Sıyırarak şekillendirme işlemi ne zaman kullanılmalı
- İç ve dış dişliler ile kamalar
- Silindirik alın dişlileri ve helisel dişliler
- Kaba talaş işlemeden ince talaş işlemeye
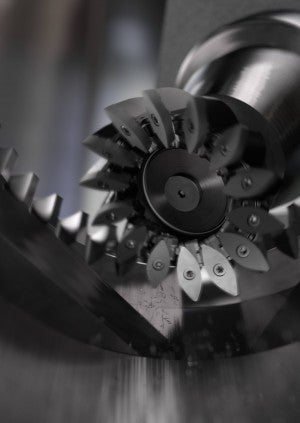
Disk kesme
Disk kesme nedir?
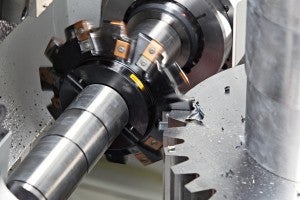
Disk kesimi, bir seferde bir diş boşluğunun kesildiği bir süreçtir. Disk kesme yöntemleri, işleme merkezlerine, çok amaçlı tezgahlara ve tornalama merkezlerine kolaylıkla uygulanır ve böylece tezgah tek bir kurulumla parçaları eksiksiz olarak işleyebilir. Azdırma tezgahlarında yapılan veya taşeron sistemiyle üretilen kamaları, disk kesme teknolojisi kullanılarak kurum içi mevcut tezgahlarınızla işleyebilirsiniz. Böylece, disk kesme büyük bir başlangıç yatırımı gerektirmez.Disk kesme avantajları
- İşleme merkezlerinde, çok amaçlı tezgahlarda ve tornalama merkezlerinde kama frezeleme
- Düşük yatırım maliyetleri
- Azdırma tezgahı yatırımı yerine mevcut tezgahlarda kama işleme
- Lojistik için daha az zaman ve maliyet
- Tezgahlar ve imalathaneler arasında parçaları taşımanıza gerek yoktur
- Yüksek hız çeliği (HSS) takımları tekrar bilemenize ve tekrar kaplamanıza gerek yoktur
- Yüksek kesme hızları
- Zor malzemeleri kesme yeteneği
- Kuru işleme; tedarik sürelerini ve kesme sıvısı maliyetlerini ortadan kaldırarak daha çok çevre ve çalışan dostu bir ortam sunar
- Küçük ve orta parti büyüklükleri için maliyet tasarruflu çözüm
Disk kesme işlemi ne zaman kullanılmalı
- Dış kamalar
- Kaba talaş işlemeden ince talaş işlemeye
- Tüm tezgah tipleri
- Kuru işleme
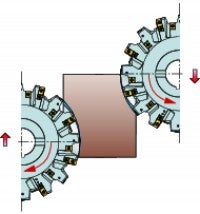
Aşağı/eş yönlü frezeleme
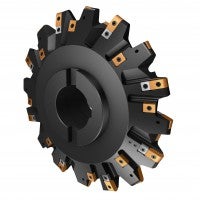
Yukarı/ters yönlü frezeleme
Dişli azdırma
Dişli azdırma nedir?
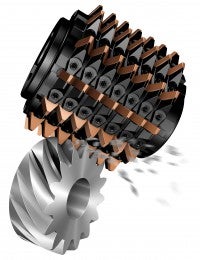
Azdırma, dişli dişlerinin bir helisel kesici takımı kullanılarak bir dizi kesimle üretildiği bir dişli üretim işlemidir. Tüm dişler kesilene kadar azdırma bıçağı ve dişli boşluğu sürekli olarak döndürülür. Azdırma işlemi sadece dış dişliler için kullanılır.Dişli azdırmanın avantajları
- HSS takımlara göre dişli çark başına daha düşük toplam maliyet
- Yüksek kesme hızları
- Daha uzun takım ömrü, düşük duruş süresi
- Kolay ve tekrarlanabilir takım indeksleme ve uygulama
- İlave yeniden taşlama veya yeniden kaplama maliyeti yoktur
Dişli azdırma işlemi ne zaman kullanılmalı
- Kaba talaş işleme, yarı ince talaş işleme, ince talaş işleme
- DIN 3972-2'ye göre dişli profilleri
- Modül aralığı: 3–10
- Azdırma tezgahları, çok-amaçlı tezgahlar, 5 eksenli tezgahlar
Dişli azdırma nasıl uygulanır?
- Her diş farklı talaşı keser. Takım ömrü en ağır kesimlerle ve en kalın talaşlarla sınırlıdır. Talaş kalınlığını değerlendirmek için maksimum talaş kalınlığını (hex) hesaplayın ve eksenel ilerleme hızını belirleyin. Maksimum talaş kalınlığı Hoffmeister denklemiyle hesaplanır
- Önerilen maks. hex = 0,18–0,22 mm (0,007–0,009 inç)
- Takım ömrünü uzatmak için mümkünse takım kaydırma yöntemi uygulayın
- Karbür takımlarla kuru frezelemeyi tercih ederseniz ıslak frezelemeye göre daha uzun takım ömrü elde edersiniz
- Mümkünse aşağı/aynı yönlü frezeleme ile takım ömrünü uzatın
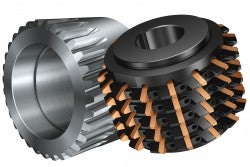