穴とキャビティ/ポケットのフライス加工
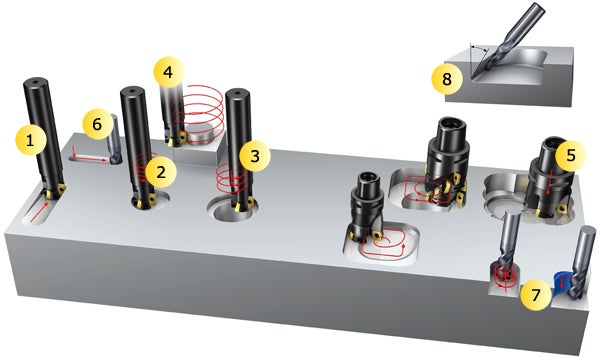
- 2軸ランピング加工
- ヘリカル加工
- コンタリング加工
- 外径ヘリカル加工またはランピング加工
- プランジ加工
- ペックドリリング加工
- スライス加工法
- 閉鎖ポケットまたは閉鎖角
穴のフライス加工:開口部の作成
- 中実ワークでの開口部の作成
- 穴またはキャビティの拡張
- キャビティまたはポケットの加工/拡張
中実ワークでの開口部の作成
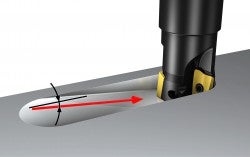
ランピング加工
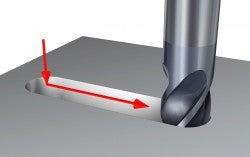
ペックドリリング加工
溝の作製
穴のフライス加工時には常に、ペックドリリング加工よりランピング加工 (2軸同時) が推奨されます。
ペックドリリング加工は、ランピング加工に代わる方法ですが、多くの場合、長い切りくずが生成され、望ましくない切削抵抗がカッターに生じます。
穴またはキャビティの作製
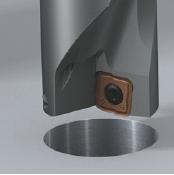
穴あけ加工
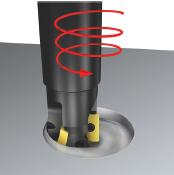
ヘリカル加工
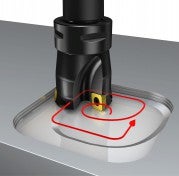
キャビティのランピング加工
穴あけ加工は、穴をあけるための最も速い従来の方法ですが、被削材によっては切りくず処理が困難で、さまざまな加工径および丸穴以外の穴に柔軟に対応できません。
ヘリカル加工(3軸同時) は、ドリル加工よりも生産性が低い方法ですが、以下の場合の代替方法として適している場合があります。
- 機械の動力に制限がある場合の大径穴加工
- 製造個数の少ない場合。径が25 mmを超える場合の一般測フライス加工のコスト効率が高いのは約500穴まで
- さまざまなサイズの穴を加工する場合
- 工具マガジンスペースが限られており、多くのサイズのドリルを保管できない場合
- 平らな底が必要な場合の止まり穴の作成
- 非剛性の薄壁部品
- 断続加工
- 切りくず処理と切りくず排出に問題があるために穴あけが困難な被削材
- 切削油が使用できない場合
- キャビティ/ポケット (「非丸穴」) のフライス加工時
加工方法の選択 - 例
キャビティ/ポケットの作製
![]() ![]() | ||
穴あけ加工とヘリカル加工 ![]() ![]() | 穴あけ加工とプランジ加工 ![]() ![]() | ヘリカル加工 ![]() |
長所 + 非丸穴用の高い切りくず排出率 + 航空宇宙産業の構造フレーム部品の第一推奨 短所 - 安定した機械が必要 - 切りくず排出 - 横型機械 - 慎重なプログラミングが必要 | 長所 + 突出し量が長い場合の問題を解決 + 簡単なプログラミング、旧式/多スピンドル機械に適合 短所 - 少ない切りくず排出量 | 長所 + 工具の削減 (ドリルが不要) + 柔軟性 (さまざまなサイズを生産) + 切削油が不要 = 開放型機械に適している + すべてのマシンコンセプトと構造に適合 短所 - 大きなキャビティでは生産性が低下 |
ポケット加工の第一推奨 | 長い工具突出し量での加工の 解決オプション | 3Dキャビティ加工の第一推奨 |
穴またはキャビティの拡張
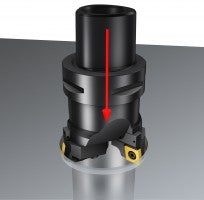
ボーリング加工
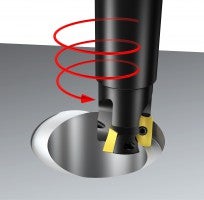
ヘリカル加工
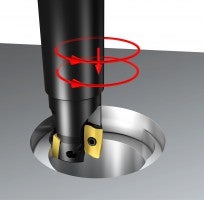
コンタリング加工
穴の拡張
ボーリング加工は通常、穴あけ加工と同じ理由により、最も速い方法ですが、穴フライス加工の方が適している場合もあります。2つのフライス加工法、ヘリカル加工 (3軸) とコンタリング加工 (2軸) を代わりに使用できます。ヘリカル加工は、穴の深さが切込み (ap) 最大値より深い場合、またはびびりやすい加工の場合に推奨されます。さらに、特に突出し量が長い場合に、穴の真円度/同心円度が高くなります。ヘリカル加工とコンタリング加工の両方で、ワークが回転する方が、フライスカッターが円軌道で移動するより真円度が高くなります。
キャビティの拡張
内径肩削りフライス加工とプランジ加工には、初回試行穴を作製し、中実ブロックに直接キャビティをランピングした場合と比較する必要があります。
- ランピング加工 (3軸) は、必要な工具が1つで、3D形状を作製できるという利点があるため、倣いフライス加工に適しています。高送り加工 (軽量および高速) で使用すると、切削抵抗が都合良く作用するため、びびりの問題が最小限になります。
- 突出し量が長い場合や、深いキャビティの場合の問題は、多くの場合、プランジ加工により解決します
- 内径肩削りフライス加工は、プランジ加工より多くのプログラミングを必要としますが、より高速です
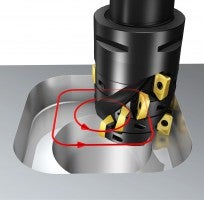
内径肩削り加工
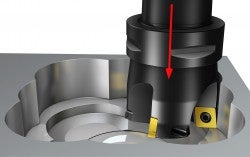
プランジ加工
プランジミリング
キャビティの荒加工の完了時に、特にコーナに取り代が残っていることがよくあります。小径カッターによるプランジ加工は、仕上げ形状に近づけるための方法の1つです。スライス加工 (軽量および高速) がコーナ加工に使用されることもよくあります。トロコイド加工は、スライス加工法の1種で、溝やポケットなどのフライス加工にも使用されます。
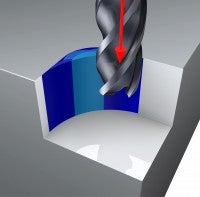
コーナのプランジ加工
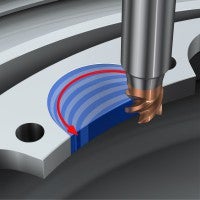
スライス加工法 – 小切込み高送り

コーナのスライス加工
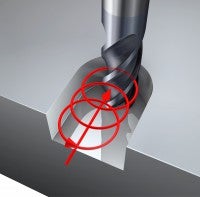
トロコイド加工
キャビティまたはポケットの加工/拡張方法
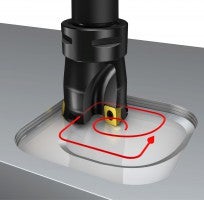
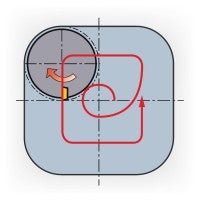
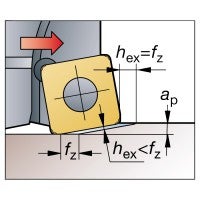
2通りの方法があります。
1. ヘリカル加工 (3軸) – 小径ap
切込角の小さいカッターを使用します。または、 丸チップカッターを使用します。
この「小切込み高送り」の加工法は、切りくず排出量が非常に多いため、機械 (ISO 40準拠) の安定性が低い場合、およびキャビティが専用形状である場合 (つまり、押し出し&射出成型) の第一推奨です。
注意:90°ショルダー部に対するすべての加工は避けてください。切込みが急激に深くなり、小さなアプローチ角のプラス効果が失われるためです。
切削条件:
- 最大カッター径 = 1.5 x ワークのコーナR
- ランピング回転方向 - 反時計回り
- 次の切削にロールイン
- 径方向切込み - 最大 ae = 70% DC
- 丸チップカッターの軸方向切込み、25% iC
- コーナのツールパスR = DC
- コーナの送りを下げる
2. 内周肩削りフライス加工 (2軸) – 大径ap
穴をあけた後、ショルダーエンドミルまたはロングエッジカッターに交換します。一般的な適用範囲は、航空宇宙産業の構造フレーム部品 (チタンの加工) です。
加工ヒント
切削が適切に排出されるようにして、切削のリカット/切削詰まりを防止してください。
- 水平スピンドル (ISO 50) を推奨します
- 高圧クーラント、またはクーラントスルーを使用する圧縮エアー
- DCは、穴径の75%以下にしてください大きな軸方向の切削を使用します (最大ae = 2 x DC)
あけた穴は、円軌道上にある必要があります。
- 径方向の食いつきを最大ae = 30 % DCに調整します
径方向の食いつきを調整して、コーナのびびりを最小限にし、生産性を最大にします。
- コーナにはできる限り大きなRを使用し、スパイラルモーフプログラミングを使用します
- できる限り大きなDCを使用し、コーナRの1.5倍以下でレストミリングを別に行います
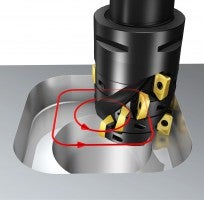
![]() ![]() | ![]() ![]() |
![]() ![]() 小さいコーナR | ![]() ![]() スパイラルモーフプログラミング |